Реактор в виде барботажной колонны и способ управления реактором в виде барботажной колонны
Номер патента: 21337
Опубликовано: 29.05.2015
Авторы: Вакамура Осаму, Ониси Ясухиро, Мурата Ацуси, Ямада Эиити, Като Юдзуру
Формула / Реферат
1. Реактор в виде барботажной колонны для осуществления реакции Фишера-Тропша в суспензии, содержащей твердотельные частицы катализатора, суспендированные в жидкости, содержащий
корпус реактора;
впускное отверстие, которое предусмотрено в нижней части корпуса реактора и обеспечивает возможность протекания синтез-газа, включающего газообразный монооксид углерода и газообразный водород в качестве основных компонентов, через него в суспензию;
выпускное отверстие, которое предусмотрено в верхней части корпуса реактора и предоставляет возможность вытекания через него газообразных углеводородов, синтезированных посредством химической реакции между синтез-газом и суспензией, непрореагировавшего синтез-газа;
туманоуловитель, который размещен между уровнем жидкости суспензии внутри корпуса реактора и выпускным отверстием для того, чтобы захватывать проходящие через него частицы катализатора; и
нагревательный узел для нагревания туманоуловителя.
2. Реактор в виде барботажной колонны по п.1, в котором нагревательный узел включает нагревательную трубу, по меньшей мере часть которой расположена внутри туманоуловителя, и узел с протеканием теплоносителя для подачи в нагревательную трубу теплоносителя, используемого для нагревания нагревательной трубы.
3. Способ управления реактором в виде барботажной колонны по любому из пп.1, 2, при этом способ содержит стадии, на которых
захватывают частицы катализатора туманоуловителем и
нагревают туманоуловитель до определенной температуры или выше, при которой затвердевшие компоненты суспензии расплавляются нагревателем.
4. Способ управления реактором в виде барботажной колонны по п.3, при этом способ дополнительно содержит стадию, на которой управляют скоростью потока синтез-газа в реактор таким образом, что значение приведенной скорости газа в реакторе находится в пределах от 0,04 м/с или более и 0,3 м/с или менее.
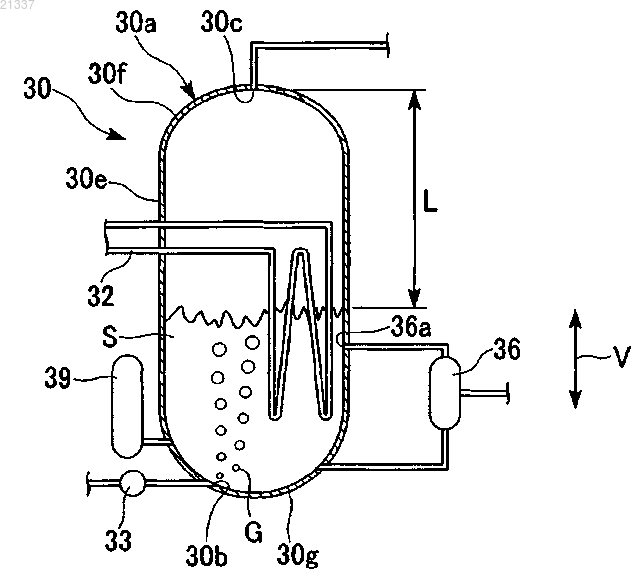
Текст
РЕАКТОР В ВИДЕ БАРБОТАЖНОЙ КОЛОННЫ И СПОСОБ УПРАВЛЕНИЯ РЕАКТОРОМ В ВИДЕ БАРБОТАЖНОЙ КОЛОННЫ Реактор в виде барботажной колонны включает корпус реактора, который содержит суспензию,содержащую твердотельные частицы катализатора, суспендированные в жидкости, впускное отверстие, которое предусмотрено в нижней части корпуса реактора и обеспечивает возможность протекания синтез-газа, включающего газообразный монооксид углерода и газообразный водород в качестве основных компонентов, через него в суспензию, и выпускное отверстие, которое предусмотрено в верхней части корпуса реактора и представляет возможность вытекания через него газообразных углеводородов, синтезированных посредством химической реакции между синтез-газом и суспензией, непрореагировавшего синтез-газа и т.п. Расстояние в вертикальном направлении между поверхностью жидкости суспензии и выпускным отверстием составляет 1,4 м или более и 10 м или менее.(71)(73) Заявитель и патентовладелец: ДЖЭПЭН ОЙЛ, ГЭЗ ЭНД МЕТАЛЗ НЭШНЛ КОРПОРЕЙШН; ИНПЕКС КОРПОРЕЙШН; ДжейЭкс НИППОН ОЙЛ ЭНД ЭНЕРДЖИ КОРПОРЕЙШН; ДЖАПАН ПЕТРОЛЕУМ ЭКСПЛОРЕЙШН КО., ЛТД.; КОСМО ОЙЛ КО., ЛТД.; НИППОН СТИЛ ИНДЖИНИРИНГ КО., ЛТД. (JP) Область техники Данное изобретение относится к реактору типа барботажной колонны, для синтеза углеводорода посредством химической реакции с применением катализатора, и к способу управления реактором в виде барботажной колонны. Заявка устанавливает приоритет заявки на патент Японии 2008-254813 и заявки на патент Японии 2008-254814, зарегистрированных 30 сентября 2008 г., содержание которых включено в данный документ полностью в качестве ссылки. В последние годы в качестве метода синтеза жидких топлив из природного газа была разработана система синтеза жидкого топлива с применением в качестве реактора барботажной колонны. В этой системе синтеза жидкого топлива, была использована технология GTL (газ-в-жидкость: синтез жидкого топлива) риформинга природного газа, чтобы производить синтез-газ, содержащий газообразный водород(Н 2) и газообразный монооксид углерода (СО) в качестве основных компонентов, синтеза углеводородов с применением катализатора с этим синтез-газом в качестве исходного газа посредством реакции синтеза Фишера-Тропша далее реакция синтеза FT) и дополнительной гидрогенизации и фракционирования углеводородов, чтобы производить жидкие топлива в качестве конечных продуктов, такие как лигроин(исходный тяжелый бензин), керосин, газойль и парафин. В реакторе в виде барботажной колонны, например, как показано в Патентном документе 1, синтезгаз подается в реактор из нижней части суспензии, включающей катализатор, и синтез-газ проходит через суспензию в виде пузырьков. При этом синтез-газ растворяется в жидкости суспензии, за время прохождения через суспензию, и приходит в соприкосновение с частицами катализатора, обеспечивающих протекание реакции синтеза FT, для производства газообразных или жидких углеводородов. Патентный документ Патентный документ 1. Публикация нерассмотренной заявки на патент Японии 2007-197405 При этом, как правило, синтез-газ, который не прореагировал внутри реактора в виде барботажной колонны, газообразные углеводороды и т.п. вытекают из верхней части реактора в виде барботажной колонны для того, чтобы быть разделенными. Непрореагировавший синтез-газ и т.п. возвращают снова в реактор в виде барботажной колонны, а газообразные углеводороды охлаждаются и сжижаются в ходе последующего процесса таким образом, чтобы стать жидким топливом. Однако, поскольку используются частицы катализатора малого диаметра, для того, чтобы получить хорошее псевдоожижение и смешанное состояние суспензии, то частицы катализатора увлекаются вверх от поверхности жидкости суспензии вместе с непрореагировавшим синтез-газом, газообразными углеводородами и т.п. таким образом, что выпускаются из отверстия для выпуска газа через верхнюю часть реактора в виде барботажной колонны, и газообразные углеводороды сжижаются, наряду с тем, что с ними смешиваются частицы катализатора, вследствие чего создается проблема, заключающаяся в том,что качество продуктов ухудшается, и внутри аппаратов и труб возникает удерживание и блокирование. Данное изобретение создано, принимая во внимание вышеописанные проблемы, и целью данного изобретения является обеспечение реактора в виде барботажной колонны, который сдерживает, вовлечение частиц катализатора в отходящие газообразные углеводороды. В соответствии с первой особенностью данного изобретения, предоставлен реактор в виде барботажной колонны, включающий корпус реактора, который содержит суспензию, содержащую твердотельные частицы катализатора, суспендированные в жидкости; впускное отверстие, которое предусмотрено в нижней части корпуса реактора и обеспечивает возможность протекания синтез-газа, включающего газообразный монооксид углерода и газообразный водород в качестве основных компонентов, через него в суспензию; и выпускное отверстие, которое предусмотрено в верхней части корпуса реактора и которое предоставляет возможность вытекания через него газообразных углеводородов, синтезированных посредством химической реакции между синтез-газом и суспензией, непрореагировавшего синтезгаза и т.п., при этом расстояние в вертикальном направлении между поверхностью жидкости суспензии и выпускным отверстием составляет 1,4 м или более и 10 м или менее. В соответствии с первой особенностью синтез-газ, подаваемый в жидкую суспензию внутри корпуса реактора через впускное отверстие, предусмотренное в корпусе реактора, превращается в углеводороды посредством химической реакции с частицами катализатора, включенными в суспензию, при одновременном подъеме через суспензию в виде пузырьков. Хотя некоторые частицы катализатора могут уноситься вверх от поверхности жидкости суспензии вместе с синтезированными газообразными углеводородами, непрореагировавшим синтез-газом, который не прореагировал внутри суспензии и т.