Резьбовое соединение
Номер патента: 24917
Опубликовано: 30.11.2016
Авторы: Пинель Элит, Гард Эрик, Пети Микаель, Гуидер Мохамед
Формула / Реферат
1. Резьбовой трубчатый компонент для бурения или эксплуатации углеводородных скважин с резьбовой зоной (3; 4), расположенной на одном из его концов (1; 2) на наружной или внутренней периферийной поверхности, отличающийся тем, что по меньшей мере часть конца (1; 2) покрыта по меньшей мере одной сухой пленкой (12), имеющей твердость по шкале Шора D больше 50 и включающей матрицу из полиуретана и полимочевины, в которой количество уретановых функциональных групп преобладает над количеством мочевинных функциональных групп при соотношении по меньшей мере 55 вес.%.
2. Резьбовой трубчатый компонент по п.1, отличающийся тем, что матрица на основе полиуретана и полимочевины получена из мономера полиольного типа с высоким молекулярным весом, средства удлинения цепи и свободных ароматических изоцианатов, которые могут быть отверждены путем полиприсоединения с применением влаги.
3. Резьбовой трубчатый компонент по п.2, отличающийся тем, что матрица на основе полиуретана и полимочевины включает
многофункциональный изоцианатный форполимер с количеством функциональных групп по меньшей мере 2, полученный из смеси полиолов на основе полиэфира, полибутадиена или гидроксилированного сложного полиэфира с молекулярной массой в диапазоне от 300 до 6000 г/моль и ароматических изоцианатов дифенилметандиизоцианатного типа в избытке;
сореагент моно- или бис-оксазолидонного типа для инициации реакции и разбавления форполимера;
алифатическое полиизоцианатное отверждающее средство гексаметилендиизоцианатного типа для поддержания отверждения;
катализатор для форполимера типа простого диморфолинодиэтилового эфира или лаурата дибутилолова;
пластификатор для контроля пенообразования во время формирования пленки, в частности, триэтиленфосфатного типа.
4. Резьбовой трубчатый компонент по п.3, отличающийся тем, что матрица на основе полиуретана и полимочевины включает поглотитель влаги для стабилизации форполимера при хранении путем захвата остаточной воды, при этом указанный поглотитель влаги относится к п-толуолсульфонилизоцианатному, триметилортоформиатному или триметилортоацетатному типу.
5. Резьбовой трубчатый компонент по п.3 или 4, отличающийся тем, что матрица на основе полиуретана и полимочевины включает поглотитель СО2 кальцийоксидного или магнийоксидного типа для контроля вспенивания и образования пузырей во время реакции.
6. Резьбовой трубчатый компонент по п.1, отличающийся тем, что матрица на основе полиуретана и полимочевины получена из смеси термоплавких полиолов и полиаминов с низким молекулярным весом, которые могут быть отверждены путем поликонденсации с применением алифатического полиизоцианата.
7. Резьбовой трубчатый компонент по п.6, отличающийся тем, что матрица на основе полиуретана и полимочевины включает
полиольный форполимер, выбранный из полиолов на основе сложного полиэфира, полиэфира и полибутадиена с молекулярной массой в диапазоне от 300 до 6000 г/моль, отвержденный с применением алифатического полиизоцианата (компонента А);
термоплавкий полиамин с количеством функциональных групп 2 или более и с молекулярной массой в диапазоне от 168 до 600 г/моль, в частности 4,4'-метилен-бис-(2-хлоранилин); а также
алифатическое полиизоцианатное отверждающее средство гексаметилендиизоцианатного типа в избытке.
8. Резьбовой трубчатый компонент по одному из пп.1-7, отличающийся тем, что матрица на основе полиуретана и полимочевины дополнительно включает по меньшей мере один твердый смазочный материал в качестве снижающего трение средства, выбранный из категории твердых смазочных материалов класса 1, 2, 3 или 4, в соотношении в диапазоне от 5 до 30 вес.%.
9. Резьбовой трубчатый компонент по п.8, отличающийся тем, что твердый смазочный материал выбран из
твердого смазочного материала из класса 2 типа Bi2S3;
твердого смазочного материала из класса 4 типа PTFE
и их комбинации.
10. Резьбовой трубчатый компонент по одному из пп.1-9, отличающийся тем, что матрица на основе полиуретана и полимочевины дополнительно включает ингибитор коррозии.
11. Резьбовой трубчатый компонент по одному из пп.1-10, отличающийся тем, что вся резьбовая зона (3; 4) покрыта сухой пленкой (12).
12. Резьбовой трубчатый компонент по одному из пп.1-11, отличающийся тем, что он содержит участок уплотнения металл/металл, причем указанный участок уплотнения покрыт сухой пленкой (12).
13. Резьбовое трубчатое соединение, содержащее трубчатый компонент с наружной резьбой и трубчатый компонент с внутренней резьбой, расположенные один в другом, отличающиеся тем, что по меньшей мере один из указанных резьбовых трубчатых компонентов является компонентом по одному из пп.1-12.
14. Способ нанесения покрытия на резьбовой трубчатый компонент для бурения или эксплуатации углеводородных скважин с резьбовой зоной (3; 4), расположенной на одном из его концов (1; 2) на наружной или внутренней периферийной поверхности, отличающийся тем, что данный способ включает следующие этапы, на которых
получают матрицу на основе полиуретана и полимочевины сухой пленки по одному из пп.1-10 в жидком состоянии;
наносят матрицу из полиуретана и полимочевины в жидком состоянии путем распыления на часть конца (1; 2) указанного резьбового трубчатого компонента и
отверждают матрицу с формированием сухой пленки (12) практически с жесткой структурой.
15. Способ по п.14, отличающийся тем, что матрица на основе полиуретана и полимочевины представляет собой матрицу сухой пленки по одному из пп.2-5.
16. Способ по п.15, отличающийся тем, что отверждение сухой пленки инициируют воздействием относительной влажности (RH) по меньшей мере 60% при температуре по меньшей мере 20°С необязательно с последующей сушкой.
17. Способ по п.16, отличающийся тем, что сушку проводят в инфракрасной или конвекционной сушильной печи, обеспеченной водяным паром.
18. Способ по п.14, отличающийся тем, что матрица на основе полиуретана и полимочевины представляет собой матрицу сухой пленки по одному из пп.6, 7.
19. Способ по п.18, отличающийся тем, что сухую пленку отверждают с помощью двухкомпонентного распыляющего устройства с внешним смешиванием отвердителя.
20. Способ по п.19, отличающийся тем, что отверждение сухой пленки сопровождается горячей сушкой или операцией дополнительного отверждения при температуре 90°С.
