Установка для реакции синтеза углеводородов, реакционная система синтеза углеводородов и способ синтеза углеводородов
Формула / Реферат
1. Установка для реакции синтеза углеводородов, включающая в себя
реактор, предназначенный для заполнения суспензией катализатора, содержащей частицы твердого катализатора, суспендированные в жидкости, в котором суспензию катализатора приводят в контакт с синтез-газом, содержащим газообразный монооксид углерода и газообразный водород в качестве основных компонентов, для синтезирования углеводородов;
подводящий трубопровод синтез-газа, предназначенный для подачи синтез-газа в реактор;
устройство для нагрева текучей среды, расположенное в подводящем трубопроводе синтез-газа и предназначенное для нагрева текучей среды, протекающей через подводящий трубопровод синтез-газа;
средство детектирования, расположенное в подводящем трубопроводе синтез-газа, которое обнаруживает прекращение подачи синтез-газа в реактор;
первый двухпозиционный вентиль, расположенный в подводящем трубопроводе синтез-газа;
емкость резервного газа, в которой хранятся инертный газ или газообразный водород;
резервный подводящий трубопровод, предназначенный для подачи в реактор инертного газа или водорода, хранящихся в емкости резервного газа, при этом резервный подводящий трубопровод соединен с подводящим трубопроводом синтез-газа в промежутке между первым двухпозиционным вентилем и устройством для нагрева текучей среды;
второй двухпозиционный вентиль, расположенный в резервном подводящем трубопроводе; и
средство контроля, предназначенное для закрывания первого двухпозиционного вентиля и открывания второго двухпозиционного вентиля, когда средство детектирования обнаруживает прекращение подачи синтез-газа в реактор,
при этом упомянутое устройство для нагрева текучей среды также предназначено для нагрева инертного газа или газообразного водорода из емкости резервного газа, которые подают в реактор через резервный подводящий трубопровод синтез-газа, когда останавливают подачу синтез-газа в реактор.
2. Установка для реакции синтеза углеводородов по п.1, дополнительно включающая в себя теплообменную трубу, установленную внутри реактора, через которую осуществляется теплообмен с суспензией катализатора, при этом при синтезировании углеводородов внутри реактора по теплообменной трубе протекает жидкая среда для отвода тепла реакции, образовавшегося при синтезировании углеводородов, а когда подачу синтез-газа в реактор прекращают, жидкая среда нагревается и затем протекает по теплообменной трубе, нагревая суспензию катализатора в реакторе.
3. Реакционная система синтеза углеводородов для производства базовых компонентов жидкого топлива из углеводородного сырья, включающая в себя
установку для реакции синтеза углеводородов по п.1;
узел производства синтез-газа, предназначенный для риформинга углеводородного сырья с образованием синтез-газа и подачи синтез-газа в реактор установки для реакции синтеза углеводородов;
узел повышения качества, предназначенный для очищения углеводородов, полученных в реакторе установки для реакции синтеза углеводородов, с получением базовых компонентов жидкого топлива.
4. Способ синтеза углеводородов с помощью установки по п.1, включающий стадии, на которых
нагревают синтез-газ, содержащий газообразный монооксид углерода и газообразный водород в качестве основных компонентов, с помощью устройства для нагрева текучей среды;
подают синтез-газ, нагретый указанным устройством для нагрева текучей среды, в реактор, содержащий суспензию катализатора, содержащую частицы твердого катализатора, суспендированные в жидкости, через подводящий трубопровод синтез-газа, для того чтобы синтезировать углеводороды посредством приведения в контакт суспензии катализатора с синтез-газом в реакторе;
хранят инертный газ или газообразный водород в емкости резервного газа;
подают инертный газ или газообразный водород, хранящиеся в емкости резервного газа, в реактор через подающий трубопровод синтез-газа совместно с нагреванием инертного газа или газообразного водорода с помощью указанного устройства для нагрева текучей среды после прекращения подачи синтез-газа в реактор.
5. Способ по п.4, где инертный газ представляет собой газ, состоящий из любого газа из ряда азота, диоксида углерода, благородного газа, метана и этана или смесевого газа, в котором смешано большое число таких газов.
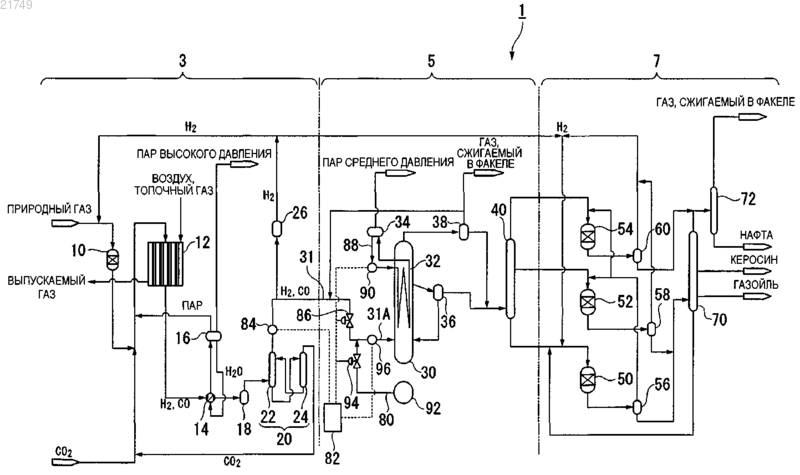
Текст
УСТАНОВКА ДЛЯ РЕАКЦИИ СИНТЕЗА УГЛЕВОДОРОДОВ, РЕАКЦИОННАЯ СИСТЕМА СИНТЕЗА УГЛЕВОДОРОДОВ И СПОСОБ СИНТЕЗА УГЛЕВОДОРОДОВ Изобретение относится к установке для реакции синтеза углеводородов, включающей в себя реактор и подводящий трубопровод синтез-газа, через который синтез-газ подают в реактор,и синтезирующей углеводороды контактированием синтез-газа и суспензии катализатора в реакторе. Установка для реакции синтеза углеводородов включает в себя резервный подводящий трубопровод, который соединен с подводящим трубопроводом синтез-газа и подает инертный газ или газообразный водород в реактор через подводящий трубопровод синтез-газа, когда подачу синтез-газа в подводящий трубопровод синтез-газа из подающего устройства синтез-газа останавливают; и устройство для нагрева текучей среды, которое нагревает по меньшей мере одну текучую среду из текучей среды, протекающей через проточный трубопровод подводящего трубопровода синтез-газа, расположенный ближе к реактору, чем часть, соединенная с резервным подводящим трубопроводом, и текучей среды, которая протекает через резервный подводящий трубопровод.(71)(73) Заявитель и патентовладелец: ДЖЭПЭН ОЙЛ, ГЭЗ ЭНД МЕТАЛЗ НЭШНЛ КОРПОРЕЙШН; ИНПЕКС КОРПОРЕЙШН; ДжейЭкс НИППОН ОЙЛ ЭНД ЭНЕРДЖИ КОРПОРЕЙШН; ДЖАПАН ПЕТРОЛЕУМ ЭКСПЛОРЕЙШН КО., ЛТД.; КОСМО ОЙЛ КО., ЛТД.; НИППОН СТИЛ ИНДЖИНИРИНГ КО., ЛТД. (JP) Область техники Настоящее изобретение относится к установке для реакции синтеза углеводородов, реакционной системе синтеза углеводородов и реакционному способу синтеза углеводородов. Приоритет заявлен японской патентной заявкой 2009-200346, направленной на рассмотрение 31 августа 2009 г., содержание которой включено в качестве ссылки. Уровень техники В последние годы в качестве одного из способов синтеза жидкого топлива из природного газа разработана технология GTL (Gas-To-Liquids, "газ-в-жидкость": синтез жидкого топлива). В технологииGTL природный газ подвергают риформингу с получением синтез-газа, содержащего газообразный водород (H2) и газообразный монооксид углерода (CO) в качестве основных компонентов, углеводороды синтезируют по реакции синтеза Фишера-Тропша (называемой далее в описании как "реакция синтеза ФТ") с помощью катализатора при использовании синтез-газа в качестве исходного газа и углеводороды гидрируют и фракционируют с получением продуктов жидкого