п., таким образом, что удаляются из выпускного отверстия, предусмотренного в верхней части, расстояние в вертикальном направлении между поверхностью жидкости суспензии и выпускным отверстием установлено таким образом, что составляет 1,4 м или более и 10 м или менее. Посредством установки расстояния,составляющего 1,4 м или более, большинство частиц катализатора, которые уносятся вверх, падают под влиянием действующей на них силы тяжести перед достижением ими выпускного отверстия, и возвращаются в суспензию, содержащуюся в корпусе реактора. Соответственно, возможно сдерживание вовлечения частиц катализатора в углеводороды, вытекающие через выпускное отверстие. Кроме того, посредством установки расстояния, составляющего 10 м или менее, возможно сдержи-1 021337 вание повышения расходов, обусловленного увеличением размера реактора в виде барботажной колонны, и предотвращение трудностей при включении реактора в виде барботажной колонны в устройство для синтеза жидкого топлива. Кроме того, в вышеописанном реакторе в виде барботажной колонны, приведенная скорость синтез-газа, втекающего в корпус реактора, может составлять 0,04 м/с или более и 0,3 м/с или менее. В этом случае, поскольку скорость углеводородов, протекающих вверх от поверхности жидкости суспензии, сдерживается посредством установки приведенной скорости газа таким образом, чтобы она составляла 0,3 м/с или менее, возможно дополнительное надежное сдерживание вовлечения частиц катализатора в углеводороды, отходящие через выпускное отверстие. Кроме того, поскольку приведенная скорость газа устанавливается таким образом, что составляет 0,04 м/с или более, то возможно предотвращение накапливания катализатора внутри корпуса реактора вследствие осаждения частиц катализатора в суспензии, и, тем самым, предотвращение ухудшения эффективности химической реакции между синтез-газом и суспензией. В соответствии со второй особенностью данного изобретения, предоставлен реактор в виде барботажной колонны, включающий корпус реактора, который содержит суспензию, содержащую твердотельные частицы катализатора, суспендированные в жидкости; впускное отверстие, которое предусмотрено в нижней части корпуса реактора и обеспечивает возможность протекания синтез-газа, включающего газообразный монооксид углерода и газообразный водород в качестве основных компонентов, через него в суспензию; выпускное отверстие, которое предусмотрено в верхней части корпуса реактора и предоставляет возможность вытекания через него газообразных углеводородов, синтезированных посредством химической реакции между синтез-газом и суспензией, непрореагировавшего синтез-газа и т.п., и туманоуловитель, который размещен между поверхностью жидкости суспензии внутри корпуса реактора и выпускным отверстием для того, чтобы захватывать проходящие через него частицы катализатора. В соответствии с данной второй особенностью, синтез-газ, втекающий в суспензию, включающую катализатор, внутри корпуса реактора через впускное отверстие, предусмотренное в корпусе реактора,превращается в углеводороды посредством химической реакции с частицами катализатора, включенными в суспензию, при одновременном подъеме через суспензию в виде пузырьков. Хотя некоторые частицы катализатора могут уноситься вверх от поверхности жидкости суспензии вместе с синтезированными газообразными углеводородами, непрореагировавшим синтез-газом, который не прореагировал внутри суспензии и т.п., таким образом, чтобы удаляться из выпускного отверстия, предусмотренного в верхней части, однако, поскольку туманоуловитель предусмотрен между суспензией и выпускным отверстием,частицы катализатора захватываются туманоуловителем при прохождении через него. Соответственно,возможно сдерживание примешивания частиц катализатора в углеводороды, вытекающие через выпускное отверстие. Кроме того, в вышеописанном реакторе в виде барботажной колонны туманоуловитель может включать самонагреваемый узел. В этом случае, например, даже когда суспензия, включающая катализатор, прилипает к туманоуловителю, охлаждается и затвердевает, прилипшая суспензия может быть нагрета и расплавлена данным нагревательным узлом, с тем, чтобы стекать каплями и возвращаться в жидкую суспензию, содержащуюся в корпусе реактора. Соответственно, возможно предотвращение затвердевания суспензии, которое засоряет туманоуловитель, и предотвращение прекращения протекания газообразных углеводородов. Кроме того, в реакторе в виде барботажной колонны нагревательный узел может включать нагревательную трубу, по меньшей мере часть которой расположена внутри туманоуловителя, и узел с протеканием теплоносителя для подачи в нагревательную трубу теплоносителя, используемого для нагревания нагревательной трубы. В этом случае, поскольку нагревательная труба расположена внутри туманоуловителя, возможно дополнительное надежное нагревание туманоуловителя посредством предоставления возможности теплоносителю втекать в нагревательную трубу. Кроме того, например, посредством протекания пара, образованного в процессе выполнения теплообмена с суспензией, нагретой посредством реакции синтеза FT,которая является экзотермической реакцией, в нагревательную трубу, возможно эффективное нагревание туманоуловителя. Кроме того, в вышеописанном реакторе в виде барботажной колонны, приведенная скорость синтез-газа, втекающего в корпус реактора, может составлять 0,04 м/с или более и 0,3 м/с или менее. В этом случае, поскольку скорость углеводородов, протекающих вверх от поверхности жидкости суспензии, сдерживается посредством установки приведенной скорости газа таким образом, чтобы она составляла 0,3 м/с или менее, возможно дополнительное надежное сдерживание вовлечения частиц катализатора в углеводороды, вытекающие через выпускное отверстие. Кроме того, поскольку приведенная скорость газа устанавливается таким образом, что составляет 0,04 м/с или более, то возможно предотвращение накапливания катализатора внутри корпуса реактора вследствие осаждения частиц катализатора в суспензии, и, тем самым, предотвращение ухудшения эффективности химической реакции между синтез-газом и суспензией. Кроме того, способ управления реактором в виде барботажной колонны в соответствии с данным изобретением представляет собой способ управления реактором в виде барботажной колонны, включающем корпус реактора, который содержит суспензию, содержащую твердотельные частицы катализатора, суспендированные в жидкости; впускное отверстие, которое предусмотрено в корпусе реактора и обеспечивает возможность протекания синтез-газа, включающего газообразный монооксид углерода и газообразный водород в качестве основных компонентов, через него в суспензию; и выпускное отверстие, которое предусмотрено в верхней части корпуса реактора и предоставляет возможность вытекания через него газообразных углеводородов, синтезированных посредством химической реакции между синтез-газом и суспензией, непрореагировавшего синтез-газа и т.п. Способ включает стадию уменьшения количества суспензии, содержащейся в корпусе реактора, когда расстояние в вертикальном направлении между поверхностью жидкости суспензии и выпускным отверстием составляет менее чем 1,4 м. В соответствии с данным изобретением синтез-газ, втекающий в жидкую суспензию внутри корпуса реактора через впускное отверстие, превращается в углеводороды посредством химической реакции с частицами катализатора, включенными в суспензию, при одновременном подъеме через суспензию в виде пузырьков. Хотя синтезированные газообразные углеводороды и непрореагировавший синтез-газ,который не прореагировал внутри суспензии, уносятся вверх от верхней поверхности суспензии вместе с частицами катализатора, когда расстояние в вертикальном направлении между уровнем жидкости и выпускным отверстием меньше, чем 1,4 м, данное расстояние регулируется таким образом, чтобы оно стало равным 1,4 м или более, посредством уменьшения количества суспензии, содержащейся в корпусе реактора, т.е. посредством понижения поверхности жидкости суспензии до заданной позиции. Соответственно, большинство частиц катализатора, которые уносятся вверх, падают под влиянием действующей на них силы тяжести перед достижением ими выпускного отверстия, и возвращаются в суспензию, находящуюся в корпусе реактора. Соответственно, возможно сдерживание вовлечения частиц катализатора в углеводороды, вытекающие через выпускное отверстие. Согласно реактору в виде барботажной колонны и способу управления реактором в виде барботажной колонны в соответствии с данным изобретением, возможно сдерживание примешивания частиц катализатора в газообразные углеводороды, вытекающие наружу. Кроме того, посредством нагревания туманоуловителя нагревательным узлом возможно предотвращение затвердевания суспензии, которое засоряет туманоуловитель, и предотвращение прекращения протекания газообразных углеводородов. Краткое описание чертежей Фиг. 1 представляет собой схематическое изображение, показывающее общую конфигурацию устройства для синтеза жидкого топлива с применением реактора в виде барботажной колонны в соответствии с первым вариантом осуществления данного изобретения. Фиг. 2 представляет собой частичный вид поперечного сечения, показывающий общую конфигурацию реактора в виде барботажной колонны в соответствии с первым вариантом осуществления данного изобретения. Фиг. 3 представляет собой схематическое изображение, показывающее общую конфигурацию устройства для синтеза жидкого топлива с применением реактора в виде барботажной колонны в соответствии со вторым вариантом осуществления данного изобретения. Фиг. 4 представляет собой частичный вид поперечного сечения, показывающий общую конфигурацию реактора в виде барботажной колонны в соответствии со вторым вариантом осуществления данного изобретения. Фиг. 5 представляет собой вид поперечного сечения вдоль линии А-А на фиг. 4.Описание вариантов осуществления Первый вариант осуществления Далее в данном документе реактор в виде барботажной колонны в соответствии с первым вариантом осуществления данного изобретения и устройство для синтеза жидкого топлива с применением реактора в виде барботажной колонны будут описаны со ссылками на Фиг. 1 и 2. Фиг. 1 представляет собой схематическое изображение, показывающее общую конфигурацию устройства 1 для синтеза жидкого топлива, а Фиг. 2 представляет собой частичный вид поперечного сечения, показывающий общую конфигурацию реактора 30 в виде барботажной колонны. Как показано на фиг. 1, устройство 1 для синтеза жидкого топлива представляет собой промышленное устройство, которое выполняет процесс GTL (газ-в-жидкость), посредством которого исходный углеводородный материал, такой как природный газ, преобразуется в жидкое топливо. Это устройство для синтеза жидкого топлива 1 включает узел 3 для производства синтез-газа, узел 5 для синтеза FT и узел 7 повышения качества. Узел 3 для производства синтез-газа риформирует природный газ, который является исходным углеводородным материалом, чтобы получить синтез-газ, включающий газообразный монооксид углерода и газообразный водород в качестве основных компонентов. Узел 5 для синтеза FT производит углеводороды из полученного синтез-газа посредством реакции синтеза FT. Узел 7 повышения качества подвергает гидрогенизации и очищает жидкие углеводороды, полученные реакцией синтеза FT,чтобы получить жидкие топлива в качестве конечных продуктов (лигроин, керосин, газойль, парафин и т.