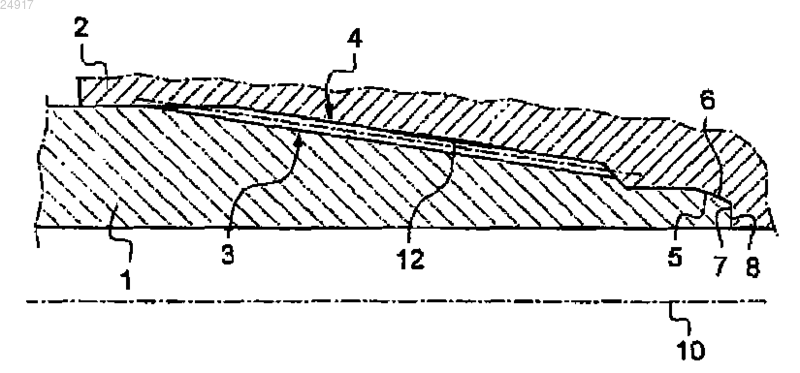
Текст
Настоящее изобретение относится к резьбовому трубчатому компоненту для бурения или эксплуатации углеводородных скважин, причем указанный трубчатый компонент имеет на одном из своих концов (1; 2) резьбовую зону (3; 4), расположенную на его наружной или внутренней периферийной поверхности в зависимости от того, относится ли резьбовой конец к типу с наружной или внутренней резьбой, в котором по меньшей мере часть конца (1; 2) покрывается по меньшей мере одной пленкой из полиуретана (12) на 100% в твердой фазе, по сути, с жесткой структурой, на основе матрицы из полиуретана и полимочевины, в которой количество уретановых функциональных групп преобладает над количеством мочевинных функциональных групп при соотношении по меньшей мере 55 вес.%.(71)(73) Заявитель и патентовладелец: ВАЛЛУРЕК МАННЕСМАНН ОЙЛ ЭНД ГЕС ФРАНС (FR); НИППОН СТИЛ ЭНД СУМИТОМО МЕТАЛ КОРПОРЭЙШН (JP) Настоящее изобретение относится к трубчатому компоненту, используемому для бурения и эксплуатации углеводородных скважин, и, в частности, к резьбовому концу этого компонента, причем указанный конец относится к типу с наружной или внутренней резьбой и может быть соединен с соответствующим концом другого компонента для образования соединения. Кроме того, изобретение относится к способу получения стойкой к заеданию и стойкой к коррозии пленке на этом трубчатом компоненте. Под компонентом, который "используют для бурения и эксплуатации углеводородных скважин",подразумевают любой элемент, являющийся, по сути, трубчатым по форме и предназначенный для соединения с еще одним элементом такого же типа или иного, чтобы в конечном итоге образовать колонну труб для бурения углеводородной скважины, райзера или райзера для капитального ремонта, или для обсадной колонны, или насосно-компрессорной колонны, используемых при эксплуатации скважин. Кроме того, изобретение может быть применимым к компонентам, используемым в бурильной колонне,таким как бурильные трубы, утяжеленные бурильные трубы, воротники бура и части трубных соединений и утяжеленных труб, известным как замковые соединения или бурильные замки. Каждый трубчатый компонент включает один конец, имеющий зону с наружной резьбой, и/или один конец, имеющий зону с внутренней резьбой, каждый из которых предназначен для соединения свинчиванием с соответствующим концом другого компонента, причем полученная сборка образует соединение. Резьбовые трубчатые компоненты соединены при определенных нагрузках, чтобы обеспечить выполнение требований для посадки с натягом и уплотнения, выдвигаемых условиями эксплуатации, зная,что в скважине может потребоваться несколько раз свинчивать и развинчивать резьбовые трубчатые компоненты. Условия использования этих резьбовых трубчатых компонентов вызывают возникновение разных типов нагрузок, что обуславливает необходимость в использовании покрытий на чувствительных участках этих компонентов, таких как резьбовые зоны, упоры или поверхности уплотнения. Операции свинчивания обычно выполняют при высокой осевой нагрузке, например, под весом трубы длиной несколько метров, соединяемой посредством резьбового соединения, возможно с небольшим несовпадением оси соединяемых резьбовых элементов, что вызывает риски заедания в резьбовых зонах и поверхностях уплотнения металл/металл. По этой причине резьбовые зоны, несущие поверхности и поверхности уплотнения металл/металл необходимо покрывать смазочными материалами. Кроме того, резьбовые трубчатые компоненты хранят (иногда несколько лет), затем свинчивают в агрессивной среде. Примерами могут служить ситуация морского бурения с брызгами морской воды или ситуация бурения на суше, когда присутствуют песок, пыль или другие загрязняющие вещества. Таким образом, на поверхностях, которые должны взаимодействовать при свинчивании (резьбовые зоны) или тугом контакте (поверхности уплотнения металл/металл), необходимо использовать покрытия, противостоящие коррозии. Кроме того, эти поверхности необходимо обрабатывать против коррозии. Однако с экологической точки зрения оказывается, что смазочные материалы для свинчивания, отвечающие требованиям стандарта RP 5A3 API (Американского института нефти), не дают длительного решения, поскольку эти смазочные материалы, содержащие тяжелые металлы, могут быть вытеснены из трубчатых компонентов и высвобождены в окружающую среду или в скважину, приводя к закупорке,вызывающей необходимость операций по чистке. Кроме того, эти смазочные материалы должны быть применены по месту при каждой операции свинчивания. Для решения проблем обеспечения длительной коррозионной стойкости и сопротивления к истиранию и соблюдения экологических прерогатив специалисты в области техники, относящейся к резьбовым соединениям, активно разрабатывают сплошные сухие покрытия (т.е. не вязкие и не липкие, как смазочные материалы), которые являются как смазочными материалами, так и защищают от коррозии, которые можно окончательно наносить на трубчатые компоненты на заводе в конце процесса их производства, и которые затем готовы к свинчиванию. В частности, разрабатываются покрытия, являющиеся инертными по отношению к окружающей среде и которые устойчивы к износу, а также к атмосферным и климатическим условиям. Кроме того, в публикации WO 2001/070918 раскрывают способ нанесения на резьбовое соединение противозадирного покрытия, содержащего полиуретановые смолы в качестве возможных альтернативных связующих. Противозадирная функция обеспечивается с помощью органических или неорганических соединений, которые способны высвобождать газ при высоких температурах, таких как те, которые встречаются в скважине, тем самым вызывая увеличение сжимаемого свободного объема при контакте для облегчения свинчивания/развинчивания без заедания. Связующим, главным образом, является термопластичный полиуретан, одно- либо двухкомпонентный, в зависимости от реакционной способности,или в водной дисперсии. Наконец, в публикации WO 2005/045188 для трубчатого резьбового соединения "расширяемого" типа предлагают способ нанесения покрытия с жидкой или пастообразной матрицей полисульфидного типа, а также из эластомерного полиуретана, двухкомпонентного типа, который может отверждаться при комбинированном отсутствии кислорода и влаги. Характеристики деформации растяжения являются предпочтительными по сравнению с механическими характеристиками (сопротивление разрыву при растяжении, твердость, стойкость к абразивному износу, адгезионная сила), в отличие от тех, которые обеспечиваются настоящим изобретением. Настоящее изобретение основывается на открытии, которое заключается в использовании конкретных матриц на основе полиуретана или мочевины, что означает, что можно получать смазочные сухие пленки, которые обладают высокой стойкостью к износу, противозадирными свойствами, высокой механической прочностью с низким коэффициентом трения, а также стойкостью к экстремальным условиям работы углеводородной скважины. Используемые решения можно адаптировать также к различным маркам металла для соединений для вышеупомянутых трубчатых компонентов. В частности, настоящее изобретение относится к резьбовому трубчатому компоненту для бурения или эксплуатации углеводородных скважин, причем указанный трубчатый компонент имеет на одном из своих концов резьбовую зону, расположенную на его наружной или внутренней поверхности в зависимости от того, имеет ли резьбовой конец наружную или внутреннюю резьбу, при этом по меньшей мере часть конца покрыта по меньшей мере одной сухой пленкой, обладающей твердостью по шкале Шора D больше 50 и включающей матрицу из полиуретана и полимочевины, в которой количество уретановых функциональных групп преобладает над количеством мочевинных функциональных групп при соотношении по меньшей мере 55 вес.