топлива, таких как нафта (неочищенный бензин), керосин, газойль и воск. Обычно в качестве установки для реакции синтеза углеводородов, которая синтезирует углеводороды по реакции синтеза ФТ, известна конфигурация, включающая реактор, который наполнен суспензий катализатора, содержащей частицы твердого катализатора, суспендированные в жидкости, и подводящий трубопровод синтез-газа, через который синтез-газ, поданный из подающего устройства синтез-газа, которое подает синтез-газ, подают в реактор. В соответствии с такой установкой для реакции синтеза углеводородов углеводороды могут быть синтезированы по реакции синтеза ФТ контактированием синтезгаза с суспензией катализатора в реакторе. В упомянутой выше установке для реакции синтеза углеводородов давление в реакторе выше в сравнении с обычным давлением и температура в реакторе выше в сравнении с обычной температурой при реакции синтеза ФТ так что, реакцию синтеза ФТ проводят в реакторе спокойно. В таком типе установки для реакции синтеза углеводородов существует возможность, что подача синтез-газа в подводящий трубопровод синтез-газа из подающего устройства синтез-газа может быть остановлена, например, из-за неожиданных внешних факторов (землетрясение, прекращение подачи электроэнергии или др.). В этом случае могут возникать проблемы, показанные ниже, так как псевдоожиженное состояние суспензии катализатора в реакторе ухудшается. Во-первых, так как реакцию синтеза ФТ продолжают проводить с синтез-газом, оставшимся в реакторе, теплоту реакции, высвобожденную за счет экзотермической реакции, не отводят в достаточной степени из-за нарушения псевдоожиженного состояния суспензии катализатора, в суспензии катализатора временно образуется участок местного перегрева, и часть катализатора, вероятно, может быть отравлена из-за избыточного повышения температуры. В этом случае существует проблема в том, что выход при синтезе углеводородов по реакции синтеза Фишера-Тропша падает после возобновления процесса,при котором подача синтез-газа из подающего устройства синтез-газа была возобновлена, по сравнению с процессом до его остановки, при котором подача синтез-газа была прекращена. Более того, частицы катализатора могут забивать подводящий трубопровод синтез-газа. В этом случае существует проблема в том, что после возобновления процесса синтез-газ из подающего устройства синтез-газа подают в реактор неравномерно, а в худшем случае синтез-газ вообще не подается. Таким образом, например, как показано в приведенной ниже публикации, предложен способ подачи другого газа в реактор и обеспечения псевдоожиженного состояния суспензии катализатора в реакторе,когда подача синтез-газа в реактор была остановлена. Патентная литература.[PTL 1]. Описание патентной заявки США 2007-0093560. Суть изобретения Техническая проблема. Перепад внутренней температуры реактора не может быть подавлен просто путем подачи газа в реактор, и, когда внутренняя температура реактора становится ниже, чем точка замерзания окружающей жидкости суспензии катализатора, окружающая жидкость отверждается, и также трудно обеспечивать псевдоожиженное состояние суспензии катализатора. Изобретение выполнено с учетом упомянутых выше ситуаций, и цель изобретения состоит в разработке установки для реакции синтеза углеводородов, реакционной системы синтеза углеводородов и реакционного способа синтеза углеводородов, которые способны подавлять в реакторе перепад температур с целью обеспечения псевдоожиженного состояния суспензии катализатора и способны подавлять отравление катализатора с целью улучшения выхода при синтезе углеводородов после возобновления процесса, когда подача синтез-газа в реактор была остановлена. Решение проблемы. Для решения упомянутых выше проблем изобретение предлагает следующие средства. Установка для реакции синтеза углеводородов в соответствии с настоящим изобретением снабжена реактором, который наполнен суспензией катализатора, содержащей частицы твердого катализатора,суспендированные в жидкости, и подводящим трубопроводом синтез-газа, через который синтез-газ, по-1 021749 данный из подающего устройства синтеза-газа, которое подает синтез-газ, содержащий газообразный монооксид углерода и газообразный водород в качестве основных компонентов, подают в реактор; и синтезирует углеводороды за счет контактирования синтез-газа и суспензии катализатора в реакторе. Установка для реакции синтеза углеводородов включает в себя резервный подводящий трубопровод,который соединен с подводящим трубопроводом синтез-газа и подает инертный газ или газообразный водород в реактор через подводящий трубопровод синтез-газа, когда подача синтез-газа в подводящий трубопровод синтез-газа из подающего устройства синтез-газа остановлена; и устройство для нагрева текучей среды, которое нагревает по меньшей мере одну текучую среду из текучей среды, протекающей через проточный трубопровод подводящего трубопровода синтез-газа, расположенный ближе к реактору, чем часть, соединенная с резервным подводящим трубопроводом, и текучей среды, которая протекает через резервный подводящий трубопровод. Кроме того, реакционный способ синтеза углеводородов в соответствии с изобретением представляет собой реакционный способ синтеза углеводородов, синтезирующий углеводороды за счет контактирования синтез-газа и суспензии катализатора в реакторе при использовании установки для реакции синтеза углеводородов, включающей реактор, который наполнен суспензией катализатора, содержащей частицы твердого катализатора, суспендированные в жидкости, и подводящий трубопровод синтез-газа, через который синтез-газ, поданный из подающего устройства синтез-газа, которое подает синтез-газ, содержащий газообразный монооксид углерода и газообразный водород в качестве основных компонентов,подают в реактор. Реакционный способ синтеза углеводородов включает в себя нагревание инертного газа или газообразного водорода и подачу нагретого инертного газа или газообразного водорода в реактор через подводящий трубопровод синтез-газа, когда подачу синтез-газа в подводящий трубопровод синтез-газа из подающего устройства синтез-газа останавливают. В данном изобретении определение "инертный газ" означает газ, который не принимает участия в реакции в условиях реактора, осуществляет реакцию синтеза ФТ, химически не меняется и не влияет на катализатор для реакции синтеза ФТ. В соответствии с изобретением, так как включено устройство для нагрева текучей среды, инертный газ или газообразный водород, подаваемые в реактор из резервного подводящего трубопровода, когда подача синтез-газа в подводящий трубопровод синтез-газа из подающего устройства синтез-газа была остановлена, могут быть нагреты перед подачей в реактор, и в реактор могут быть поданы нагретый инертный газ или газообразный