п.). Далее в данном документе будут описаны компоненты этих соответствующих узлов. Вначале будет описан узел 3 для производства синтез-газа. Узел 3 для производства синтез-газа главным образом включает, например, реактор 10 десульфурации, узел 12 для риформинга, котел 14 для рекуперации отходящего тепла, парожидкостные сепараторы 16 и 18, узел 20 для удаления СО 2 и сепаратор 2 6 водорода. Реактор 10 десульфурации состоит из гидродесульфуратора и т.д. и удаляет серосодержащие компоненты из природного газа, используемого в качестве исходного материала. Узел 12 для риформинга риформирует природный газ, подаваемый из реактора 10 десульфурации, чтобы получить синтез-газ,включающий газообразный монооксид углерода (СО) и газообразный водород (Н 2) в качестве основных компонентов. Котел 14 для рекуперации отходящего тепла рекуперирует отходящее тепло синтез-газа,произведенного в узле 12 для риформинга, чтобы получить пар высокого давления. Парожидкостной сепаратор 16 разделяет воду, нагретую теплообменом с синтез-газом в котле 14 для рекуперации отходящего тепла, на пар (пар высокого давления) и жидкость. Парожидкостной сепаратор 18 удаляет конденсат из синтез-газа, охлажденного в котле 14 для рекуперации отходящего тепла, и подает газообразный компонент в узел 20 для удаления СО 2. Узел 20 для удаления СО 2 содержит абсорбционную колонну 22, которая посредством применения абсорбента удаляет газообразный диоксид углерода из синтез-газа,подаваемого из парожидкостного сепаратора 18 и регенерационную колонну 24, которая десорбирует газообразный диоксид углерода и регенерирует абсорбент, включающий газообразный диоксид углерода. Сепаратор 26 водорода отделяет часть газообразного водорода, включенного в синтез-газ, газообразный диоксид углерода от которого отделен узлом 20 для удаления СО 2. Следует при этом заметить, что необходимость в применении вышеуказанного узла 20 для удаления СО 2 может отсутствовать, в зависимости от обстоятельств. Среди них, узел 12 для риформинга риформирует природный газ посредством использования диоксида углерода и пара, чтобы получить синтез-газ при высокой температуре, включающий газообразный монооксид углерода и газообразный водород в качестве основных компонентов, посредством метода риформинга пара и газообразного диоксида углерода, представленного приведенными ниже формулами химических реакций (1) и (2). Кроме того, метод риформинга в этом узле 12 для риформинга не ограничивается вышеуказанным методом риформинга с применением пара и газообразного диоксида углерода. Например, метод парового риформинга, метод риформинга с частичным окислением (РОХ) с применением кислорода, метод автотермического риформинга (ATR), который является комбинацией метода с частичным окислением и метода парового риформинга, метод риформинга с газообразным диоксидом углерода и т.п. также могут быть использованы. Кроме того, предусмотрен сепаратор 26 водорода на линии, ответвляющейся отосновной трубы,которая соединяет узел 20 для удаления СО 2 или парожидкостной сепаратор 18 с реактором 30 в виде барботажной колонны. Этот сепаратор 26 водорода может, например, состоять из узла адсорбции водорода с колебаниями давления (PSA), который выполняет адсорбцию и десорбцию водорода посредством использования разности давлений. Этот узел адсорбции водорода с колебаниями давления (PSA) имеет адсорбенты (цеолитовый адсорбент, активированный уголь, глинозем, силикагель и т.п.) внутри нескольких адсорбционных колонн (не показаны), которые расположены параллельно. Посредством последовательного повторения процессов, включающих повышение давления, адсорбцию, десорбцию(уменьшение давления) и продувку водородом, в каждой из адсорбционных колонн, газообразный водород высокой чистоты (например, примерно 99,999%), отделенный от синтез-газа, может поставляться непрерывным образом. Кроме того, метод отделения газообразного водорода в сепараторе 26 водорода не ограничивается примером метода адсорбции с колебаниями давления, как в вышеуказанном узле адсорбции водорода с колебаниями давления (PSA). Например, может быть использован метод адсорбции с применением сплава, накапливающего водород, метод мембранного разделения или их комбинация. Метод адсорбции с применением сплава, накапливающего водород, представляет собой, например,технологию отделения газообразного водорода с применением сплава, накапливающего водород (TiFe,LaNi5, TiFe0,7-0,9, Mn0,3-0,1, TiMn1.5 и т.п.), который обладает способностью к адсорбции или выделению водорода в охлажденном или нагретом состоянии. Посредством предоставления нескольких адсорбционных колонн, в которых содержится сплав, накапливающий водород, и поочередного повторения в каждой из адсорбционных колонн, адсорбции водорода посредством охлаждения сплава, накапливающего водород, и выделения водорода посредством нагревания сплава, накапливающего водород, газообразный водород в синтез-газе может быть отделен и извлечен. В дополнение к этому, метод мембранного разделения представляет собой технологию отделения газообразного водорода, обладающего высокой способностью к проницаемости через мембрану, от смешанного газа, с применением мембраны, изготовленной из полимерного материала, такого как ароматический полиимид. Поскольку этот метод мембранного разделения не сопровождается фазовым превращением, он требует меньше энергии для выполнения, и эксплуатационные расходы при этом низкие. Кроме того, поскольку структура узла для мембранного разделения является простой и компактной, затраты на необходимое оборудование являются низкими, и не требуется такой большой производственной площади. Более того, поскольку при мембранном разделении отсутствует приводной узел, и диапазон стабильной эксплуатации широкий, то имеет место преимущество, заключающееся в простоте технического обслуживания и управления. Далее будет описан узел 5 для синтеза FT. Как показано на фиг. 1 и 2, узел 5 для синтеза FT в основном включает, например, регулятор 33 расхода, реактор 30 в виде барботажной колонны, парожидкостной сепаратор 34, сепаратор 36, парожидкостной сепаратор 38 и первую фракционирующую колонну 40. Регулятор 33 расхода регулирует расход синтез-газа G, который втекает в реактор 30 в виде барботажной колонны, таким образом, чтобы он был постоянным. Реактор 30 в виде барботажной колонны производит углеводороды посредством предоставления возможности синтез-газу, произведенному узлом 3 для производства синтез-газа, быть подвергнутым реакции синтеза FT с частицами катализатора,включенными в суспензию, находящуюся в реакторе, и снабжен датчиком 39 уровня жидкости, который будет описан ниже. Парожидкостной сепаратор 34 разделяет воду, протекающую через теплообменную трубу 32, которая размещена в реакторе 30 в виде барботажной колонны, и нагреваемую в ней, на пар(пар среднего давления) и жидкость. Сепаратор 36 соединен со средней частью реактора 30 в виде барботажной колонны и разделяет суспензию, включающую частицы катализатора, и жидкий углеводородный продукт. Парожидкостной сепаратор 38 соединен с реактором 30 в виде барботажной колонны и охлаждает непрореагировавший синтез-газ и газообразный углеводородный продукт, возвращает непрореагировавший синтез-газ в реактор 30 в виде барботажной колонны, и охлаждает газообразный углеводородный продукт до жидкого состояния. Первая фракционирующая колонна 40 дистиллирует жидкие углеводороды, подаваемые через сепаратор 36 и парожидкостной сепаратор 38 из реактора 30 в виде барботажной колонны, разделяет жидкие углеводороды на отдельные фракции в соответствии с температурами кипения и очищает их. В дополнение к этому, буферный узел, который имеет резервуар для временного хранения в нем суспензии, и который регулирует количество суспензии, содержащейся в реакторе 30 в виде барботажной колонны, может быть размещен с внешней стороны реактора 30 в виде барботажной колонны. Среди них реактор 30 в виде барботажной колонны функционирует в качестве реактора для синтезаFT, который синтезирует углеводороды посредством реакции синтеза Фишера-Тропша (FT) между синтез-газом и суспензией, содержащей твердотельные частицы катализатора, суспендированные в жидкости. Как показано на фиг. 2, реактор 30 в виде барботажной колонны включает корпус 30 а реактора, который содержит суспензию S, впускное отверстие 30b, которое предусмотрено в нижней части корпуса 30 а реактора и предоставляет возможность синтез-газу G протекать через него в суспензию S, и выпускное отверстие 30 с, которое предусмотрено в верхней части корпуса 30 а реактора и предоставляет возможность газообразным углеводородам, непрореагировавшему синтез-газу и т.