%. Ниже приведены необязательные характеристики, которые являются дополнительными или заменяющими. Матрица на основе полиуретана и полимочевины относится к однокомпонентному типу. Матрицу из полиуретана и полимочевины получают из мономера полиольного типа с высоким молекулярным весом, средства для удлинения цепи и свободных, ароматических изоцианатов, которые могут отверждаться путем полиприсоединения с применением влаги. Матрица из полиуретана и полимочевины включает многофункциональный изоцианатный форполимер с количеством функциональных групп по меньшей мере 2, полученный из смеси полиолов на основе полиэфиров, полибутадиенов или гидроксилированных сложных полиэфиров с молекулярной массой в диапазоне от 300 до 6000 г/моль и ароматических изоцианатов дифенилметандиизоцианатного типа в избытке; сореагент моно- или бис-оксазолидонного типа для инициации реакции и разбавления форполимера; алифатическое полиизоцианатное отверждающее средство гексаметилендиизоцианатного типа для поддержания отверждения; катализатор для форполимера из типа простого диморфолинодиэтилового эфира или лаурата дибутилолова; пластификатор для контроля пенообразования во время формирования пленки, в частности, триэтиленфосфатного типа. Матрица на основе полиуретана и полимочевины дополнительно включает поглотитель влаги для стабилизации форполимера при хранении путем захвата остаточной воды, при этом поглотитель влаги относится к п-толуолсульфонилизоцианатному, триметилортоформиатному или триметилортоацетатному типу. Матрица на основе полиуретана и полимочевины дополнительно включает поглотитель СО 2 из кальцийоксидного или магнийоксидного типа для контроля вспенивания и образования пузырей во время реакции. Матрица на основе полиуретана и полимочевины относится к двухкомпонентному типу. Матрицу на основе полиуретана и полимочевины получают из смеси термоплавких полиолов и полиаминов с низким молекулярным весом, которые могут быть отверждены путем поликонденсации с использованием алифатического полиизоцианата. Матрица из полиуретана и полимочевины включает форполимер полиола, выбранный из сложных полиолов на основе сложных полиэфиров, простых полиэфиров и полибутадиенов и с молекулярной массой в диапазоне от 300 до 6000 г/моль, отвержденных с помощью алифатического полиизоцианата; термоплавкий полиамин с количеством функциональных групп 2 или более, а также с молекулярной массой в диапазоне от 168 до 600 г/моль, в частности 4,4'-метилен-бис(2-хлоранилин), а также алифатическое полиизоцианатное отверждающее средство гексаметилендиизоцианатного типа в избытке. Матрица на основе полиуретана и полимочевины дополнительно включает по меньшей мере один твердый смазочный материал в качестве снижающего трение средства, выбранный из категории твердых смазок из 1, 2, 3 или 4 класса в диапазоне от 5 до 30 вес.%. Твердый смазочный материал выбирается из твердого смазочного материала из класса 2 типа Bi2S3; твердого смазочного материала из класса 4 типа PTFE и их комбинации. Матрица на основе полиуретана и полимочевины дополнительно включает ингибитор коррозии. Вся резьбовая зона покрыта полиуретановой пленкой. Резьбовой трубчатый компонент содержит поверхность уплотнения металл/металл, причем указанная поверхность уплотнения покрыта полиуретановой пленкой. Кроме того, настоящее изобретение относится к резьбовому трубчатому соединению, содержащему резьбовой трубчатый компонент с наружной резьбой и резьбовой трубчатый компонент с внутренней резьбой, выполненные один в другом, причем по меньшей мере один из указанных резьбовых трубчатых компонентов является таким, как определено выше. Кроме того, настоящее изобретение относится к способу покрытия резьбового трубчатого компонента для бурения или эксплуатации углеводородных скважин, причем указанный трубчатый компонент имеет на одном из своих концов резьбовую зону, расположенную на его наружной или внутренней поверхности в зависимости от того, имеет ли резьбовой конец наружную или внутреннюю резьбу, при этом способ включает следующие этапы, на которых получают матрицу на основе полиуретана и полимочевины, как определено выше, в жидком состоянии; наносят матрицу из полиуретана и полимочевины в жидком состоянии путем распыления частиц на конце указанного резьбового трубчатого компонента и отверждают матрицу для формирования полиуретановой пленки, по сути, с жесткой конструкцией. Дополнительные характеристики способа нанесения покрытия, которые являются дополнительными или замещающими, определены ниже. Матрица на основе полиуретана и полимочевины представляет собой однокомпонентную матрицу,как определено выше. Отверждение полиуретановой пленки инициируется путем применения относительной влажности(RH) не менее 60% при температуре не менее 20 С, необязательно с последующим высушиванием. Высушивание проводят в инфракрасной или конвекционной сушильной печи, оснащенной водяным паром. Матрица на основе полиуретана и полимочевины представляет собой двухкомпонентную матрицу,как определено выше. Полиуретановую пленку отверждают с помощью двухкомпонентного распыляющего устройства с внешним смешиванием отвердителя. После отверждения полиуретановой пленки проводят горячую сушку или операцию дополнительного отверждения при температуре 90 С. Отличительные признаки и преимущества изобретения более подробно описаны в последующем описании, которое подано со ссылками на прилагаемые графические материалы, на которых на фиг. 1 показан схематический вид соединения, полученного в результате соединения двух трубчатых компонентов свинчиванием; на фиг. 2 - схематический вид кривой свинчивания двух резьбовых трубчатых компонентов; на фиг. 3 - схематический вид подложки, покрытой смазывающей сухой пленкой; на фиг. 4 - схематический вид испытательной установки; на фиг. 5 - схематический вид другой испытательной установки; на фиг. 6 - схематический вид другой испытательной установки; на фиг. 7 и 8 - графики результатов испытаний. Резьбовое соединение, показанное на фиг. 1, содержит первый трубчатый компонент с осью вращения 10, имеющий конец 1 с наружной резьбой, и второй трубчатый компонент с осью вращения 10, имеющий конец 2 с внутренней резьбой. Оба конца, 1 и 2, каждый из которых заканчивается в концевой поверхности, ориентированной радиально относительно оси 10 резьбового соединения, соответственно имеют резьбовые зоны 3 и 4, которые взаимодействуют для взаимного соединения этих двух компонентов свинчиванием. Резьбовые зоны 3 и 4 могут быть с резьбой трапецеидального, самозапирающегося и т.д. типа. Кроме того, на концах с наружной и внутренней резьбой рядом с резьбовыми зонами 3, 4 предусмотрены, соответственно, поверхности уплотнения металл/металл 5, 6, предназначенные для вхождения в контакт с герметичным зацеплением между собой после соединения двух резьбовых компонентов свинчиванием. Наконец, конец 1 с наружной резьбой заканчивается в концевой поверхности 7, упирающейся в соответствующую поверхность 8, предусмотренную на конце 2 с внутренней резьбой, когда эти два конца свинчены. Заявитель предусмотрел и другие конструктивные исполнения, в которых упор, образованный в данном случае двумя контактными поверхностями 7 и 8, смещается самозапирающимся взаимодействием резьбовых зон 3, 4 с автоматической блокировкой (см. документы US 4822081, US RE30467 и USRE34467). Как можно видеть на фиг. 1 и 3, по меньшей мере одно из резьбовых трубчатых соединений покрыто на части своего конца 1, названной подложкой 11, пленкой 12 из полиуретана, обладающей твердостью по Шору 50 или больше, при этом она включает матрицу из полиуретана и полимочевины, в которой количество уретановых функциональных групп преобладает над количеством мочевинных функциональных групп в соотношении более 55 вес.%. Так как количество уретановых функциональных групп преобладает над количеством мочевинных функциональных групп, создается определенная жесткость и твердость пленки, что гарантирует хорошее сопротивление абразивному износу. Это преобладание количества уретановых функциональных групп над количеством мочевинных функциональных групп достигается путем целесообразного выбора определенных параметров данного способа, такого как выбор компонентов и молекулярного веса. Эти жесткие полиуретановые покрытия различаются по происхождению применяемого олигомера и отверждающего средства, а также по характеру реакции, которая происходит, степени отверждения и способу, который на 100% проходит в твердой фазе (нет ни плавления, ни диспергирования полиуретана). Согласно D.K. Chattopadhyay (Prog. Polym. Sci. 32 (2007), 352-418) две реакции обеспечивают получение жестких полиуретановых покрытий: экзотермическая реакция между диизоцианатом и гидроксил-функционализированным мономером(полиолом на основе полиэфира, сложного полиэфира, схема 1) или амин-функционализированным мономером (полиамином, схема 2) для двухкомпонентного покрытия Схема 1 экзотермическая реакция, проходящая в два этапа, начинающаяся с изоцианатфункционализированного форполимера на основе сложного полиэфира, инициированного гидратацией(схема 3) для однокомпонентного покрытия Схема 3 Первый этап включает проведение реакции