водород. Соответственно, существует возможность удерживать внутреннюю температуру реактора от перепада и гарантировать псевдоожиженное состояние суспензии катализатора и может быть подавлено отравление катализатора. Кроме того, так как перепад внутренней температуры реактора подавляют, даже если синтез-газ остается в реакторе, может быть сдержано образование карбонильных соединений металлов, которые отравляют катализатор. То есть, когда внутренняя температура реактора падает до температуры ниже, чем температура разложения карбонильных соединений металлов, существует вероятность того, что могут образовываться карбонильные соединения металлов, так как синтез-газ, который остается в реакторе,входит в контакт с железом, никелем или подобными металлами, составляющими сталь, которая образует реактор. Более того, так как инертный газ или газообразный водород в качестве компонента синтез-газа подают в реактор, когда подача синтез-газа была остановлена, может быть сдержано отравление катализатора благодаря текучей среде, поданной в реактор. Как обсуждено выше, когда подача синтез-газа в реактор была остановлена, есть возможность подавить отравление катализатора, а выход при синтезе углеводородов после возобновления процесса может быть улучшен. Кроме того, в установке для реакции синтеза углеводородов в соответствии с изобретением инертный газ может представлять собой газ, содержащий любой газ из числа азота, диоксида углерода, благородного газа, метана и этана или смешанного газа, в котором смешано большое число таких газов. В этом случае, так как инертный газ представляет собой газ, состоящий из любого газа из числа азота, диоксида углерода, благородного газа, метана и этана или смешанного газа, в котором смешано большое число таких газов, существует возможность надежно предупредить отравление благодаря контактированию инертного газа и частиц катализатора, а выход при синтезе углеводородов после возобновления процесса может быть дополнительно улучшен. Кроме того, в установке для реакции синтеза углеводородов в соответствии с изобретением может быть предусмотрено устройство для нагрева текучей среды с тем, чтобы нагреть текучую среду, которая протекает через проточный трубопровод. В этом случае, так как предусмотрено устройство для нагрева текучей среды с тем, чтобы нагреть текучую среду, которая протекает через проточный трубопровод, синтез-газ, подаваемый в подводящий трубопровод синтез-газа из подающего устройства синтез-газа, также может быть нагрет перед подачей в реактор в ходе нормального процесса. В результате даже в случае, где карбонильные соединения металлов, которые оказывают влияние на отравление катализатора, находятся в синтез-газе, синтез-газ может быть нагрет с помощью устройства для нагрева текучей среды до температуры выше, чем температура разложения карбонильных соединений металлов, чтобы разложить карбонильные соединения металлов и затем подать синтез-газ в реактор. Соответственно, существует возможность предотвращать отравление катализатора из-за карбонильных соединений металлов, находящихся в синтез-газе, а выход при синтезе углеводородов может быть дополнительно улучшен. Кроме того, пока синтез-газ подают в реактор из подающего устройства синтез-газа, синтез-газ вступает в контакт с железом, никелем или подобными металлами, составляющими сталь, которая образует установку для реакции синтеза углеводородов. В результате в синтез-газе могут образовываться карбонильные соединения металлов (например, карбонильное соединение железа или карбонильное соединение никеля), которые отравляют катализатор. Кроме того, установка для реакции синтеза углеводородов в соответствии с изобретением дополнительно может включать охлаждающее устройство, которое охлаждает содержимое реактора. Охлаждающее устройство может быть выполнено так, чтобы оно имело возможность переключения на нагревающее устройство, которое нагревает содержимое реактора, когда подачу синтез-газа в подводящий трубопровод синтез-газа из подающего устройства синтез-газа останавливают. В этом случае, так как включено охлаждающее устройство, даже в случае, где в реакторе протекает экзотермическая реакция, существует возможность предупреждать избыточное повышение внутренней температуры реактора. Кроме того, охлаждающее устройство выполнено так, чтобы оно имело возможность переключения на нагревающее устройство, которое нагревает содержимое реактора, когда подача синтез-газа в подводящий трубопровод синтез-газа из подающего устройства синтез-газа была остановлена. Следовательно,за счет нагревания содержимого реактора с помощью нагревающего устройства, когда подача синтезгаза была остановлена, существует возможность надежно подавлять неожиданный перепад внутренней температуры реактора и надежно подавлять отравление катализатора, а выход при синтезе углеводородов после возобновления процесса может быть дополнительно улучшен. Кроме того, установка для реакции синтеза углеводородов в соответствии с изобретением дополнительно может включать средство контроля, которое обнаруживает остановку подачи синтез-газа, чтобы подать инертный газ или газообразный водород в реактор через резервный подводящий трубопровод,когда подача синтез-газа в подводящий трубопровод синтез-газа из подающего устройства синтез-газа была остановлена. В этом случае, так как включено средство контроля, существует возможность надежно подавать инертный газ или газообразный водород в реактор через резервный подводящий трубопровод, когда подача синтез-газа в подводящий трубопровод синтез-газа из подающего устройства синтез-газа была остановлена, и неожиданный перепад внутреннего давления и температуры реактора может быть надежно подавлен. Соответственно, существует возможность надежно подавлять отравление катализатора, а выход при синтезе углеводородов после возобновления процесса может быть дополнительно улучшен. Кроме того, установка для реакции синтеза углеводородов в соответствии с изобретением представляет собой реакционную систему синтеза углеводородов, которая производит базовые компоненты жидкого топлива из углеводородного сырья. Система включает в себя установку для реакции синтеза углеводородов в соответствии с описанным выше изобретением и узел повышения качества, который очищает углеводороды, давая базовые компоненты жидкого топлива. Подающее устройство синтез-газа представляет собой узел производства синтез-газа, который подвергает риформингу углеводородное сырье с производством синтез-газа и подает синтез-газ в подводящий трубопровод синтез-газа. Установка для реакции синтеза углеводородов в соответствии с изобретением включает в себя установку для реакции синтеза углеводородов настоящего изобретения, в которой выход при синтезе углеводородов улучшен, когда процесс возобновляют