п. вытекать через него из корпуса 30 а реактора. Корпус 30 а реактора включает цилиндрическую часть 30 е, которая имеет круговое поперечное сечение, и по существу полусферические верхнюю и нижнюю части 30f и 30g в виде крышек, которые расположены соответственно таким образом, что соединены с обоими концами части 30 е. В качестве такового, в корпусе 30 а реактора, впускное отверстие 30b расположено в нижней части нижней крышки 30g, размещенной на нижней стороне, и выпускное отверстие 30 с расположено в верхней части верхней крышки 30f, размещенной на верхней стороне. Например, синтез-газ G, из которого удален газообразный диоксид углерода, поступает во впускное отверстие 30b из узла 20 для удаления СО 2, и вышеуказанный парожидкостной сепаратор 38 соединен с выпускным отверстием 30 с. Датчик 39 уровня жидкости определяет положение верхней части суспензии S, содержащейся в реакторе 30 в виде барботажной колонны, т.е. высоту расположения поверхности жидкости суспензии S. При этом синтез-газ G, подаваемый в суспензию S вышеуказанным регулятором 33 расхода, оценивается далее в данном документе по приведенной скорости газа. В этом варианте осуществления поперечное сечение части 30 е корпуса является круговым. В дополнение к этому, суспензия в основном включает жидкие углеводороды, которые получены посредством реакции синтеза FT с частицами катализатора, и жидкие углеводороды включают парафиновую фракцию, которая затвердевает при определенной температуре или ниже. В этом реакторе 30 в виде барботажной колонны синтез-газ G, который является исходным газом,подается в виде пузырьков из впускного отверстия 30b реактора 30 в виде барботажной колонны и проходит через суспензию S, и в диспергированном состоянии газообразный водород и газообразный монооксид углерода подвергаются реакции синтеза, как показано в приведенной ниже формуле (3) химической реакции. Поскольку эта реакция синтеза FT является экзотермической реакцией, то реактор 30 в виде барботажной колонны, который является реактором теплообменного типа, внутри которого размещена теплообменная труба 32, адаптирован таким образом, что, например, вода (BFW: подпиточная вода для котла) подается в качестве хладагента, так что теплота вышеуказанной реакции синтеза FT может быть рекуперирована в виде, например, пара среднего давления посредством теплообмена между суспензией и водой. В заключение, будет описан узел 7 повышения качества. Как показано на фиг. 1, узел 7 повышения качества включает, например, реактор 50 гидрокрекинга парафиновой фракции, реактор 52 гидроочистки керосиновой и газойлевой фракции, реактор 54 гидроочистки лигроиновой фракции, парожидкостные сепараторы 56, 58 и 60, вторую фракционирующую колонну 70 и стабилизатор 72 лигроина. Реактор 50 гидрокрекинга парафиновой фракции соединен с нижней частью первой фракционирующей колонны 40. Реактор 52 гидроочистки керосиновой/газойлевой фракции соединен со средней частью первой фракционирующей колонны 40. Реактор 54 гидроочистки лигроиновой фракции соединен с верхней частью первой фракционирующей колонны 40. Парожидкостные сепараторы 56, 58 и 60 расположены таким образом, чтобы соответствовать реакторам гидрогенизации 50, 52 и 54, соответственно. Вторая фракционирующая колонна 70 разделяет и очищает жидкие углеводороды, подаваемые из парожидкостных сепараторов 56 и 58 в соответствии с их температурами кипения. Стабилизатор 72 лигроина дистиллирует жидкие углеводороды лигроиновой фракции, подаваемые из парожидкостного сепаратора 60 и второй фракционирующей колонны 70, чтобы выпускать бутан и компоненты, более легкие, чем бутан, в качестве газа, сжигаемого в факеле, и отделять и извлекать компоненты, имеющие число атомов углерода пять или более, в качестве продукта, являющегося лигроином. Далее будет описан процесс (GTL процесс) синтезирования жидких топлив из природного газа посредством устройства 1 длясинтеза жидкого топлива, сконфигурированного так, как описано выше. Природный газ (основным компонентом которого является СН 4) в качестве углеводородного сырья подается в устройство 1 для синтеза жидкого топлива из внешнего источника подачи природного газа (не показан), такого как месторождение природного газа или завод по обработке природного газа. Вышеуказанный узел 3 для производства синтез-газа риформирует этот природный газ, чтобы получить синтез-газ(газовую смесь, включающую газообразный монооксид углерода и газообразный водород в качестве основных компонентов). Более конкретно, вначале природный газ подается в реактор 10 десульфурации вместе с газообразным водородом, отделенным сепаратором 26 водорода. Реактор 10 десульфурации гидрогенизирует и десульфурирует серосодержащие компоненты, включенные в природный газ, с применением газообразного водорода вместе, например, с катализатором на базе ZnO. Посредством предварительной десульфурации природного газа указанным образом возможно предотвращение деактивации катализатора, используемого в узле 12 для риформинга, реакторе 30 в виде барботажной колонны и т.п., под действием серосодержащих компонентов. Природный газ (который может также содержать диоксид углерода), десульфурированный таким образом, подается в узел 12 для риформинга после смешивания газообразного диоксида углерода (СО 2),подаваемого из источника подачи диоксида углерода (не показан), и пара, образуемого в котле 14 для рекуперации отходящего тепла. Узел 12 для риформинга риформирует природный газ с применением диоксида углерода и пара, чтобы получить синтез-газ при высокой температуре, включающий газообразный монооксид углерода и газообразный водород в качестве основных компонентов, посредством вышеописанного способа риформинга с применением пара и газообразного диоксида углерода. При этом в узел 12 для риформинга подается, например, топливный газ для горелки, размещенной в узле 12 для риформинга, и воздух, и теплота реакции, требующаяся для вышеуказанной реакции риформинга с паром и СО 2, которая является эндотермической реакцией, предоставляется посредством теплоты сгорания топливного газа в горелке. Синтез-газ при высокой температуре (например, 900 С, 2,0 МПа изб. давл.), произведенный таким образом в узле 12 для риформинга подается в котел 14 для рекуперации отходящего тепла и охлаждается посредством теплообмена с водой, которая протекает через котел 14 для рекуперации отходящего тепла(например, 400 С), посредством чего рекуперируется отходящее тепло. При этом вода, нагретая синтезгазом в котле 14 для рекуперации отходящего тепла, подается в парожидкостной сепаратор 16. Из этого парожидкостного сепаратора 16 газообразный компонент подается в узел 12 для риформинга или другие внешние устройства в качестве пара высокого давления (например, от 3,4 до 10,0 МПа изб. давл.), а вода в качестве жидкого компонента возвращается в котел 14 для рекуперации отходящего тепла. В это же время синтез-газ, охлажденный в котле 14 для рекуперации отходящего тепла, подается в абсорбционную колонну 22 узла 20 для удаления СО 2 или реактор 30 в виде барботажной колонны после того как конденсат отделен и удален из синтез-газа в парожидкостном сепараторе 18. Абсорбционная колонна 22 абсорбирует газообразный диоксид углерода, включенный в синтез-газ, и удерживает его в абсорбенте, чтобы отделить газообразный диоксид углерода от синтез-газа. Абсорбент, включающий газообразный диоксид углерода внутри абсорбционной колонны 22, вводится в регенерационную колонну 24, абсорбент, включающий газообразный диоксид углерода, нагревается и подвергается процедуре десорбции посредством, например, пара, и результирующий десорбированный газообразный диоксид углерода возвращается в узел 12 для риформинга из регенерационной колонны 24 и используется по-6 021337 вторно для вышеуказанной реакции риформинга. Синтез-газ, полученный таким образом в узле 3 для производства синтез-газа, подается в реактор 30 в виде барботажной колонны вышеуказанного узла 5 для синтеза FT. При этом соотношение компонентов синтез-газа, подаваемого в реактор 30 в виде барботажной колонны, регулируется до соотношения компонентов, подходящего для реакции синтеза FT (например, Н 2:СО = 2:1 (молярное соотношение. Кроме того, давление синтез-газа, подаваемого в реактор 30 в виде барботажной колонны увеличивают до давления, подходящего для реакции синтеза FT, (например, примерно 3,6 МПа изб. давл.) компрессором (не показан), установленным на трубопроводе, который соединяет узел 20 для удаления СО 2 с реактором 30 в виде барботажной колонны. Кроме того, часть синтез-газа, газообразный диоксид углерода которого отделен вышеуказанным узлом 20 для удаления СО 2, также поступает в сепаратор 26 водорода. Сепаратор 26 водорода отделяет газообразный водород, включенный в синтез-газ, посредством адсорбции и десорбции (адсорбции и десорбции водорода с колебаниями давления (PSA с применением разности давления, как описано выше. Этот отделенный водород непрерывно подается из газгольдера (не показан) или т.п. посредством компрессора (не показан) к различным узлам для проведения реакции с применением водорода (например,реактору 10 десульфурации, реактору 50 гидрокрекинга парафиновой фракции, реактору 52 гидроочистки керосиновой и газойлевой фракции, реактору 54 гидроочистки лигроиновой фракции, и т.