изоцианатных функциональных групп с водой в условиях повышенной температуры и относительной влажности (схема 4). Схема 4 На втором этапе полиамины могут реагировать со свободными полиизоцианатами (схема 2). Таким образом, заявитель преимущественно рассматривает жесткие полиуретаны из-за их механических свойств - твердости, гибкости, жесткости под нагрузкой, но прежде всего с целью преодоления экологических ограничений, связанных с выбросами летучих органических соединений (VOC). Кроме того, полимер-полиолы с низкой молекулярной массой использовались для получения связующих с низкой вязкостью для сокращения использования органических растворителей, выделяющихVOC, но это способствовало увеличению реакционной способности и изменило связывающие продукты. Альтернативный вариант соответствует использованию сореагента на основе оксазолидина, в частности однокомпонентных полимеров, где отверждение инициируется влагой. Оксазолидины способствуют снижению вязкости как полимер-полиолов, так и полиаминных полимеров с высокой молекулярной массой, однако блокированные химические свойства аминоспирта подразумевают, что они могут инициировать и ускорить отверждение путем гидролиза гидроксильных и аминных реакционноспособных функциональных групп, подвергнутых воздействию благоприятных условий влажности. Таким образом, из существующих жестких полиуретановых покрытий заявитель обратил особое внимание на жесткие полиуретановые и полимочевинные покрытия из-за их высокой степени отверждения, которая обусловлена плотной межмолекулярной сетчатой структурой, являющейся причиной свойств твердости,коррозионной и химической стойкости, которые превосходят таковые для других марок. Одно из основных различий между жестким и мягким (или эластомерным) полиуретаном задается соотношением между изоцианат-функционализированным форполимером и полиолом и/или полиаминным полимером. Чем ближе коэффициент к 1, тем более жестким является полученное полиуретановое/полимочевинное покрытие. Одним из средств для измерения жесткости и, следовательно, степени отверждения является твердость пленки по различным шкалам (по шкале Шора D и по шкале Шора А или же твердость по карандашной шкале) с помощью дюрометра. Самая высокая твердость по Шору(50 по шкале Шора D) измеряется для показателя 1, в то время как низкая твердость по Шору (30 по шкале Шора А), соответствующая мягким или эластомерным покрытиям, измеряется для показателей менее 0,4. Заявитель был особенно заинтересован в гибридных полиуретановых/полимочевинных покрытиях,которые имеют другие преимущества, связанные с сочетанием уретановых и мочевинных функциональных групп в одном покрытии. В отличие от полиуретановой фракции в отвержденной пленке фракции полимочевины обеспечивают большую энергию когезии, термостойкость и адгезию из-за большей полярности. Полярность усиливается за счет прибавления гидрофильной части, связанной с мочевинной функциональной группой. Во время выполнения способа фракцией полимочевины обеспечивается покрытие с гибкостью и относительной нечувствительностью к влаге в отличие от одной только полиуретановой системы. Так как кинетика реакции между аминными функциональными группами и изоцианатом является более предпочтительной по сравнению с кинетикой реакции между гидроксильными функциональными группами и изоцианатом, вспенивание полимочевинных систем или систем, включающих полимочевины, по сути, невозможно. Во всех других случаях, в частности, если присутствует катализатор реакции,пенообразование может привести к снижению плотности сети, пористости и худшим эксплуатационным свойствам. Матрица, приведенная выше, может быть либо матрицей однокомпонентного типа, либо матрицей двухкомпонентного типа. Однокомпонентную полиуретановую матрицу получают из мономера полиольного типа с высоким молекулярным весом, средства удлинения цепи и свободных ароматических изоцианатов, которые могут быть отверждены путем полиприсоединения посредством влаги. Так, например, однокомпонентная матрица может включать многофункциональный изоцианатный форполимер с количеством функциональных групп по меньшей мере 2, полученный из смеси полиолов на основе полиэфира, полибутадиена или гидроксилированного сложного полиэфира с молекулярной массой в диапазоне от 300 до 6000 г/моль и ароматических изоцианатов дифенилметандиизоцианатного типа в избытке; сореагент моно- или бис-оксазолидонного типа для инициации реакции и разбавления форполимера; алифатическое полиизоцианатное отверждающее средство гексаметилендиизоцианатного типа для поддержания отверждения; катализатор для форполимера типа простого диморфолинодиэтилового эфира или лаурата дибутилолова и пластификатор для контроля пенообразования во время формирования пленки, в частности, триэтиленфосфатного типа. Данная однокомпонентная матрица может дополнительно включать поглотитель влаги для стабилизации форполимера при хранении посредством захвата остаточной воды, в частности птолуолсульфонилизоцианатного, триметилортоформиатного или триметилортоацетатного типа. При необходимости она может также включать СО 2 поглотитель из кальцийоксидного или магнийоксидного типа для контроля вспенивания и образования пузырей во время реакции. Двухкомпонентную полиуретановую матрицу получают из смеси термоплавких полиолов и полиаминов с низким молекулярным весом, которые могут быть отверждены путем поликонденсации с использованием алифатического полиизоцианата. Так, например, двухкомпонентная матрица может включать форполимер полиола, выбранный из полиолов на основе полиэфира, полибутадиена и гидроксилированного сложного полиэфира с молекулярной массой в диапазоне от 300 до 6000 г/моль; термоплавкий полиамин с количеством функциональных групп от 2 или более и с молекулярной массой в диапазоне от 168 до 600 г/моль, в частности 4,4'-метилен-бис(2-хлоранилин), а также алифатическое полиизоцианатное отверждающее средство гексаметилендиизоцианатного типа в избытке. Матрица в настоящем изобретении может также содержать частицы твердого смазочного материала по меньшей мере одного из классов 1, 2, 3 и 4, в соотношении по весу в диапазоне от 5 до 30%. Предпочтительно указанный твердый смазочный материал выбирается из твердого смазочного материала из класса 2 типа BI2S3, твердого смазочного материал из класса 4 типа PTFE, а также их комбинации. Выражение "твердый смазочный материал", как применяется в данном документе, означает твердое и устойчивое тело, которое при помещении между двумя поверхностями трения может уменьшить коэффициент трения и уменьшить износ и повреждение этих поверхностей. Данные тела могут разбиваться на разные категории, определяемые их функциональным механизмом и их структурой, а именно класс 1:твердые тела, смазывающие свойства которых обусловлены их кристаллической структурой, например графит, оксид цинка (ZnO) или нитрид бора (BN); класс 2: твердые тела, смазывающие свойства которых обусловлены их кристаллической структурой, а также реакционным химическим элементом в их составе, например дисульфид молибдена MoS2,фторид графита, сульфиды олова, сульфиды висмута, дисульфид вольфрама или фторид кальция; класс 3: твердые тела, смазывающие свойства которых обусловлены их химической реакционной способностью, например некоторые химические соединения типа тиосульфата или Desilube 88, продаваемый компанией Desilube Technologies Inc.; класс 4: твердые тела, смазывающие свойства которых обусловлены пластическим или вязкопластическим поведением под действием силы трения, например политетрафторэтилен (PTFE) или полиамиды. В матрице также могут быть включены другие добавки, такие как, например, ингибиторы коррозии. Способ нанесения покрытия согласно настоящему изобретению включает в основном распыление полиуретановой пленки в жидком состоянии на резьбовой трубчатый компонент с последующей ее полимеризацией, это означает, что покрытие может быть получено с высокими вязкостными свойствами,стойкостью к истиранию и адгезионными свойствами. Данная жесткая полиуретановая пленка с твердостью по Шору D больше 50, полученная с помощью матрицы из полиуретана и полимочевины, не включает и не требует добавления растворителя или разбавителя. Способ нанесения покрытия может быть быстро осуществлен на любой наружной или внутренней части трубчатого компонента. Настоящее изобретение может быть преимущественно использовано для замены акриловоэпоксидного покрытия, отвержденного посредством ультрафиолетового света на наружной части соединения, тем самым обеспечивая лучшее или эквивалентное скольжение, производительность и защиту от коррозии с помощью жесткого однокомпонентного полиуретана. Кроме того, изобретение означает, что коэффициенты трения менее 0,06 могут быть получены независимо от давления и зоны резьбы с помощью жесткого двухкомпонентного полиуретана, и, следовательно, могут быть получены относительно низкие значения крутящего момента при действии. Лучшая твердость жестких полиуретановых покрытий направлена на модель трения посредством скольжения при контакте для увеличения долговечности покрытия, в отличие от других покрытий, которые являются хрупкими даже при низких нагрузках. Заявитель предпочтительно выбрал для выполнения осаждение распылением, т.