после остановки подачи синтез-газа. Следовательно,установка для реакции синтеза углеводородов может улучшать выход при производстве базового компонента жидкого топлива из углеводородного сырья. Полезные эффекты изобретения. В соответствии с изобретением, когда подачу синтез-газа в реактор останавливают, перепад температуры в реакторе может быть подавлен, чтобы обеспечить псевдоожиженное состояние суспензии катализатора, и может быть подавлено отравление катализатора, чтобы улучшить выход при синтезе углеводородов после возобновления процесса. Краткое описание чертежей Фигура представляет собой принципиальную схему, показывающую общую конфигурацию системы синтеза жидкого топлива в соответствии с одним из вариантов осуществления настоящего изобретения. Наилучший способ осуществления изобретения Далее система синтеза жидкого топлива в соответствии с одним вариантом осуществления изобретения описана со ссылкой на фигуру. Как показано на фигуре, система синтеза жидкого топлива (реакционная система синтеза углеводородов) 1 представляет собой промышленную установку, которая осуществляет процесс GLT, в котором углеводородное сырье, такое как природный газ, превращается в жидкое топливо. Система синтеза жид-3 021749 кого топлива 1 включает в себя узел производства синтез-газа 3, узел синтеза ФТ (установка для реакции синтеза углеводородов) 5 и узел повышения качества 7. Узел производства синтез-газа 3 подвергает риформингу природный газ, который является углеводородным сырьем, с производством синтез-газа, содержащего газообразный монооксид углерода и газообразный водород. Узел синтеза ФТ 5 производит жидкие углеводороды из произведенного синтез-газа по реакции синтеза ФТ. Узел повышения качества 7 гидрирует и фракционно перегоняет жидкие углеводороды, произведенные по реакции синтеза ФТ, производя базовые компоненты продуктов жидкого топлива (нафта, керосин, газойль, воск или др.) (базовые компоненты жидкого топлива). Далее описаны составные части таких узлов. Во-первых, описан узел производства синтез-газа 3. Узел производства синтез-газа 3 преимущественно включает, например, реактор десульфуризации 10, риформинг-установку 12, котел-утилизатор 14,газожидкостные сепараторы 16 и 18, узел удаления CO2 20 и водородный сепаратор 26. Реактор десульфуризации 10 состоит из гидродесульфуризатора или подобного оборудования и удаляет серные компоненты из природного газа, который является исходным сырьем. Риформингустановка 12 подвергает риформингу природный газ, подаваемый из реактора десульфуризации 10, производя синтез-газ, содержащий газообразный монооксид углерода (CO) и газообразный водород (H2) в качестве основных компонентов. Котел-утилизатор 14 выделяет отходящее тепло синтез-газа, произведенного в риформинг-установке 12, чтобы генерировать пар высокого давления. Газожидкостной сепаратор 16 разделяет воду, нагретую за счет теплообмена с синтез-газом в котле-утилизаторе 14, на газ (пар высокого давления) и жидкость. Газожидкостной сепаратор 18 выводит сконденсированные фракции из синтез-газа, охлажденного в котле-утилизаторе 14, и подает газовый компонент в узел удаления CO2 20. Узел удаления CO2 20 включает в себя абсорбционную колонну 22, которая удаляет газообразный диоксид углерода за счет использования абсорбента из синтез-газа, поданного из газожидкостного сепаратора 18, и регенерационную колонну 24, которая диффундирует газообразный диоксид углерода из абсорбента, содержащего газообразный диоксид углерода, чтобы регенерировать абсорбент. Водородный сепаратор 26 отделяет часть газообразного водорода, находящегося в синтез-газе, из которого газообразный диоксид углерода был отделен с помощью узла удаления CO2 20. Следует отметить, что в зависимости от условий описанный выше узел удаления CO2 20 может быть не предусмотрен. Наряду с этим риформинг-установка 12 подвергает риформингу природный газ с использованием диоксида углерода и пара, чтобы получить высокотемпературный синтез-газ, содержащий газообразный монооксид углерода и газообразный водород в качестве основных компонентов, за счет способа парового и углекислотного риформинга, выраженного приведенными ниже схемами химических реакций (1) и (2). Кроме того, способ риформинга в риформинг-установке 12 не ограничен примером описанного выше способа парового и углекислотного риформинга. Например, также может быть использован способ парового риформинга, способ риформинга с неполным окислением (РОХ) с использованием кислорода, способ автотермического риформинга (ATR), который представляет собой комбинацию способа риформинга с неполным окислением и способа парового риформинга, способ углекислотного риформинга и т.д. Кроме того, водородный сепаратор 26 устанавливают на трубопроводе, ответвляющемся от подводящего трубопровода синтез-газа 31, который соединяет узел удаления CO2 20 или газожидкостной сепаратор 18 с барботажной реакционной колонной 30. Водородный сепаратор 26 может состоять, например,из устройства PSA водорода (Pressure Swing Adsorption, абсорбция с перепадом давления), которое осуществляет адсорбцию и десорбцию примесных газов, включенных в газообразный водород, за счет использования разности давлений. Устройство PSA водорода содержит адсорбенты (цеолитный адсорбент,активированный уголь, оксид алюминия, силикагель или подобные адсорбенты) внутри множества абсорбционных колонн (не показаны), которые расположены параллельно. Путем последовательно повторяющегося процесса, включающего повышение давления, адсорбцию, десорбцию (сброс давления) и продувку газообразного водорода, который включает в себя примесные газы, в каждой из адсорбционных колонн, высокочистый (например, приблизительно 99,999%) газообразный водород, отделенный от синтез-газа, можно непрерывно подавать в реактор. Кроме того, способ отделения газообразного водорода в водородном сепараторе 26 не ограничен примером способа абсорбции с колебаниями давления, как в описанном выше устройстве PSA водорода. Например, такими способами могут быть адсорбция сплавами, запасающими водород, мембранный способ разделения или их комбинация. Способ адсорбции сплавами, запасающими водород, представляет собой, например, технологию отделения газообразного водорода с использованием запасающего водород сплава (TiFe, LaNi5,TiFe0,7-0,9, Mn0,3-0,1, TiMn1,5 или подобными сплавами), имеющего свойство адсорбировать или испускать газообразный водород при его охлаждении или нагревании. За счет обеспечения большого числа адсорбционных колонн, в которых находится запасающий водород сплав, и поочередно повторяющихся в каждой из адсорбционных колонн адсорбции газообразного водорода путем охлаждения запасающего водо-4 021749 род сплава и выделения газообразного водорода за счет нагревания запасающего водород сплава газообразный