п.), которые выполняют заданные реакции с применением водорода внутри устройства 1 для синтеза жидкого топлива. Затем вышеуказанный узел 5 для реакции синтеза синтезирует жидкие углеводороды реакцией синтеза FT из синтез-газа, произведенного в вышеуказанном узле 3 для производства синтез-газа. Конкретно, как показано на фиг. 2, синтез-газ G, от которого газообразный диоксид углерода отделен в узле 20 для удаления СО 2, втекает во впускное отверстие 30b, которое предусмотрено в нижней части корпуса 30 а реактора 30 в виде барботажной колонны, через регулятор 33 расхода и поднимается в виде пузырьков через жидкую суспензию S, содержащуюся внутри корпуса 30 а реактора. При этом приведенная скорость синтез-газа G регулируется регулятором 33 расхода таким образом, что равна заданной величине в интервале от 0,04 м/с или более до 0,3 м/с или менее. В дополнение к этому, более предпочтительно, когда приведенная скорость газа составляет 0,1 м/с или более и 0,2 м/с или менее. Внутри корпуса 30 а реактора газообразный монооксид углерода и газообразный водород, которые включены в синтез-газ G, реагируют один с другим посредством вышеописанной реакции синтеза FT, посредством чего производятся газообразные или жидкие углеводороды. При этом положение поверхности жидкости суспензии S постоянно определяется датчиком 39 уровня жидкости. Расстояние L в вертикальном направлении V между поверхностью жидкости суспензии S и выпускным отверстием 30 с регулируется таким образом, чтобы оно составляло 1,4 м или более, и положение поверхности жидкости суспензии S регулируется таким образом, чтобы она находилась выше выпускного отверстия 36 а трубы, связанной с сепаратором 36. То есть, когда расстояние L меньше чем 1,4 м, количество суспензии S, содержащейся в корпусе реактора 30 а, может быть уменьшено таким образом, что расход суспензии S, вытекающей из сепаратора 36, временно увеличивается, или приведенная скорость газа уменьшается. Кроме того, часть суспензии S может быть временно введена в вышеуказанный буферный узел, размещенный с внешней стороны корпуса 30 а реактора. Когда поверхность жидкости суспензии S становится ниже выпускного отверстия 36 а, положение поверхности жидкости суспензии S может быть повышено таким образом, что расход суспензии S, вытекающей в сепаратор 36, временно уменьшается, или приведенная скорость газа увеличивается. Кроме того, суспензия S, сохраняемая в вышеуказанном буферном узле, размещенном с внешней стороны корпуса 30 а реактора, может быть подана в корпус 30 а реактора. Частицы катализатора, включенные в суспензию S, уносятся вверх от поверхности жидкости суспензии S вместе с мелкими каплями жидкости, которые образуются, когда разрываются пузырьки, состоящие из непрореагировавшего синтез-газа G, которые не прореагировали внутри суспензии, синтезированных газообразных углеводородов и т.п. Однако, поскольку приведенная скорость синтез-газа G и расстояние L регулируются, как описано выше, то большинство частиц катализатора, которые уносятся вверх, падают под влиянием действующей на них силы тяжести перед достижением ими выпускного отверстия 30 с, и возвращаются в суспензию, содержащуюся в корпусе 30 а реактора. Более того, посредством протекания воды через теплообменную трубу 32 реактора 30 в виде барботажной колонны во время этой реакции синтеза, теплота реакции синтеза FT удаляется, и вода, нагревающаяся посредством этого теплообмена, испаряется с образованием пара. Что касается этого пара, то вода, ожиженная в парожидкостном сепараторе 34, возвращается в теплообменную трубу 32, а газообразный компонент подается во внешний узел в качестве пара среднего давления (например, от 1,0 до 2,5 МПа изб. давл.). Жидкие углеводороды, синтезированные в реакторе 30 в виде барботажной колонны таким образом, извлекаются из средней части реактора 30 в виде барботажной колонны и вводятся в сепаратор 36. Сепаратор 36 отделяет суспензию, включающую частицы катализатора, и жидкий углеводородный продукт. Отделенная суспензия возвращается в реактор 30 в виде барботажной колонны, а жидкий углево-7 021337 дородный продукт подается в первую фракционирующую колонну 40. Из выпускного отверстия 30 с,предусмотренного в верхней части реактора 30 в виде барботажной колонны, непрореагировавший синтез-газ, газообразная составная часть синтезированных углеводородов и т.п. вводятся в парожидкостной сепаратор 38. Парожидкостной сепаратор 38 охлаждает эти газы, чтобы отделить некоторые сконденсированные жидкие углеводороды и ввести их в первую фракционирующую колонну 40. В то же время, что касается газообразного компонента, отделенного в парожидкостном сепараторе 38, непрореагировавший синтез-газ (СО и Н 2) возвращается в нижнюю часть реактора 30 в виде барботажной колонны и используется повторно для реакции синтеза FT. Кроме того, выпускаемый газ (газ, сжигаемый в факеле), иной,чем целевые продукты, включающий в качестве основного компонента газообразный углеводород с небольшим числом атомов углерода (С 4 или меньше), вводится во внешний агрегат для сжигания (не показан), сжигается в нем и затем выпускается в атмосферу. Затем первая фракционирующая колонна 40 нагревает жидкие углеводороды (с разным числом атомов углерода), подаваемые через сепаратор 36 и парожидкостной сепаратор 38 из реактора 30 в виде барботажной колонны, как описано выше, чтобы фракционировать дистилляцией жидкие углеводороды,используя разность в их температурах кипения. Посредством этого, первая фракционирующая колонна 40 разделяет и очищает жидкие углеводороды на лигроиновую фракцию (температура кипения которой ниже примерно 150 С), керосиновую и газойлевую фракцию (температура кипения которой составляет примерно от 150 до 350 С) и парафиновую фракцию (температура кипения которой выше примерно 350 С). Жидкие углеводороды (в основном С 21 или более), отбираемые в качестве парафиновой фракции из нижней части первой фракционирующей колонны 40, перемещаются в реактор 50 гидрокрекинга парафиновой фракции, жидкие углеводороды (в основном от С 11 до С 20), извлеченные в качестве керосиновой и газойлевой фракции из средней части первой фракционирующей колонны 40, перемещаются в реактор 52 гидроочистки керосиновой и газойлевой фракции, и жидкие углеводороды (в основном от C5 до С 10), извлеченные в качестве лигроиновой фракции из верхней части первой фракционирующей колонны 40, перемещаются в реактор 54 гидроочистки лигроиновой фракции. Реактор 50 гидрокрекинга парафиновой фракции подвергает гидрокрекингу жидкие углеводороды,являющиеся парафиновой фракцией с большим числом атомов углерода (примерно С 21 или более), которая подается из нижней части первой фракционирующей колонны 40, посредством использования газообразного водорода, подаваемого из вышеуказанного сепаратора 26 водорода, чтобы уменьшить число атомов углерода до С 20 или менее. В этой реакции гидрокрекинга углеводороды с небольшим числом атомов углерода и с низкой молекулярной массой производятся посредством разрыва связей С-С углеводородов с большим числом атомов углерода при применении катализатора и нагревания. Продукт, включающий жидкие углеводороды, подвергнутые гидрокрекингу посредством этого реактора 50 гидрокрекинга парафиновой фракции, разделяется на газ и жидкость в парожидкостном сепараторе 56, жидкие углеводороды от которого перемещаются во вторую фракционирующую колонну 70, а газообразный компонент (включающий газообразный водород) от которого перемещается в реактор 52 гидроочистки керосиновой/газойлевой фракции и реактор 54 гидроочистки лигроиновой фракции. Реактор 52 гидроочистки керосиновой и газойлевой фракции подвергает гидроочистке жидкие углеводороды, являющиеся керосиновой и газойлевой фракциями, имеющими в основном среднее число атомов углерода (примерно от С 11 до С 20), которые подаются из средней части первой фракционирующей колонны 40, посредством использования газообразного водорода, подаваемого через реактор 50 гидрокрекинга парафиновой фракции из сепаратора 26 водорода. В этой реакции гидроочистки, для того, чтобы получить в основном насыщенные углеводороды с боковыми цепями, жидкие углеводороды изомеризуются, и к ненасыщенным связям вышеуказанных жидких углеводородов добавляется водород, чтобы насытить их. В результате, продукт, включающий гидроочищенные жидкие углеводороды, разделяют на газ и жидкость в парожидкостном сепараторе 58, жидкие углеводороды от которого перемещают во вторую фракционирующую колонну 70, а газообразный компонент (включающий газообразный водород) от которого используют повторно для вышеуказанной реакции гидрогенизации. Реактор 54 гидроочистки лигроиновой фракции подвергает гидроочистке жидкие углеводороды,являющиеся лигроиновой фракцией с небольшим числом атомов углерода (примерно С 10 или менее),которая подается из верхней части первой фракционирующей колонны 40, посредством использования газообразного водорода, подаваемого через реактор 50 гидрокрекинга парафиновой фракции из сепаратора 26 водорода. В результате, продукт, включающий гидроочищенные жидкие углеводороды, разделяют на газ и жидкость в парожидкостном сепараторе 60, жидкие углеводороды от которого перемещают в стабилизатор 72 лигроина, а газообразный компонент (включающий газообразный водород) от которого используют повторно для вышеуказанной реакции гидрогенизации. Затем вторая фракционирующая колонна 70 дистиллирует жидкие углеводороды, подаваемые из реактора 50 гидрокрекинга парафиновой фракции и реактора 52 гидроочистки керосиновой и газойлевой фракции, как описано выше. В соответствии с этим вторая фракционирующая колонна 70 разделяет и очищает жидкие углеводороды из реактора 