е. способ, который на 100% проходит в твердой фазе, матрицы из полиуретана, полимочевины с жесткой структурой, связанной с высокой твердостью однокомпонентные полиуретановые матрицы, полученные путем полиприсоединения посредством инициирования под воздействием влаги; двухкомпонентные полиуретановые матрицы, полученные путем поликонденсации. Реакция отверждения однокомпонентной пленки инициируется при относительной влажности (RH) выше 60% при 20 С. За ней может следовать сушка. Скорость отверждения повышается с увеличением уровня влажности и температуры. В случае однокомпонентной пленки начальное отверждение для получения сухого покрытия может быть осуществлено в два этапа. Первый этап включает в себя следующие операции, на которых применяют минимальную относительную влажность (RH) 70% в течение 10 мин при 30 С или применяют относительную влажность (RH) 70% в течение 10 мин при 90 С. Второй этап включает в себя следующие операции, на которых осуществляют сушку в печи при 80 С в течение 2 ч либо осуществляют сушку в печи при 130 С в течение 15 мин. Пленка становится сухой на ощупь через 25 мин после отверждения. Во всех случаях после охлаждения отверждение проводят при относительной влажности и при температуре окружающей среды в воздухе так, что оно завершается минимум через 24 ч. Кроме того, не существует, по сути, никаких рисков незамедлительного появления коррозии или быстровозникающего ржавления во время этапа сушки, так как достаточно гидрофильного характера изоцианата, который находится немного в избытке, чтобы вода не оказалась уловленной в виде пара или в конденсированном виде в качестве границы раздела фаз между сформированным покрытием и подложкой. Вся остаточная вода вступает в реакцию с изоцианатными функциональными группами посредством гидролиза для поддержания полимеризации до конца отверждения. Сушку можно проводить в инфракрасной или конвекционной сушильной печи. Печь при необходимости может быть снабжена подачей водяного пара посредством генератора контролируемой влажности. Отверждение двухкомпонентных пленок происходит гораздо быстрее. Поскольку время отверждения может составлять менее 2 мин при температуре окружающей среды, отверждение осуществляется с использованием двухкомпонентной распылительной системы, например, такой, которую предлагаютWalther или Devilbiss, с нагнетателем с внешним смешиванием отвердителя. Он используется путем взаимодействия полиольного и/или полиаминного соединения А и соединения или отвердителя В в жидком состоянии в соотношении в диапазоне от 1,07 до 1,12. Горячая сушки или дополнительное отверждение при температуре 90 С непосредственно после нанесения может увеличить скорость отверждения и позволить избежать реакционной активности по отношению к влаге в окружающем воздухе. Заявитель провел определенное количество оценочных испытаний. Водостойкие свойства оценивались с помощью ускоренных испытаний на воздействие влажных условий, а трибореологические свойства сформированного материала или смазочного покрытия определялись с помощью испытания царапаньем для определения значений трения и адгезии. Стойкость к истиранию оценивали с помощью трибологического испытания Фалекса в конфигурации, соответствующей таковой у соединения. Испытания на коррозию включают испытание в солевом тумане, осуществляемое в климатической камере при следующих условиях: температура 35 С с 50 г/л солевого раствора с плотностью в диапазоне от 1,029 до 1,036 при 25 С, при рН в диапазоне от 6,5 до 7,2 при 25 С и со средней скоростью восстановления 1,5 мл/ч. Образцы, которые были неповрежденными, без ржавчины, соответствуют классу ReO стандартаISO 9227 после воздействия. Способ обеспечивает средство проверки того, что сохраняется сравнительное качество металлического материала с противокоррозионным защитным покрытием или без такового(металлическое или органическое покрытие на металлическом материале). Испытания на водостойкость включают выполнение с образцами ускоренного испытания на коррозию в соответствии со стандартом DIN 50017, проводящегося в климатической камере. Данное испытание, включающее один цикл в день, заключается в осаждении водного пара путем конденсации при следующих условиях: 35 С, относительная влажность 90% в течение 8 ч, после чего допускается, чтобы образцы высохли. После 7 циклов выполняется проверка, чтобы увидеть подверглась ли коррозии подложка, защищенная сухим покрытием. Исключительная устойчивость должна соответствовать классификации в стандарте ISO 4628: отсутствие коррозии, образования пузырей, отсутствие трещин, отсутствие отслаивания хромированного покрытия или покрытия из углеродистой стали, обработанного либо механически, либо посредством фосфатирования с цинком (отложение фосфата от 8 до 20 г/м 2) или марганцем (от 4 до 16 г/м 2 фосфата). Контрольная подложка может быть также обработана электролитическим покрытием из тройного сплаваCu-Sn-Zn с промежуточным слоем Ni. Испытание погружением в воду является гораздо более серьезным, чем испытание на водостойкость по стандарту DIN 50017. Оно заключается в испытании водостойкости покрытий. Оно является производным от стандарта ASTM D870-09, связанного с промышленными и автомобильными красками. Погружение в воду может привести к разрушению покрытия. Понимание того, каким образом покрытие выдерживает погружение в воду, полезно для прогнозирования срока службы. Растрескивание или повреждение в испытании погружением в воду может быть вызвано рядом факторов, в частности, недостатком в самом покрытии, загрязнением подложки или недостаточной подготовкой поверхности. Таким образом, испытание полезно для оценки покрытий в отдельности или завершенных систем покрытий. Испытание включает погружение наполовину образца 20 в деминерализованную воду 21 сроком на 168 ч при 40 С в печи 22, как показано на фиг. 5. Адгезия, образование пузырьков, ржавчина или раковины наблюдаются визуально, указывая на чувствительность покрытия к воде. Испытание может быть продолжено последующим определением адгезии влаги с помощью испытания царапаньем. Испытание, известное как "испытание царапаньем", схематично показанное на фиг. 4, позволяет определить силу сцепления или адгезию пленки на поверхности или подготовленной поверхности. Способ, который включает сдвиг и деформацию пленки сферическим шариком, подвергающимся увеличивающейся нагрузке, также позволяет определить два основных трибологических параметра, а именно,коэффициент трения и критическую нагрузку, соответствующие появлению потери когезии пленки. Испытание особенно подходит для покрытий с моделью трения скольжения, таких как пенополиуретаны. Образцы покрывают посредством пневматического распыления. Условия отверждения для пленки являются специфичными и главным образом зависят от физико-химических характеристик связующего. В качестве условий опыта используется сферический наконечник, сформированный из сплава Inconel 718 с диаметром 5 мм, и металлический образец, сформированный из углеродистой стали ХС 48 или хромированной стали Z20C13, механической обработки поверхности или обработки поверхности посредством цинкового фосфатирования, или обработки поверхности электролитическим покрытием CuSn-Zn. Параметры являются следующими: нагрузка увеличилась от 10 до 310 Н при скорости увеличения нагрузки 15 Н/с или же нагрузка увеличилась с 250 до 750 Н при скорости увеличения нагрузки 25 Н/с для более износостойких покрытий. Скорость перемещения шарика составляла 2 мм/с в течение 20 с(длина траектории 40 мм). Измеренный коэффициент трения считается низким, если он находится в диапазоне от= 0,05 при нагрузке 10 Н до= 0,09 при нагрузке 310 Н. При нагрузке на поверхность из углеродистой стали 310 Н была измерена величина коэффициента , равная 0,07. Следует отметить, что необходимо четко задать нагрузку и рабочие условия для испытания каждого типа покрытия. Испытание адгезии методом решетчатого надреза заключается в определении сопротивления одноили многослойного покрытия отделению от подложки, когда покрытие заштриховывают путем нанесения надрезов на указанную подложку в соответствии с делением на шесть категорий. Исключительная адгезия покрытия подложки должна соответствовать классу 0 стандарта ISO 2409 (2007): идеально гладкие края надрезов, ни один из квадратов полученной решетки не отпадает. С учетом влияния окружающей среды данное испытание осуществляется после размещения во влажной среде (35 С и RH 90%). Характеристиками хорошей влагостойкости являются отсутствие изменений во внешнем виде, отсутствие пузырей, отсутствие коррозии, отсутствие трещин, отсутствие отслаивания согласно классификации в стандарте ISO 4628, а также отсутствие потери адгезии. При определении сопротивления к истиранию под действием высокого давления (также названном испытанием Фалекса) применяется вращающийся штифт 23, сжатый между двумя V-образными блоками 24 и 25, как изображено на фиг. 6. Испытание Фалекса используется, в частности при высоких скоростях для оценки износостойких и противозадирных свойств смазочных жидкостей в соответствии со стандартами ASTM D 2670 и ASTM D 3233, но оно также используется при низких скоростях для оценки твердых смазочных материалов в соответствии со способом ASTM D 2625. Испытание Фалекса приспособлено для применения резьбовых соединений, используемых в эксплуатируемых углеводородных скважинах, при этом в нем используются полузакрытая контактная геометрия (для гарантии удерживания третей смазочной основы); цилиндрическая геометрия для штифтов, приспособленных к нанесению покрытия полиуретанового типа; диапазон значений давление-скорость (диаграмма PV), который соответствует этому соединению; возможность проведения однонаправленных испытаний или альтернативных испытаний для имитации операции свинчивания и развинчивания. Условия испытания являются следующими: нагрузка = 785 Н; скорость вращения штифта = 60 об/мин; среднее давление в зоне контакта металл/металл = 560 МПа; скорость проскальзывания штифта= 20 мм/с. Целью данной проверки является моделирование, определение и сравнение износостойкости (стойкости к истиранию) различных покрытий без необходимости проводить определение на соединениях. Показатель истирания определяется с использованием стандарта ASTM D 2625-94, относящегося к измерению предельно допустимой нагрузки на твердую смазочную пленку, и соответствует резкому увеличению крутящего момента по сравнению с начальным состоянием порядка 1130 Нмм или коэффициентом трения порядка 0,15 при нагрузке 785 Н. Жесткая одно- или двухкомпонентная полиуретановая пленка по настоящему изобретению имеет следующие отличительные преимущества: твердость покрытия больше или равна таковой у эпоксидных смол, что обеспечивает модель трения с повышенной жесткостью посредством скольжения по поверхности без скачкообразного движения, что означает, что можно обойтись без обработки противозадирной поверхности, такой как посредством электролитических покрытий Cu-Sn-Zn. Свойства покрытия остаются постоянными в течение долгого времени, гарантируя, что операции свинчивания и развинчивания воспроизводимы; улучшенная ударопрочность, в частности, превышающая ударопрочность акриловых эпоксидных смол и усиливающая механические характеристики при сдвигающих/сжимающих нагрузках; превосходная адгезия и гибкость пленки подложки по сравнению с эпоксидными смолами, усиливающая применимость к деталям сложной геометрии, таким как резьба; усиленный барьерный эффект электролита (в частности, отсутствует остаточная вода при сушке),обеспечивающий лучшую противокоррозионную защиту, даже при отсутствии ингибиторов коррозии; незначительное экологическое воздействие и большая безопасность для пользователя благодаря отсутствию летучих органических соединений (VOC); сохранение механических свойств в диапазоне от -40 до +125 С, поскольку температуры стеклования исключены из этого диапазона. Данные идеи в этом отношении попадают в целый ряд технологических вопросов, в каждом из которых имеются упущения. Акриловые эпоксидные смолы, отвержденные с использованием УФ, в частности, служащие в качестве защитного покрытия и описанные в публикации WO 2006/104251 и публикации WO 2009/072486,имеют недостаток, заключающийся в неспособности быть примененными к соединению с внутренней резьбой или замковой муфтой из-за геометрии резьбы. Полиуретановые смолы, применяемые в настоящее время к резьбовым соединениям в данной об-8 024917 ласти техники, относятся к реакционноспособным эластомерным термопластичным классам, которые преимущественно обеспечивают соединение с уплотнителем, но механические свойства которых хуже,чем у жестких полиуретанов. Техники на основе термоотверждающихся эпоксидных смол вызывают необходимость в нанесении защитного нижнего слоя, защищающего от коррозии, а, возможно, и грунтовки, улучшающей адгезию, и верхнего слоя смазочного материала, вследствие чего неизбежно увеличение производственного времени. В условиях данной технологии получение ультрастойкого отверждаемого при нагревании покрытия типа жестких полиуретанов подразумевает, что фрикционные свойства и свойства улучшения адгезии на различных поверхностях или подготовка и защита поверхности, необходимые для подходящего противодействия вреду соединению, могут быть объединены в одном слое, независимо от того, какая зона резьбы поддается нагрузке. Заявитель сосредотачивает внимание на получении следующих жестких полиуретановых покрытий: однокомпонентного полиуретана, выпускаемого поставщиком HK Wentworth под торговым наименованием Electrolube NVOC, из-за твердости по карандашной шкале 7 Н, которая больше, чем у фторуретана, из-за гибкости и превосходной адгезии на металлической подложке; двухкомпонентная система полиуретан/полимочевина, выпускаемая поставщиком Merylithe под торговым наименованием Isolythe 115, из-за ее быстрого способа производства, из-за высокой твердости 750 Hv по сравнению с углеродистыми сталями, гибкости и высокой механической прочности. Во-первых, заявитель определил экспериментальные условия для получения однокомпонентного полиуретанового покрытия. Однокомпонентный полиуретан NVOC может быть разбавлен в негидроксилированном органическом растворителе, не содержащем VOC (летучих органических соединений), пропиленкарбонатного типа для регуляции его вязкости. Вязкость должна быть в диапазоне от 70 до 200 сП при 20 С для обеспечения хорошего охвата при пневматическом распылении. Добавление поверхностно-активного вещества, полидиметилсилоксанового силикона, может быть предусмотрено для улучшения смачивания подложки. Посредством реакции полиолов по изоцианатной функциональной группе высвобождается большое количество СО 2, который может содержаться в пузырьках или раковинах. Соединения щелочного магнийоксидного типа или кальцийоксидного типа могут быть добавлены в качестве поглотителя СО 2. Нанесение на подложку при температуре окружающей среды в диапазоне от 10 до 30 С проводилось распылением с помощью пневматического нагнетателя с дальнобойной распыляющей насадкой 1,7 мм и давлением от 4 до 6 бар. Подложку с нанесенным покрытием затем помещали в печь при 90 С и выдерживали в течение 10 мин при относительной влажности не менее 80%, полученной с помощью водяного пара, который образуется с использованием колбы Эрленмейера, содержащей воду, которая нагревалась до температуры кипения, при этом колба была расположена снаружи печи и подключена к емкостному устройству, приспособленному к размеру образца, через гибкую трубку с теплоизоляцией. После инициации отверждения следовал этап сушки при температуре окружающей среды в течение 72 ч. Альтернативный вариант включает размещение контейнера с горячей водой с объемом более 1 л внутри печи. Могут быть предусмотрены другие способы, которые включают нагревание подложки путем индукции. Водяной пар образуется при использовании колбы Эрленмейера, содержащей воду, нагретую до температуры кипения и распыляющуюся в близости от образца. Относительная влажность труднее контролируется, но она остается на уровне в диапазоне от 65 до 90%. Толщина влажной пленки должна быть примерно на 20% больше, чем требуется для сухой пленки из-за потери СО 2 в ходе реакции при парообразовании. Толщина сухой пленки находится в диапазоне от 30 до 50 мкм. Во-вторых, заявитель определил условия опыта для получения двухкомпонентного полиуретанового покрытия. Исследуемые двухкомпонентные системы полиуретан/полимочевина включают компонент А, полученный из смеси полиола на основе сложного полиэфира и 4,4'-метилен-бис(2-хлоранилина). Компонент А имеет свойства жидкости при от 70 С из-за наличия полиамина с температурой плавления в диапазоне от 85 до 90 С. Для возможности применения его в лаборатории заявитель нагревал и гомогенизировал компонент А при 90 С. Во избежание преждевременной перекристаллизации компонент был разбавлен до 30 вес.