водород в синтез-газе может быть отделен и извлечен. Кроме того, мембранный способ разделения представляет собой технологию отделения газообразного водорода, имеющего прекрасную мембранную проницаемость, из смешанных газов с использованием мембраны, изготовленной из полимерного материала, такого как ароматический полиимид. Так как такой мембранный способ разделения не сопровождается фазовым изменением, для работы требуется меньше энергии, и эксплуатационные расходы являются низкими. Кроме того, так как конструкция устройства для мембранного разделения является простой и компактной, требуются низкие затраты на оборудование, а также меньше необходимая для монтажа площадь. Кроме того, так как при мембранном разделении отсутствует приводное устройство, а стабильный рабочий диапазон является широким, есть преимущество простого технического обслуживания и управления. Узел производства синтез-газа 3, выполненный, как описано выше, работает как подающее устройство синтез-газа, которое подает синтез-газ в подводящий трубопровод синтез-газа 31 и подает синтезгаз в узел синтеза ФТ 5 через подводящий трубопровод синтез-газа 31. Далее описан узел синтеза ФТ 5. Узел синтеза ФТ 5 преимущественно включает, например, барботажную реакционную колонну 30, подводящий трубопровод синтез-газа 31, теплообменную трубу 32,газожидкостной сепаратор 34, сепаратор 36, газожидкостной сепаратор 38, первую ректификационную колонну 40, резервный подводящий трубопровод 80 и средство контроля 82. Барботажная реакционная колонна 30, которая представляет собой, например, реактор, который превращает синтез-газ в жидкие углеводороды (синтезирует жидкие углеводороды из синтез-газа), работает как реактор синтеза ФТ, который синтезирует жидкие углеводороды из синтез-газа по реакции синтеза ФТ. Барботажная реакционная колонна 30 состоит, например, из барботажной реакционной колонны со слоем суспензии, в которой суспензия катализатора, содержащая преимущественно частицы катализатора и окружающее масло, загружена в емкость колонны. Барботажная реакционная колонна 30 производит газообразные или жидкие углеводороды из синтез-газа по реакции синтеза ФТ. Подробно, синтез-газ,который является исходным газом, подаваемым из узла производства синтез-газа 3 (узла удаления CO2 20 или газожидкостного сепаратора 18), подают в барботажную реакционную колонну 30 через подводящий трубопровод синтез-газа 31. В данном случае в настоящем варианте осуществления подводящий трубопровод синтез-газа 31 подает синтез-газ от нижней части барботажной реакционной колонны 30 и выполнен так, что синтез-газ, поданный в барботажную реакционную колонну 30 через подводящий трубопровод синтез-газа 31, проходит через суспензию катализатора, загруженную в барботажную реакционную колонну 30, протекая вверх в суспензии. В барботажной реакционной колонне 30 синтез-газ, поданный из узла производства синтез-газа 3, подают в виде пузырьков из барботера у нижней части барботажной реакционной колонны 30, и он проходит через суспензию катализатора, и в суспендированном состоянии газообразный водород и газообразный монооксид углерода реагируют друг с другом по следующему уравнению химической реакции (3): Подводящий трубопровод синтез-газа 31 снабжен средством детектирования 84, которое обнаруживает остановку подачи синтез-газа из узла производства синтез-газа 3 в подводящий трубопровод синтезгаза 31, и первым двухпозиционным вентилем 86, который выполнен так, чтобы он был способен открывать и закрывать подводящий трубопровод синтез-газа 31, и который дает возможность узлу производства синтез-газа 3 (узлу удаления CO2 20 или газожидкостному сепаратору 18) и барботажной реакционной колонне 30 находиться во взаимодействии друг с другом или быть отключенными друг от друга. Средство детектирования 84 включает в себя расходомер (не показан), который измеряет расход синтез-газа, протекающего через подводящий трубопровод синтез-газа 31, и установлен так, чтобы обнаруживать, что подача синтез-газа из узла производства синтез-газа 3 в подводящий трубопровод синтезгаза 31 остановлена, например, в случае, когда расход синтез-газа, измеренный расходомером, падает ниже предварительно заданного нижнего предела. Кроме того, средство детектирования 84 устанавливают так, чтобы направить сигнал обнаружения к средству контроля 82, когда упомянутая выше остановка была обнаружена. Первый двухпозиционный вентиль 86 устанавливают в части подводящего трубопровода синтезгаза 31, которая расположена к барботажной реакционной колонне 30 ближе, чем любая соединенная часть между подводящим трубопроводом синтез-газа 31 и описанным выше ответвляющим трубопроводом и средством детектирования 84. Кроме того, положение открывания и закрывания первого двухпозиционного вентиля 86 контролируют с помощью средства контроля 82, и первый двухпозиционный вентиль 86 переведен в открытое положение в нормальный период, когда синтез-газ подают в подводящий трубопровод синтез-газа 31 из узла производства синтез-газа 3. Так как реакция синтеза ФТ является экзотермической реакцией, барботажная реакционная колонна 30 представляет собой тип теплообменника, который имеет теплообменную трубу 32, расположенную в ней. Например, воду (BFW: Boiler Feed Water - вода для подпитки котла) подают в теплообменную трубу 32 в качестве охладителя так, что теплота реакции упомянутой выше реакции синтеза ФТ может быть отведена в виде пара среднего давления за счет теплообмена между суспензией катализатора и водой. То есть, теплообменная труба 32 действует как охлаждающее устройство, которое охлаждает содержимое барботажной реакционной колонны 30. Так как узел синтеза ФТ 5 включает в себя теплообменную трубу 32, внутреннюю температуру барботажной реакционной колонны 30 во время реакции синтеза ФТ, т.