50 гидрокрекинга парафиновой фракции, разделяя их на углеводороды (температура кипения которых ниже примерно 150 С) с числом атомов углерода С 10 или менее, керосин (температура кипения которого примерно от 150 до 250 С), газойль (температура кипения которого примерно от 250 до 350 С) и некрекированную парафиновую фракцию (температура кипения которой выше, чем примерно 350 С). Газойль отбирается из нижней части второй фракционирующей колонны 70, и керосин отбирается из ее средней части. В то же время углеводородный газ с числом атомов углерода С 10 или менее отбирается из верхней части второй фракционирующей колонны 70 и подается в стабилизатор 72 лигроина. Кроме того, стабилизатор 72 лигроина дистиллирует углеводороды с числом атомов углерода С 10 или менее, которые подаются из вышеуказанного реактора 54 гидроочистки лигроиновой фракции и второй фракционирующей колонны 70. Таким образом, стабилизатор 72 лигроина отделяет и очищает лигроин (от C5 до С 10) в качестве продукта. Соответственно, высокочистый лигроин отбирается из нижней части стабилизатора 72 лигроина. В то же время выпускаемый газ (газ, сжигаемый в факеле), иной, чем целевые продукты, который содержит в качестве основного компонента углеводороды с заданным числом атомов углерода или меньше (С 4 или меньше), выпускается из верхней части стабилизатора 72 лигроина. В реакторе 30 в виде барботажной колонны в соответствии с первым вариантом осуществления данного изобретения синтез-газ G, который втекает в жидкую суспензию S внутри корпуса 30 а реактора из впускного отверстия 30b, которое предусмотрено в нижней части корпуса 30 а реактора, преобразуется в газообразные или жидкие углеводороды посредством реакции синтеза FT с частицами катализатора,включенными в суспензию S, при одновременном подъеме внутри суспензии S в виде пузырьков. При этом некоторые частицы катализатора могут уноситься в направлении к верхней части корпуса реактора от поверхности жидкости суспензии S вместе с синтез-газом G, который не прореагировал внутри суспензии S, газообразными углеводородами, которые были синтезированы внутри суспензии, или т.п. Однако, поскольку приведенная скорость газа регулируется регулятором 33 расхода таким образом, что равна заданной величине в интервале от 0,04 м/с или более до 0,3 м/с или менее, расстояние L в вертикальном направлении между поверхностью жидкости суспензии S и выпускным отверстием 30 с регулируется датчиком 39 уровня жидкости таким образом, что составляет 1,4 м или более и 10 м или менее. Поскольку скорость углеводородов, протекающих вверх от поверхности жидкости суспензии S,сдерживается посредством установки приведенной скорости газа таким образом, чтобы она составляла 0,3 м/с или менее, то возможно дополнительное надежное сдерживание вовлечения частиц катализатора в углеводороды, вытекающие через выпускное отверстие 30 с. Более того, поскольку приведенная скорость газа устанавливается таким образом, что составляет 0,04 м/с или более, то возможно предотвращение накапливания катализатора внутри корпуса 30 а реактора вследствие осаждения частиц катализатора в суспензии, и, тем самым, предотвращение ухудшения эффективности химической реакции между синтез-газом G и суспензией S. В дополнение к этому, поскольку расстояние L в вертикальном направлении между поверхностью жидкости суспензии S и выпускным отверстием 30 с составляет 1,4 м или более, то большинство частиц катализатора, которые уносятся вверх, падают перед достижением ими выпускного отверстия 30 с под влиянием действующей на них силы тяжести, и возвращаются в суспензию, содержащуюся в корпусе 30 а реактора. Соответственно, возможно сдерживание вовлечения частиц катализатора в углеводороды, вытекающие через выпускное отверстие 30 с. Посредством установки расстояния L, составляющего 10 м или менее, возможно сдерживание повышения расходов, обусловленного увеличением размера реактора 30 в виде барботажной колонны, и предотвращение трудностей при включении реактора 30 в виде барботажной колонны в устройство 1 для синтеза жидкого топлива. Кроме того, расстояние L предпочтительно составляет 1,4 м или более и 10 м или менее, и более предпочтительно 1,8 м или более и 7 м или менее. Посредством установки расстояния L, составляющего 1,8 м или более, возможно стабилизировать поток газа, вытекающего из выпускного отверстия 30 с, предусмотренного в верхней части. Также, посредством установки расстояния L, составляющего 7 м или менее, возможно включить реактор 30 в виде барботажной колонны в устройство 1 для синтеза жидкого топлива, не принимая во внимание его размеры. Далее будут описаны результаты, полученные измерением количества частиц катализатора, выпускаемых из выпускного отверстия 30 с корпуса 30 а реактора при применении реактора 30 в виде барботажной колонны устройства 1 для синтеза жидкого топлива в соответствии с первым вариантом осуществления. Табл. 1 показывает результаты испытаний в случае, когда внутренний диаметр части 30 е корпуса 30 а реактора составляет 250 мм. В примере данного изобретения и сравнительном примере определяли выпущенное количество частиц катализатора, когда реактор 30 в виде барботажной колонны функционировал в течение заданного периода времени. Как показано в примере данного изобретения, когда расстояние L в вертикальном направлении V между поверхностью жидкости суспензии S и выпускным отверстием 30 с составляло 1,4 м, было установлено, что количество частиц катализатора, выпущенное в час, составляло 0,0037 г/ч. В противоположность этому, как показано в сравнительном примере, когда расстояние L составляло 0,7 м, выпускаемое количество было увеличено вплоть до 0,0875 г/ч, что превышало величину в примере данного изобретения в двадцать раз или более. Когда результаты измерений и результаты расчетов преобразуются в концентрации катализатора в жидких углеводородах, подаваемых в первую фракционирующую колонну 40, может быть установлено, что концентрация составляла 2,1 мас. млн-1 в примере данного изобретения и составляла 50 мас. млн-1 в сравнительном примере. Кроме того, когда корпус 30 а реактора, в котором проводилось испытание примера данного изобретения, разбирали и визуально осматривали, было обнаружено, что частицы катализатора прилипали к внутренней поверхности части 30 е корпуса в интервале высот вплоть до 1,3 м в вертикальном направлении V от положения поверхности жидкости суспензии S. Хотя здесь был подробно описан со ссылками на чертежи первый вариант осуществления данного изобретения, конкретные конфигурации не ограничиваются вариантами осуществления, и данное изобретение также включает изменения в конфигурации без отклонения от сущности данного изобретения. Например, хотя поперечное сечение части 30 е корпуса является круговым в первом варианте осуществления, поперечное сечение может иметь другие формы, такие как овальная форма, четырехугольная форма и шестиугольная форма. Кроме того, в первом варианте осуществления, когда расстояние L в вертикальном направлении V между уровнем поверхности суспензии S и выпускным отверстием 30 с меньше чем 1,4 м, количество суспензии S, содержащейся в корпусе 30 а реактора, уменьшается. Однако вместо этого может быть генерирован тревожный звуковой сигнал или функционирование устройства 1 для синтеза жидкого топлива может быть остановлено. Кроме того, туманоуловитель может быть размещен между суспензией S и выпускным отверстием 30 с внутри корпуса 30 а реактора таким образом, чтобы захватывать проходящие через него частицы катализатора. Туманоуловитель имеет, например, структуру, в которой сформировано множество малых взаимно связанных пространств посредством переплетения тонких металлических проволок. Второй вариант осуществления Далее в данном документе реактор в виде барботажной колонны в соответствии со вторым вариантом осуществления данного изобретения и устройство для синтеза жидкого топлива с применением реактора в виде барботажной колонны будут описаны со ссылками на фиг. с 3 по 5. Фиг. 3 представляет собой схематическое изображение, показывающее общую конфигурацию устройства 1 для синтеза жидкого топлива, а фиг. 4 представляет собой частичный вид поперечного сечения, показывающий общую конфигурацию реактора в виде барботажной колонны. Как показано на фиг. 3, устройство 1 для синтеза жидкого топлива представляет собой промышленное устройство, которое выполняет процесс GTL (газ-в-жидкость), посредством которого исходный углеводородный материал, такой как природный газ, преобразуется в жидкое топливо. Это устройство для синтеза жидкого топлива 1 включает узел 3 для производства синтез-газа, узел 5 для синтеза FT и узел 7 повышения качества. Узел 3 для производства синтез-газа риформирует природный газ, который является исходным углеводородным материалом, чтобы получить синтез-газ, включающий газообразный монооксид углерода и газообразный водород в качестве основных компонентов. Узел 5 для синтеза FT производит углеводороды из полученного синтез-газа посредством реакции синтеза FT. Узел 7 повышения качества подвергает гидрогенизации и очищает жидкие углеводороды, полученные реакцией синтеза FT,чтобы получить жидкие топлива в качестве конечных продуктов (лигроин, керосин, газойль, парафин и т.