% с совместимым органическим растворителем без VOC типа двухосновного сложного эфира, такого как сложный метиловый эфир, предпочтительно сложный изобутиловый эфир. В этих условиях разбавленный компонент А обладает вязкостью менее 200 МПас при 20 С и менее 100 МПас при 90 С и может храниться в течение по крайней мере двух месяцев при температуре окружающей среды без риска кристаллизации. Жидкий компонент В с вязкостью в диапазоне от 1 до 2 Пас был вмешан к компоненту А при тем-9 024917 пературе окружающей среды и предпочтительно к компоненту А при 90 С для способствования однородности. Количества по весу, используемые для смеси, составляли 52% разбавленного компонента А и 48% компонента В. После гомогенизации в течение от 30 до 40 с с медленным механическим перемешиванием, во избежание включения пузырьков воздуха, смесь наносилась на подложку при температуре окружающей среды при использовании машины для нанесения пленки. Подложка затем помещалась в печь дополнительного отверждения на 15 мин при 90 С. Толщина полученной сухой пленки находилась в диапазоне от 20 до 40 мкм. Далее будут описаны полученные результаты. Во-первых, заявитель оценивал адгезионные свойства одно- и двухкомпонентных полиуретановых покрытий, не подвергшихся нагрузке, для сравнения их, inter alia, с результатами, полученными для покрытий эпоксидного, акрилово-эпоксидного и фторуретанового типа. Эпоксидное покрытие состояло из водной дисперсии олигомера типа смолы на основе бисфенола А,отверждаемой с использованием отвердителя диамин-функционализированного типа. Этот тип эпоксидного покрытия упоминается, в частности, в публикации WO 2008/090411. Акрилово-эпоксидное покрытие состояло из смеси смол (1-метил-1,2-этандиил)бис[окси(метил-2,1 этандиил)]диакрилата и триметилолпропантриакрилата, отверждаемой с применением ультрафиолетового излучения. Этот тип покрытия, обладающий твердостью по карандашной шкале 3 Н, упоминается, в частности, в публикации WO 2006/104251 и публикации WO 2009/072486. Фторуретановое покрытие состоит из водной дисперсной системы полимера фторэтиленвинилэфира, отвержденного с использованием алифатического полиизоцианатного отвердителя. Адгезия к различным металлическим подложкам определялась с помощью испытания царапаньем для нагрузок, возрастающих от 10 Н до 750 Н, что соответствует давлениям в зоне контакта сталь/сталь в диапазоне от 1,0 до 4,5 ГПа. Значения модуля Юнга, взятые из литературы для жестких термоотверджающихся полимеров полиуретанового типа, находились в диапазоне от 4 до 5 ГПа. Используя эти значения, можно было оценить, что среднее давление находилось в диапазоне от 150 до 450 МПа для нагрузок в диапазоне от 10 до 310 Н. Эти давления соответствуют теоретическим давлениям, определенным для типов резьбы во время действия. В табл. 1 приведены шероховатости, определенные с использованием ругозиметра в соответствии со стандартом ISO 1997 для используемых образцов. Таблица 1 Шероховатость испытуемых образцов в зависимости от состава для подготовки поверхности Критические нагрузки для испытания царапаньем, а также на адгезию с применением определения адгезии методом решетчатого надреза в соответствии со стандартом ISO 2409 (класс 0 для исключительной адгезии, класс 5 для посредственной адгезии), приведены в табл. 2, 3, 4 и 5 соответственно, для механически обработанной подложки из углеродистой стали (ХС 48 AsM), углеродистой стали с цинковым или марганцевым фосфатированием (PhZn), прокатной нержавеющей стали, содержащей 13% хрома(13Cr), и углеродистой стали, покрытой электролитическим покрытием Cu-Sn-Zn (ТА). Таблица 2 Сравнение адгезионной способности на ХС 48 AsM Таблица 3 Сравнение адгезионной способности на PhZn Таблица 4 Сравнение адгезионной способности на 13 Cr Таблица 5 Сравнение адгезионной способности на ТА Жесткие одно- и двухкомпонентные полиуретановые покрытия демонстрировали относительно высокую адгезию независимо от химической природы состава для подготовки поверхности. Посредством испытания показана способность покрытия оставаться на месте в зоне контакта под действием напряжения сдвига/сжатия. Высокая сила адгезии и когезии обеспечивает достаточное разделение поверхностей для увеличения долговечности и стойкости к истиранию. Стойкость полиуретанового покрытия сравнима с таковой у эпоксидной смолы и значительно выше, чем у отверждаемой УФ акрилово-эпоксидной смолы. Жесткие полиуретановые смолы и, в частности, однокомпонентные смолы, отверждаемые посредством влаги, были отобраны за их высокую гибкость и непроницаемость по сравнению с другими химическими свойствами. В табл. 6 показаны результаты адгезии после 168 ч погружения в деминерализованную воду при 40 С. Таблица 6 а Сравнение адгезии после погружения в деминерализованную воду жесткого однокомпонентного полиуретанового покрытия на ХС 48 AsM Таблица 6b Сравнение адгезии после погружения в деминерализованную воду жесткого однокомпонентного полиуретанового покрытия на 100% в твердой фазе на различных подложках Жесткий однокомпонентный полиуретан показал примечательную герметичность и исключительную адгезию влаги. Что касается критических нагрузок, то важно отметить, что адгезия не зависела от испытания погружением и могла усиливаться в условиях испытания, что подтверждает важность данной технологии, так как отверждение может продолжаться в течение долгого времени, если относительная влажность выше порога активации реакции. Влага расходуется до насыщения, тем самым ограничивая проблемы с образованием пузырей или плохим связыванием поверхностного слоя. Для иллюстрации непроницаемости покрытия заявитель провел измерения краевого угла смачивания на 3 мкл капле дистиллированной воды, помещенной на поверхность сухого покрытия, используя гониометр Kruss DSA 100 (диаметр иглы 0,52 мм), как показано в табл. 7. Во-вторых, заявитель оценил трибологические свойства ненагруженных жестких одно- и двухкомпонентных полиуретановых покрытий для сравнения их, inter alia, с результатами, полученными для эпоксидных, акрилово-эпоксидных и фторуретановых покрытий. Таблица 8 Независимо от способа нанесения коэффициент трения для жесткого полиуретанового покрытия был меньше, чем =0,080 для нагрузок 310 Н или менее, соответствующих давлениям в зоне контакта металл/металл до 3,5 ГПа, независимо от подложки, что обеспечивало хорошую смазку даже без снижающей трение добавки. Коэффициент трения находится в диапазоне от =0,080 до =0,13 для нагрузок в диапазоне от 250 до 750 Н, соответствующих давлению в зоне контакта металл/металл до 4,5 ГПа. На кривых трения для углеродистой стали с покрытием, иллюстрирующих данные результаты на фиг. 7 и 8,показан низкий, стабильный коэффициент трения для смолы PU 2K на 100% в твердой фазе (2 компонента) в сравнении с отверждаемой УФ-акриловой эпоксидной смолой, которая при нагрузке от 200 Н проявляет резкое расслаивание, отмеченное высоким, нестабильным коэффициентом трения. Трение на фиг. 8 увеличивалось в зависимости от приложенной нагрузки, но оставалось менее =0,12. Низкое значение трения было вызвано высокой твердостью и относительно высокой силой адгезии выбранных жестких полиуретанов, таким образом демонстрируется более совершенная модель трения скольжения. Стабильные коэффициенты трения менее =0,06 для давлений в диапазоне от 150 до 400 МПа, соответствующие средним давлениям на типы резьбы при действии во время обычного свинчивания, означают, что при свинчивании 7" 29 L80 VAM ТОР НТ соединений, которые являются высокочувствительными к истиранию (крутящий момент свинчивания 29900 Нм), могут быть предусмотрены относительно низкие значения крутящего момента при действии по сравнению со значениями крутящего момента между 68 и 74% для фторуретановых смол с высокими значениями трения, особенно на образце углеродистой стали с электролитическим покрытием Cu-Sn-Zn (FR 906320). В-третьих, заявитель определил характерные противокоррозионные свойства покрытий настоящего изобретения. Результаты, полученные при различных составах для подготовки поверхностей с, соответственно,жестким однокомпонентным полиуретановым покрытием и жестким двухкомпонентным полиуретановым покрытием приведены в табл. 9 и 10. Таблица 9 Коррозионная стойкость для жесткого однокомпонентного полиуретана, NVOC Таблица 10 Коррозионная стойкость для жесткого двухкомпонентного полиуретана, Isolythe 115 С целью сравнения в табл. 11 сравниваются противокоррозионные свойства жестких полиуретановых покрытий с другими смолами, не содержащими ингибитора коррозии, при том же составе для подготовки поверхности. Таблица 11 Сравнение коррозионной стойкости углеродистой стали и стали с цинковым фосфатированием За счет способа нанесения жестких однокомпонентных полиуретановых покрытий на 100% в твердой фазе с инициацией отверждения под воздействием влаги обеспечивается большая защита, чем при жестких двухкомпонентных полиуретановых покрытиях, и при этом может достигаться 750-часовое воздействие с низкой степенью ржавления на углеродистой стали после механической обработки. По сравнению с другими покрытиями жесткие полиуретановые покрытия и, в частности те, для которых отверждение инициируется влагой, демонстрируют лучшую защиту от коррозии и лучшее пассивирование состава для подготовки поверхности даже без ингибитора коррозии. Тем не менее, следует отметить, что данный способ должен полностью контролироваться во избежание образования пузырьков при гомогенизации и нанесении. Пузырьки могут способствовать диффузии электролитов к поверхности контакта и инициировать механизм коррозии. ФОРМУЛА ИЗОБРЕТЕНИЯ 1. Резьбовой трубчатый компонент для бурения или эксплуатации углеводородных скважин с резьбовой зоной (3; 4), расположенной на одном из его концов (1; 2) на наружной или внутренней периферийной поверхности, отличающийся тем, что по меньшей мере часть конца (1; 2) покрыта по меньшей мере одной сухой пленкой (12), имеющей твердость по шкале Шора D больше 50 и включающей матрицу из полиуретана и полимочевины, в которой количество уретановых функциональных групп преобладает над количеством мочевинных функциональных групп при соотношении по меньшей мере 55 вес.%. 2. Резьбовой трубчатый компонент по п.1, отличающийся тем, что матрица на основе полиуретана и полимочевины получена из мономера полиольного типа с высоким молекулярным весом, средства удлинения цепи и свободных ароматических изоцианатов, которые могут быть отверждены путем полиприсоединения с применением влаги. 3. Резьбовой трубчатый компонент по п.2, отличающийся тем, что матрица на основе полиуретана и полимочевины включает многофункциональный изоцианатный форполимер с количеством функциональных групп по меньшей мере 2, полученный из смеси полиолов на основе полиэфира, полибутадиена или гидроксилированного сложного полиэфира с молекулярной массой в диапазоне от 300 до 6000 г/моль и ароматических изоцианатов дифенилметандиизоцианатного типа в избытке; сореагент моно- или бис-оксазолидонного типа для инициации реакции и разбавления форполимера; алифатическое полиизоцианатное отверждающее средство гексаметилендиизоцианатного типа для поддержания отверждения; катализатор для форполимера типа простого диморфолинодиэтилового эфира или лаурата дибутилолова; пластификатор для контроля пенообразования во время формирования пленки, в частности, триэтиленфосфатного типа. 4. Резьбовой трубчатый компонент по п.3, отличающийся тем, что матрица на основе полиуретана и полимочевины включает поглотитель влаги для стабилизации форполимера при хранении путем захвата остаточной воды, при этом указанный поглотитель влаги относится к п-толуолсульфонилизоцианатному,триметилортоформиатному или триметилортоацетатному типу. 5. Резьбовой трубчатый компонент по п.3 или 4, отличающийся тем, что матрица на основе поли- 16024917 уретана и полимочевины включает поглотитель СО 2 кальцийоксидного или магнийоксидного типа для контроля вспенивания и образования пузырей во время реакции. 6. Резьбовой трубчатый компонент по п.1, отличающийся тем, что матрица на основе полиуретана и полимочевины получена из смеси термоплавких полиолов и полиаминов с низким молекулярным весом,которые могут быть отверждены путем поликонденсации с применением алифатического полиизоцианата. 7. Резьбовой трубчатый компонент по п.6, отличающийся тем, что матрица на основе полиуретана и полимочевины включает полиольный форполимер, выбранный из полиолов на основе сложного полиэфира, полиэфира и полибутадиена с молекулярной массой в диапазоне от 300 до 6000 г/моль, отвержденный с применением алифатического полиизоцианата (компонента А); термоплавкий полиамин с количеством функциональных групп 2 или более и с молекулярной массой в диапазоне от 168 до 600 г/моль, в частности 4,4'-метилен-бис-(2-хлоранилин); а также алифатическое полиизоцианатное отверждающее средство гексаметилендиизоцианатного типа в избытке. 8. Резьбовой трубчатый компонент по одному из пп.1-7, отличающийся тем, что матрица на основе полиуретана и полимочевины дополнительно включает по меньшей мере один твердый смазочный материал в качестве снижающего трение средства, выбранный из категории твердых смазочных материалов класса 1, 2, 3 или 4, в соотношении в диапазоне от 5 до 30 вес.%. 9. Резьбовой трубчатый компонент по п.8, отличающийся тем, что твердый смазочный материал выбран из твердого смазочного материала из класса 2 типа Bi2S3; твердого смазочного материала из класса 4 типа PTFE и их комбинации. 10. Резьбовой трубчатый компонент по одному из пп.1-9, отличающийся тем, что матрица на основе полиуретана и полимочевины дополнительно включает ингибитор коррозии. 11. Резьбовой трубчатый компонент по одному из пп.1-10, отличающийся тем, что вся резьбовая зона (3; 4) покрыта сухой пленкой (12). 12. Резьбовой трубчатый компонент по одному из пп.1-11, отличающийся тем, что он содержит участок уплотнения металл/металл, причем указанный участок уплотнения покрыт сухой пленкой (12). 13. Резьбовое трубчатое соединение, содержащее трубчатый компонент с наружной резьбой и трубчатый компонент с внутренней резьбой, расположенные один в другом, отличающиеся тем, что по меньшей мере один из указанных резьбовых трубчатых компонентов является компонентом по одному из пп.1-12. 14. Способ нанесения покрытия на резьбовой трубчатый компонент для бурения или эксплуатации углеводородных скважин с резьбовой зоной (3; 4), расположенной на одном из его концов (1; 2) на наружной или внутренней периферийной поверхности, отличающийся тем, что данный способ включает следующие этапы, на которых получают матрицу на основе полиуретана и полимочевины сухой пленки по одному из пп.1-10 в жидком состоянии; наносят матрицу из полиуретана и полимочевины в жидком состоянии путем распыления на часть конца (1; 2) указанного резьбового трубчатого компонента и отверждают матрицу с формированием сухой пленки (12) практически с жесткой структурой. 15. Способ по п.14, отличающийся тем, что матрица на основе полиуретана и полимочевины представляет собой матрицу сухой пленки по одному из пп.2-5. 16. Способ по п.15, отличающийся тем, что отверждение сухой пленки инициируют воздействием относительной влажности (RH) по меньшей мере 60% при температуре по меньшей мере 20 С необязательно с последующей сушкой. 17. Способ по п.16, отличающийся тем, что сушку проводят в инфракрасной или конвекционной сушильной печи, обеспеченной водяным паром. 18. Способ по п.14, отличающийся тем, что матрица на основе полиуретана и полимочевины представляет собой матрицу сухой пленки по одному из пп.6, 7. 19. Способ по п.18, отличающийся тем, что сухую пленку отверждают с помощью двухкомпонентного распыляющего устройства с внешним смешиванием отвердителя. 20. Способ по п.19, отличающийся тем, что отверждение сухой пленки сопровождается горячей сушкой или операцией дополнительного отверждения при температуре 90 С.
МПК / Метки
МПК: F16L 15/00, E21B 17/042, C09D 175/00, C10M 107/44
Метки: резьбовое, соединение
Код ссылки
<a href="https://eas.patents.su/20-24917-rezbovoe-soedinenie.html" rel="bookmark" title="База патентов Евразийского Союза">Резьбовое соединение</a>
Предыдущий патент: Анод для выделения кислорода
Следующий патент: Котел водогрейный твердотопливный
Случайный патент: Способ энантиоселективного синтеза отдельных энантиомеров модафинила ассиметричным окислением