е. реакционную температуру реакции синтеза ФТ, поддерживают приблизительно постоянной (например,230C). Газожидкостной сепаратор 34 разделяет воду, протекшую и нагретую через теплообменную трубу 32, расположенную внутри барботажной реакционной колонны 30, на пар (пар среднего давления) и жидкость. Кроме того, газожидкостной сепаратор 34 оборудован системой труб 88, через которую воду,отделенную в виде жидкости, подают в теплообменную трубу 32, и система труб 88 оборудована нагревателем 90, который нагревает воду (жидкость), протекающую через систему труб 88. В качестве нагревателя 90, например, может быть приспособлен теплообменник или подобное оборудование. Нагревание воды, которая протекает через систему труб 88, нагревателем 90 контролируют с помощью средства контроля 82. Кроме того, нагреватель 90 снабжают выделенным источником управления (не показан), независимым от других составных частей, и нагреватель 90 устанавливают так, чтобы он был способен работать (нагревать) даже в том случае, когда другие составные части были остановлены. Теплообменная труба 32, выполненная, как описано выше, адаптирована так, что может быть осуществлено переключение на нагревающее устройство, которое нагревает содержимое барботажной реакционной колонны 30, от охлаждающего устройства, которое охлаждает содержимое барботажной реакционной колонны 30, за счет нагревания воды, протекающей через систему труб 88, с помощью нагревателя 90. Сепаратор 36, который представляет собой пример фильтрующего устройства, которое разделяет частицы катализатора и жидкие углеводороды в суспензии катализатора, размещают снаружи барботажной реакционной колонны 30. Газожидкостной сепаратор 38 соединяют с верхней частью барботажной реакционной колонны 30, чтобы охлаждать непрореагировавший синтез-газ и газообразные углеводородные продукты. Первая ректификационная колонна 40 фракционно перегоняет жидкие углеводороды,подаваемые через сепаратор 36 и газожидкостной сепаратор 38, в отдельные фракции в соответствии с точками кипения. Кроме того, сепаратор 36 может быть размещен внутри барботажной реакционной колонны 30. Резервный подводящий трубопровод 80 соединяют с подводящим трубопроводом синтез-газа 31, и он подает инертный газ в барботажную реакционную колонну 30 через подводящий трубопровод синтезгаза 31, когда подача синтез-газа в подводящий трубопровод синтез-газа 31 из узла производства синтезгаза 3 была остановлена. Хотя газ, поданный, когда подача синтез-газа была остановлена, представляет собой инертный газ или газообразный водород, представленное ниже объяснение показывает пример с использованием инертного газа. В данном случае "инертный газ" означает газ, который не участвует в реакции в условиях реактора, который осуществляет реакцию синтеза ФТ, химически не меняется и не оказывает влияние на катализатор для реакции синтеза ФТ. Например, соответствующим образом может быть приспособлен газ, состоящий из любого газа из числа азота, диоксида углерода, благородного газа,метана и этана или смесевого газа, в котором смешано большое число таких газов. Один конец резервного подводящего трубопровода 80 соединен с частью подводящего трубопровода синтез-газа 31, которая расположена к барботажной реакционной колонне 30 ближе, чем первый двухпозиционный вентиль 86. Кроме того, емкость резервного газа 92, которая содержит инертный газ,хранящийся в ней, соединена с другим концом резервного подводящего трубопровода 80. Подводящий трубопровод синтез-газа 31 и емкость резервного газа 92 имеют возможность находиться во взаимодействии друг с другом с помощью резервного подводящего трубопровода 80, выполненного таким образом. Кроме того, внутреннее давление в емкости резервного газа 92 выше, чем наиболее высокое внутреннее давление, которое допустимо в барботажной реакционной колонне 30, когда синтез-газ подают в подводящий трубопровод синтез-газа 31 из узла производства синтез-газа 3 и осуществляют реакцию синтеза ФТ. Более того, резервный подводящий трубопровод 80 снабжают вторым двухпозиционным вентилем 94, который устанавливают так, чтобы он был способен открывать и закрывать резервный подводящий трубопровод 80 и позволял подводящему трубопроводу синтез-газа 31 и емкости резервного газа 92 находиться во взаимодействии друг с другом или быть отключенными друг от друга. Кроме того,положение открывания и закрывания второго двухпозиционного вентиля 94 контролируют с помощью средства контроля 82, и в нормальном состоянии второй двухпозиционный вентиль 94 закрыт. В соответствии с резервным подводящим трубопроводом 80 емкостью резервного газа 92 и вторым двухпозиционным вентилем 94, которые выполнены, как описано выше, в нормальном состоянии инертный газ не подают в барботажную реакционную колонну 30 из резервного подводящего трубопровода 80, так как второй двухпозиционный вентиль 94 находится в закрытом положении. Кроме того, в том случае, когда второй двухпозиционный вентиль 94 находится в открытом положении, внутреннее давление емкости резервного газа 92 является более высоким, чем наиболее высокое внутреннее давление в барботажной реакционной колонне 30, когда синтез-газ подают в подводящий трубопровод синтез-газа 31 из узла производства синтез-газа 3 и осуществляют реакцию синтеза ФТ. Поэтому инертный газ внут-6 021749 ри емкости резервного газа 92 поступает в барботажную реакционную колонну 30 из резервного подводящего трубопровода 80. В данном варианте осуществления узел синтеза ФТ 5 снабжают устройством для нагрева текучей среды 96, которое нагревает по меньшей мере одну текучую среду из текучей среды, которая протекает через проточный трубопровод 31 А подводящего трубопровода синтез-газа 31, который расположен к барботажной реакционной колонне 30 ближе, чем часть, соединенная с резервным подводящим трубопроводом 80, и текучей среды, которая протекает через резервный подводящий трубопровод 80. В проиллюстрированном примере устройство для нагрева текучей среды 96 выполнено так, чтобы нагреть текучую среду, которая протекает через описанный выше проточный трубопровод 31 А. В качестве устройства для нагрева текучей среды 96, например, может быть приспособлен теплообменник или подобное оборудование. Нагревание текучей среды, которая протекает через описанный выше проточный трубопровод 31 А, с помощью устройства для нагрева текучей среды 96 контролируют с помощью средства контроля 82. Кроме того, устройство для нагрева текучей среды 96 снабжают выделенным источником управления (не показан), независимым от других составных частей; и устройство для нагрева текучей среды 96 устанавливают так, чтобы оно было способно работать (нагревать) даже в том случае, когда другие составляющие части остановлены. Кроме того, устройство для нагрева текучей среды 96 устанавливают так, чтобы оно было способно нагревать синтез-газ, который подан из узла производства синтез-газа 3 и протекает через подводящий трубопровод синтез-газа 31, до температуры разложения или выше температуры разложения карбонильных соединений металлов. В данном варианте осуществления устройство для нагрева текучей среды 96 устанавливают так, чтобы оно было способно нагревать синтез-газ до температуры разложения или выше температуры разложения карбонильного соединения железа или карбонильного соединения никеля. Конкретно, устройство для нагрева текучей среды 96 устанавливают так, чтобы оно было способно нагревать синтез-газ до 140C или выше, предпочтительно до 140C или выше и температуры реакции синтеза ФТ или ниже, более предпочтительно до 200C или выше и реакционной температуры реакции синтеза ФТ или ниже. Когда подачу синтез-газа в подводящий трубопровод синтез-газа 31 из узла производства синтезгаза 3 останавливают, средство контроля 82 обнаруживает остановку, чтобы подать