п.). Компоненты узла 3 для производства синтез-газа и узла 7 повышения качества являются такими же,- 10021337 что и в первом варианте осуществления. Далее в данном документе будет описан узел 5 для синтеза FT,имеющий компоненты, отличающиеся от компонентов первого варианта осуществления. Узел 5 для синтеза FT в основном включает, например, регулятор 33 расхода, реактор 30 в виде барботажной колонны, парожидкостной сепаратор 34, сепаратор 36, парожидкостной сепаратор 38 и первую фракционирующую колонну 40. Регулятор 33 расхода регулирует расход синтез-газа G, который втекает в реактор 30 в виде барботажной колонны, таким образом, чтобы он был равен заданной величине. Реактор 30 в виде барботажной колонны выполняет реакцию синтеза FT для синтез-газа, произведенного в вышеуказанном узле 3 для производства синтез-газа, чтобы получить жидкие углеводороды. Парожидкостной сепаратор 34 разделяет воду, протекающую через теплообменную трубу 32, которая размещена в реакторе 30 в виде барботажной колонны, и нагреваемую в ней, на пар (пар среднего давления) и жидкость. Сепаратор 36 соединен со средней частью реактора 30 в виде барботажной колонны таким образом, что разделяет частицы катализатора и жидкий углеводородный продукт, извлеченные из реактора 30 в виде барботажной колонны. Парожидкостной сепаратор 38 соединен с верхней частью реактора 30 в виде барботажной колонны таким образом, что охлаждает непрореагировавший синтез-газ и газообразный углеводородный продукт, возвращает непрореагировавший синтез-газ в реактор 30 в виде барботажной колонны, и охлаждает газообразный углеводородный продукт до жидкого состояния. Первая фракционирующая колонна 40 дистиллирует жидкие углеводороды, подаваемые через сепаратор 36 и парожидкостной сепаратор 38 из реактора 30 в виде барботажной колонны, разделяет жидкие углеводороды на отдельные фракции в соответствии с температурами кипения и очищает их. Среди них реактор 30 в виде барботажной колонны функционирует в качестве реактора для синтезаFT, который синтезирует углеводороды посредством реакции синтеза Фишера-Тропша (FT) между синтез-газом и суспензией, содержащей твердотельные частицы катализатора, суспендированные в жидкости. Как показано на фиг. 4, реактор 30 в виде барботажной колонны включает корпус 30 а реактора, который содержит суспензию S, впускное отверстие 30b, которое предусмотрено на одном конце корпуса 30 а реактора и которое предусмотрено в нижней части корпуса 30 а реактора и предоставляет возможность синтез-газу G протекать через него в суспензию S, выпускное отверстие 30 с, которое предусмотрено на другом конце корпуса 30 а реактора и предоставляет возможность углеводородам вытекать через него из корпуса 30 а реактора, и туманоуловитель 30d, который предусмотрен между выпускным отверстием 30 с и поверхностью жидкости суспензии S внутри корпуса 30 а реактора, чтобы захватывать проходящие через него частицы катализатора. В корпусе 30 а реактора впускное отверстие 30b расположено в нижней части, а выпускное отверстие 30 с расположено в верхней части. Например, синтез-газ G, из которого удален газообразный диоксид углерода, поступает во впускное отверстие 30b из узла 20 для удаления СО 2, и вышеуказанный парожидкостной сепаратор 38 соединен с выпускным отверстием 30 с. В дополнение к этому суспензия S в основном включает жидкие углеводороды, которые получены посредством реакции синтеза FT с частицами катализатора, и жидкие углеводороды включают парафиновую фракцию, которая затвердевает при определенной температуре или ниже. Кроме того, в этом варианте осуществления туманоуловитель 30d имеет, например, структуру, в которой сформировано множество малых взаимно связанных пространств посредством переплетения тонких металлических проволок. Кроме того, синтез-газ G, подаваемый в суспензию S вышеуказанным регулятором 33 расхода, оценивается далее в данном документе по приведенной скорости газа. В этом варианте осуществления, как показано на фиг. с 3 по 5, туманоуловитель 30d включает нагревательный узел 31, имеющий нагревательную трубу 31 а, которая установлена таким образом, что по меньшей мере часть ее расположена в виде змеевика внутри туманоуловителя 30d, и парожидкостной сепаратор (узел с протеканием теплоносителя) 34, который подает пар (теплоноситель), нагревающий нагревательную трубу 31 а, в нагревательную трубу 31 а. В этом реакторе 30 в виде барботажной колонны синтез-газ G, который является исходным газом,подается в виде пузырьков из впускного отверстия 30b реактора 30 в виде барботажной колонны и проходит через суспензию S, и в диспергированном состоянии газообразный водород и газообразный монооксид углерода подвергаются реакции синтеза, как показано в приведенной выше формуле (3) химической реакции. Узел 5 для синтеза FT производит жидкие углеводороды реакцией синтеза FT из синтез-газа, произведенного узлом 3 для производства синтез-газа. Конкретно, как показано на фиг. 4, синтез-газ G, от которого газообразный диоксид углерода отделен в узле 20 для удаления СО 2, втекает во впускное отверстие 30b, которое предусмотрено в нижней части корпуса 30 а реактора 30 в виде барботажной колонны, через регулятор 33 расхода и поднимается в виде пузырьков через жидкую суспензию S, содержащуюся внутри корпуса 30 а реактора. При этом,внутри корпуса 30 а реактора, газообразный монооксид углерода и газообразный водород, которые включены в синтез-газ G, реагируют один с другим посредством вышеописанной реакции синтеза FT, посредством чего производятся газообразные или жидкие углеводороды. Кроме того, приведенная скорость синтез-газа G регулируется регулятором 33 расхода таким образом, что равна заданной величине в ин- 11021337 тервале от 0,04 м/с или более до 0,3 м/с или менее. В дополнение к этому, более предпочтительно, когда приведенная скорость газа составляет 0,1 м/с или более и 0,2 м/с или менее. Частицы катализатора, включенные в суспензию S, уносятся вверх от поверхности жидкости суспензии S вместе с мелкими каплями жидкости, которые образуются, когда разрываются пузырьки, состоящие из непрореагировавшего синтез-газа G, которые не прореагировали внутри суспензии, синтезированных газообразных углеводородов и т.п., и проходят через малые пространства, образованные в туманоуловителе 30d. При этом, несмотря на то, что газ, такой как синтез-газ G и газообразные углеводороды, проходит через данные малые пространства, капли жидкости или включенные в них твердотельные частицы катализатора захватываются туманоуловителем 30d. Кроме того, суспензия S, которая имеет капли жидкости с уменьшенными размерами, может прилипать к туманоуловителю 30d, и часть ее может затвердевать при потере ею тепла. При этом, когда туманоуловитель 30d нагрет до определенной температуры, при которой затвердевший компонент суспензии S плавится, или выше, посредством нагревательной трубы 31 а, в которой протекает пар, суспензия S, которая преобразована в капли сравнительно больших размеров, возвращается к жидкой суспензии S, содержащейся внутри корпуса 30 а реактора. Более того, посредством протекания подпиточной воды для котла (BFW) через теплообменную трубу 32 реактора 30 в виде барботажной колонны во время этой реакции синтеза, теплота реакции синтеза FT удаляется, и вода, нагревающаяся посредством этого теплообмена, испаряется с образованием пара. Что касается этого пара, то вода, ожиженная в парожидкостном сепараторе 34, может быть возвращена в теплообменную трубу 32, а газообразный компонент может быть подан во внешний узел, такой как вышеуказанная нагревательная труба 31 а, в качестве пара среднего давления (например, от 1,0 до 2,5 МПа изб. давл.). Жидкие углеводороды, синтезированные в реакторе 30 в виде барботажной колонны таким образом, извлекаются из средней части реактора 30 в виде барботажной колонны и вводятся в сепаратор 36. Сепаратор 36 разделяет катализатор (твердотельный компонент) и жидкий компонент, включающий жидкий углеводородный продукт, в извлеченной суспензии. Часть отделенного катализатора подается в реактор 30 в виде барботажной колонны в виде суспензии вместе с жидкими углеводородами, а жидкий компонент подается в первую фракционирующую колонну 40. Кроме того, непрореагировавший синтезгаз и газообразная составная часть синтезированных углеводородов вводятся в парожидкостной сепаратор 38 из выпускного отверстия 30 с, предусмотренного в верхней части реактора 30 в виде барботажной колонны. Парожидкостной сепаратор 38 охлаждает эти газы, чтобы отделить жидкие углеводороды,сконденсированные в качестве части жидкости, чтобы ввести их в первую фракционирующую колонну 40. В то же время, что касается газообразного компонента, отделенного в парожидкостном сепараторе 38, непрореагировавший синтез-газ (СО и Н 2) возвращается в нижнюю часть реактора 30 в виде барботажной колонны и используется повторно для реакции синтеза FT. Кроме того, выпускаемый газ (газ,сжигаемый в факеле), иной, чем целевые продукты, содержащий в качестве основного компонента газообразный углеводород с небольшим числом атомов углерода (С 4 или меньше), используется в качестве топливного газа узла 12 для риформинга или вводится во внешний агрегат для сжигания (не показан),сжигается в нем и затем выпускается в атмосферу. В реакторе 30 в виде барботажной колонны в соответствии со вторым вариантом осуществления данного изобретения синтез-газ G, который втекает в жидкую суспензию S внутри корпуса 30 а реактора из впускного отверстия 30b, которое предусмотрено в нижней части корпуса 30 а реактора, преобразуется в газообразные и жидкие углеводороды посредством реакции синтеза FT с частицами катализатора,включенными в суспензию S, при одновременном подъеме внутри суспензии S в виде пузырьков. При этом некоторые частицы катализатора могут уноситься в направлении к верхней части от поверхности жидкости суспензии S вместе с синтез-газом G, который не прореагировал внутри суспензии S, газообразными углеводородами, которые были синтезированы внутри суспензии, или т.