инертный газ в барботажную реакционную колонну 30 через резервный подводящий трубопровод 80. Работа средства контроля 82 будет описана подробнее при описании работы узла синтеза ФТ 5, который будет описан ниже. И, наконец, приведено описание узла повышения качества 7. Узел повышения качества 7 включает,например, реактор гидрокрекинга восковой фракции 50, реактор гидрообработки среднего дистиллята 52,реактор гидрообработки фракции нафты 54, газожидкостные сепараторы 56, 58 и 60, вторую ректификационную колонну 70 и стабилизатор нафты 72. Реактор гидрокрекинга восковой фракции 50 соединяют с нижней частью первой ректификационной колонны 40. Реактор гидрообработки среднего дистиллята 52 соединяют со средней частью первой ректификационной колонны 40. Реактор гидрообработки фракции нафты 54 соединяют с верхней частью первой ректификационной колонны 40. Газожидкостные сепараторы 56, 58 и 60 устанавливают так, чтобы они соответствовали реакторам гидрирования 50, 52 и 54 соответственно. Вторая ректификационная колонна 70 отгоняет жидкие углеводороды, поданные из газожидкостных сепараторов 56 и 58 в зависимости от их точек кипения. Стабилизатор нафты 72 фракционирует жидкие углеводороды фракции нафты, поданной из газожидкостного сепаратора 60 и второй ректификационной колонны 70, чтобы выделить бутан и компоненты, легче бутана, в виде сжигаемого в факеле газа и чтобы извлечь компоненты, содержащие число атомов углерода пять или больше, в виде продукта нафты. Далее описан процесс (процесс GTL) производства базовых компонентов жидкого топлива из природного газа с помощью системы синтеза жидкого топлива 1, выполненной, как описано выше. Природный газ (основным компонентом которого является CH4) в качестве углеводородного сырья подают в систему синтеза жидкого топлива 1 от внешнего источника подачи природного газа (не показан), такого как месторождение природного газа или газогенераторная установка. Описанный выше узел производства синтез-газа 3 подвергает риформингу природный газ, производя синтез-газ (смесевой газ,содержащий газообразный монооксид углерода и газообразный водород в качестве основных компонентов). Конкретно, во-первых, указанный выше природный газ подают в реактор десульфуризации 10 вместе с газообразным водородом, отделенным с помощью водородного сепаратора 26. Реактор десульфуризации 10 десульфуризирует природный газ за счет превращения соединений серы, находящихся в природном газе, в сульфид водорода с использованием газообразного водорода с помощью известного катализатора гидродесульфуризации и путем абсорбции полученного сульфида водорода абсорбентом, таким как ZnO. За счет десульфуризации природного газа таким путем может быть заранее предупреждено снижение активности катализатора, используемого в риформинг-установке 12, барботажной реакционной колонне 30 или подобном оборудовании, из-за соединений серы. Природный газ (также может содержать диоксид углерода), десульфуризированный таким путем,подают в риформинг-установку 12 после смешения диоксида углерода (CO2), поданного из источника подачи диоксида углерода (не показан), и пара, генерированного в котле-утилизаторе 14. Риформингустановка 12 подвергает природный газ риформингу с использованием диоксида углерода и пара, производя высокотемпературный синтез-газ, содержащий газообразный монооксид углерода и газообразный водород в качестве основных компонентов, за счет способа парового и углекислотного риформинга. Одновременно в риформинг-установку 12 подают, например, топочный газ для горелки, оборудованной в риформинг-установке 12, и воздух, и теплоту реакции, требуемую для указанной выше реакции парового и углекислотного риформинга, которая является эндотермической реакцией, обеспечивают за счет теплоты сгорания топочного газа в горелке. Высокотемпературный синтез-газ (например, 900C, 2,0 МПа), произведенный таким путем в риформинг-установке 12, подают в котел-утилизатор 14 и охлаждают с помощью теплообменника водой,которая протекает через котел-утилизатор 14 (например, 400C), отводя в результате отходящее тепло. Одновременно воду, нагретую синтез-газом в котле-утилизаторе 14, подают в газожидкостной сепаратор 16. Из газожидкостного сепаратора 16 газовый компонент подают в риформинг-установку 12 или другие внешние устройства в виде пара высокого давления (например, от 3,4 до 10,0 МПа), а воду в виде жидкого компонента возвращают в котел-утилизатор 14. Тем временем, синтез-газ, охлажденный в котле-утилизаторе 14, подают в абсорбционную колонну 22 узла удаления CO2 20 или в барботажную реакционную колонну 30 после отделения и удаления сконденсированных фракций в газожидкостном сепараторе 18. Абсорбционная колонна 22 удаляет газообразный диоксид углерода из синтез-газа путем абсорбирования газообразного диоксида углерода, находящегося в синтез-газе, с помощью абсорбента, загруженного в колонну. Содержащий газообразный диоксид углерода абсорбент внутри абсорбционной колонны 22 переносят в регенерационную колонну 24,абсорбент, содержащий газообразный диоксид углерода, нагревают и подвергают отпарке, например, с помощью пара, полученный диффузный газообразный диоксид углерода из регенерационной колонны 24 направляют в риформинг-установку 12 и используют повторно для описанной выше реакции риформинга. Синтез-газ, произведенный таким путем в узле производства синтез-газа 3, подают в барботажную реакционную колонну 30 описанного выше узла синтеза ФТ 5. Одновременно соотношение состава синтез-газа, поданного в барботажную реакционную колонну 30, доводят до соотношения состава, приемлемого для реакции синтеза ФТ (например, H2:CO=2:1 (мольное отношение. Кроме того, давление синтезгаза, поданного в барботажную реакционную колонну 30, повышают до давления, приемлемого для реакции синтеза ФТ (например, приблизительно 3,6 МПа), с помощью компрессора (не показан), установленного в подводящем трубопроводе синтез-газа 31. Кроме того, часть синтез-газа, из которого газообразный диоксид углерода отделен с помощью описанного выше узла удаления CO2 20, также подают в водородный сепаратор 26. Водородный сепаратор 26 отделяет газообразный водород, находящийся в синтез-газе, за счет адсорбции и десорбции (PSA водорода) с использованием разности давления, как описано выше. Отделенный газообразный водород непрерывно подают из газового резервуара или др. (не показан) через компрессор (не показан) к различным использующим водород реакционным устройствам в системе синтеза жидкого топлива 1 (например,в реактор десульфуризации 10, реактор гидрокрекинга восковой фракции 50, реактор гидрообработки среднего дистиллята 52, реактор гидрообработки фракции нафты 54 или др.), которые проводят заданные реакции за счет использования газообразного водорода. Далее, описанный выше узел синтеза