п. Однако, поскольку туманоуловитель 30d предусмотрен между суспензией S и выпускным отверстием 30 с, частицы катализатора захватываются туманоуловителем 30d при прохождении через внутреннее пространство туманоуловителя 30d. Соответственно, возможно сдерживание вовлечения частиц катализатора в углеводороды,вытекающие через выпускное отверстие 30 с и возможно повышение качества и выхода углеводородов как продукта. Кроме того, поскольку туманоуловитель 30d включает нагревательный узел 31, имеющий нагревательную трубу 31 а и парожидкостной сепаратор 34, то даже когда часть суспензии S прилипает к туманоуловителю 30d, и парафиновая фракция, включенная в углеводороды суспензии, охлаждается и затвердевает, отвержденный компонент суспензии S может быть нагрет и расплавлен нагревательным узлом 31, с тем, чтобы стекать каплями и возвращаться в суспензию S, содержащуюся в корпусе 30 а реактора. Соответственно, возможно предотвращение затвердевания суспензии S в туманоуловителе 30d,которое засоряет туманоуловитель, и предотвращение прекращения протекания газообразных углеводородов. Это может улучшить производительность реактора 30 в виде барботажной колонны. Кроме того, поскольку часть нагревательной трубы 31 а расположена внутри туманоуловителя 30d,то возможно использование втекания греющего пара в нагревательную трубу 31 а для дополнительного надежного нагревания туманоуловителя 30d. Посредством протекания пара, нагретого внутри теплообменной трубы 32 и отделенного в парожидкостном сепараторе 34, в нагревательную трубу 31 а, возможно эффективное нагревание туманоуловителя 30d без образования нового теплоносителя с применением электроэнергии или т.п. Кроме того, приведенная скорость газа регулируется регулятором 33 расхода таким образом, что равна заданной величине в интервале от 0,04 м/с или более до 0,3 м/с или менее. Поскольку скорость углеводородов, протекающих вверх от поверхности жидкости суспензии S, сдерживается посредством установки приведенной скорости газа таким образом, чтобы она составляла 0,3 м/с или менее, то возможно дополнительное надежное сдерживание вовлечения частиц катализатора в углеводороды, вытекающие из выпускного отверстия 30 с. Кроме того, поскольку приведенная скорость газа устанавливается таким образом, что составляет 0,04 м/с или более, то возможно предотвращение накапливания катализатора внутри корпуса 30 а реактора вследствие осаждения частиц катализатора в суспензии, и, тем самым,предотвращение ухудшения эффективности химической реакции между синтез-газом G и суспензией S. Далее будут описаны результаты, полученные измерением количества частиц катализатора, выпускаемых из выпускного отверстия 30 с корпуса 30 а реактора при применении реактора 30 в виде барботажной колонны устройства 1 для синтеза жидкого топлива в соответствии с вышеописанным вариантом осуществления. Табл. 2 показывает результаты испытаний в случае, когда внутренний диаметр цилиндрической средней части корпуса 30 а реактора составляло 250 мм. В примере и сравнительном примере выпущенное количество частиц катализатора определяли, когда расстояние в вертикальном направлении между поверхностью жидкости суспензии S и выпускным отверстием 30 с было установлено равным постоянной величине 0,7 м, и реактор 30 в виде барботажной колонны функционировал в течение заданного периода времени. Таблица 2 Как показано в примере данного изобретения, когда туманоуловитель 30d был предусмотрен между поверхностью жидкости суспензии S и выпускным отверстием 30 с, было найдено, что количество частиц катализатора, выпущенное в час, составляло 0,00023 г/ч. В противоположность этому, как показано в сравнительном примере, когда туманоуловитель 30d не был предусмотрен, выпущенное количество было увеличено до 0,0875 г/ч, что было в несколько сотен раз больше, чем в случае, когда туманоуловитель 30d был предусмотрен. Когда результаты измерений и результаты расчетов преобразуются в концентрацию катализатора в жидких углеводородах, подаваемых в первую фракционирующую колонну 40 из реактора 30 в виде барботажной колонны, было найдено, что концентрация составляла 0,03 мас. млн-1, когда туманоуловитель 30d был предусмотрен, и составляла 50 мас. млн-1, когда туманоуловитель 30d не был предусмотрен. Хотя здесь был подробно описан со ссылками на чертежи второй вариант осуществления данного изобретения, конкретные конфигурации не ограничиваются вариантами осуществления, и данное изобретение также включает изменения в конфигурации без отклонения от сущности данного изобретения. Например, во втором варианте осуществления пару, отделенному в парожидкостном сепараторе 34,предоставляется возможность протекания через нагревательную трубу 31 а, однако возможность протекания через нее может быть предоставлена пару, полученному посредством отдельного узла для генерации пара. Кроме того, во втором варианте осуществления используется нагревательный узел 31, включающий нагревательную трубу 31 а и парожидкостной сепаратор 34, однако любой нагреватель или т.п. может быть использован в качестве нагревательного узла. Кроме того, во втором варианте осуществления туманоуловитель 30d может быть не снабжен нагревательным узлом 31. Это обусловлено тем, что суспензии S не требуется быть нагретой и расплавленной для того, чтобы стекать каплями из туманоуловителя 30d, когда туманоуловитель 30d является достаточно большим по отношению к количеству прилипшей суспензии S. Кроме того, во втором варианте осуществления туманоуловитель 30d сформирован посредством переплетения тонких металлических проволок. Однако, например, туманоуловитель 30d может иметь структуру, в которой канал для протекания, имеющий форму лабиринта или форму жалюзи, образован посредством объединения пластин таким образом, чтобы обеспечить возможность прохождения через них газообразных углеводородов и захватывания частиц катализатора, поднимающихся вверх от суспензии S. В соответствии с реактором в виде барботажной колонны и способом управления им возможно сдерживание примешивания частиц катализатора в газообразные углеводороды, вытекающие из реактора в виде барботажной колонны. Описание цифровых обозначений 30: Реактор в виде барботажной колонны 30 а: Корпус реактора 30b: Впускное отверстие 30 с: Выпускное отверстие 30d: Туманоуловитель 31: Нагревательный узел 31 а: Нагревательная труба 34: Парожидкостной сепаратор (узел с протеканием теплоносителя) 39: Датчик уровня жидкостиS: суспензия ФОРМУЛА ИЗОБРЕТЕНИЯ 1. Реактор в виде барботажной колонны для осуществления реакции Фишера-Тропша в суспензии,содержащей твердотельные частицы катализатора, суспендированные в жидкости, содержащий корпус реактора; впускное отверстие, которое предусмотрено в нижней части корпуса реактора и обеспечивает возможность протекания синтез-газа, включающего газообразный монооксид углерода и газообразный водород в качестве основных компонентов, через него в суспензию; выпускное отверстие, которое предусмотрено в верхней части корпуса реактора и предоставляет возможность вытекания через него газообразных углеводородов, синтезированных посредством химической реакции между синтез-газом и суспензией, непрореагировавшего синтез-газа; туманоуловитель, который размещен между уровнем жидкости суспензии внутри корпуса реактора и выпускным отверстием для того, чтобы захватывать проходящие через него частицы катализатора; и нагревательный узел для нагревания туманоуловителя. 2. Реактор в виде барботажной колонны по п.1, в котором нагревательный узел включает нагревательную трубу, по меньшей мере часть которой расположена внутри туманоуловителя, и узел с протеканием теплоносителя для подачи в нагревательную трубу теплоносителя, используемого для нагревания нагревательной трубы. 3. Способ управления реактором в виде барботажной колонны по любому из пп.1, 2, при этом способ содержит стадии, на которых захватывают частицы катализатора туманоуловителем и нагревают туманоуловитель до определенной температуры или выше, при которой затвердевшие компоненты суспензии расплавляются нагревателем. 4. Способ управления реактором в виде барботажной колонны по п.3, при этом способ дополнительно содержит стадию, на которой управляют скоростью потока синтез-газа в реактор таким образом,что значение приведенной скорости газа в реакторе находится в пределах от 0,04 м/с или более и 0,3 м/с или менее.
МПК / Метки
МПК: C10G 2/00
Метки: колонны, реактор, управления, способ, барботажной, реактором, виде
Код ссылки
<a href="https://eas.patents.su/17-21337-reaktor-v-vide-barbotazhnojj-kolonny-i-sposob-upravleniya-reaktorom-v-vide-barbotazhnojj-kolonny.html" rel="bookmark" title="База патентов Евразийского Союза">Реактор в виде барботажной колонны и способ управления реактором в виде барботажной колонны</a>
Предыдущий патент: Фармацевтические композиции и способы их получения при низкой концентрации примесей
Следующий патент: Моющие средства для очистки ствола скважины и способы их использования
Случайный патент: Трубная муфта