ФТ 5 производит жидкие углеводороды по реакции синтеза ФТ из синтез-газа, произведенного в описанном выше узле производства синтез-газа 3. Конкретно, синтез-газ, из которого был отделен диоксид углерода в узле удаления CO2 20, протекает в барботажную реакционную колонну 30 через подводящий трубопровод синтез-газа 31. В данном случае синтез-газ, который протекает через подводящий трубопровод синтез-газа 31, охлаждают приблизительно до 40C с помощью теплообменника (не показан) перед его подачей в описанный выше узел удаления CO2 20. Таким образом, в данном варианте осуществления охлажденный синтез-газ нагревают с помощью устройства для нагрева текучей среды 96 с тем, чтобы температура синтез-газа была, например, 200C, когда синтез-газ подают в барботажную реакционную колонну 30. Затем нагретый синтез-газ протекает от нижней части барботажной реакционной колонны 30 и поднимается вверх в суспензии катализатора, загруженной в барботажную реакционную колонну 30. Одновременно внутри барботажной реакционной колонны 30 газообразный монооксид углерода и газообразный водород, которые находятся в синтез-газе, реагируют друг с другом по реакции синтеза ФТ,которая описана выше, давая в результате углеводород. Кроме того, за счет протекания воды через теплообменную трубу 32 в барботажной реакционной колонне 30 во время такой реакции синтеза отводят теплоту реакции от реакции синтеза ФТ и часть воды, нагретой с помощью такого теплообменника, испаряют в пар. Из пара и воды воду, отделенную в газожидкостном сепараторе 34, возвращают в теплообменную трубу 32, а газовый компонент направляют во внешние устройства в виде пара среднего давле-8 021749 ния (например, от 1,0 до 2,5 МПа). Жидкие углеводороды, синтезированные таким путем в барботажной реакционной колонне 30, выгружают в виде суспензии катализатора из средней части барботажной реакционной колонны 30 и переносят в сепаратор 36. Сепаратор 36 разделяет выгруженную суспензию на частицы катализатора (твердый компонент) и жидкий компонент, содержащий жидкий углеводородный продукт. Некоторую часть отделенных частиц катализатора возвращают в барботажную реакционную колонну 30, а жидкий компонент подают в первую ректификационную колонну 40. Из верхней части барботажной реакционной колонны 30 непрореагировавший синтез-газ и газовый компонент синтезированных углеводородов вводят в газожидкостной сепаратор 38. Газожидкостной сепаратор 38 охлаждает такие газы для отделения некоторой части сконденсированных жидких углеводородов, чтобы ввести их в первую ректификационную колонну 40. Тем временем, большую часть газового компонента, отделенного в газожидкостном сепараторе 38, преимущественно состоящего из непрореагировавшего синтез-газа и углеводородов С 4 и выше,возвращают в нижнюю часть барботажной реакционной колонны 30, и непрореагировавший синтез-газ в нем возвращают для реакции синтеза ФТ. Кроме того, остальной газовый компонент может быть использован в качестве топочного газа риформинг-установки 12 или может быть введен во внешнее оборудование сжигания (не показано), чтобы сжечь его там и затем сбросить в атмосферу. Далее, первая ректификационная колонна 40 фракционно перегоняет углеводороды (число атомов углерода которых разное), подаваемые через сепаратор 36 и газожидкостной сепаратор 38 из барботажной реакционной колонны 30, как описано выше, во фракцию нафты (температура кипения которой ниже чем приблизительно 150C), средний дистиллят, эквивалентный фракции керосина и газойля (температура кипения которого составляет приблизительно от 150 до 360C) и восковую фракцию (температура кипения которой превышает приблизительно 360C). Жидкие углеводороды восковой фракции, выгруженной из нижней части первой ректификационной колонны 40 (главным образом C21 или более), переносят в реактор гидрокрекинга восковой фракции 50. Жидкие углеводороды среднего дистиллята, эквивалентного фракции керосина и газойля, выгруженного из средней части первой ректификационной колонны 40 (преимущественно С 11-С 20), переносят в реактор гидрообработки среднего дистиллята 52. Жидкие углеводороды фракции нафты, выгруженной из верхней части первой ректификационной колонны 40(преимущественно С 5-С 10), переносят в реактор гидрообработки фракции нафты 54. Реактор гидрокрекинга восковой фракции 50 подвергает гидрокрекингу жидкие углеводороды восковой фракции с большим числом атомов углерода (приблизительно С 21 или более), которая была выгружена из нижней части первой ректификационной колонны 40, с использованием газообразного водорода, поданного из описанного выше водородного сепаратора 26, чтобы уменьшить число атомов углерода приблизительно до 20 или меньше. В реакции гидрокрекинга углеводороды с небольшим числом атомов углерода (с низкой молекулярной массой) производят путем расщепления связей С-С углеводородов с большим числом атомов углерода с использованием катализатора и тепла. Содержащий жидкие углеводороды продукт, полученный путем гидрокрекинга в реакторе гидрокрекинга восковой фракции 50, разделяют на газ и жидкость в газожидкостном сепараторе 56; и жидкие углеводороды переносят во вторую ректификационную колонну 70, а газовый компонент (содержащий газообразный водород) направляют в реактор гидрообработки среднего дистиллята 52 и реактор гидрообработки фракции нафты 54. Реактор гидрообработки среднего дистиллята 52 подвергает гидрообработке жидкие углеводороды среднего дистиллята, эквивалентного фракции керосина и газойля, имеющего среднее число атомов углерода (приблизительно С 11-С 20), который был выгружен из средней части первой ректификационной колонны 40, с использованием газообразного водорода, поданного через реактор гидрокрекинга восковой фракции 50 из водородного сепаратора 26. В реакции гидрообработки, чтобы получить главным образом разветвленные насыщенные углеводороды, жидкие углеводороды изомеризуют и присоединяют водород к ненасыщенным связям описанных выше жидких углеводородов для насыщения жидких углеводородов. В результате продукт, содержащий гидрообработанные жидкие углеводороды, разделяют на газ и жидкость в газожидкостном сепараторе 58, жидкие углеводороды переносят во вторую ректификационную колонну 70, а газовый компонент (содержащий газообразный водород) используют повторно для описанных выше реакций гидрирования. Реактор гидрообработки фракции нафты 54 подвергает гидрообработке жидкие углеводороды фракции нафты с небольшим числом атомов углерода (приблизительно С 10 или менее), которая поступает из верхней части первой ректификационной колонны 40, с использованием газообразного водорода,подаваемого через реактор гидрокрекинга восковой фракции 50 из водородного сепаратора 26. В результате продукт, содержащий гидрообработанные жидкие углеводороды, разделяют на газ и жидкость в газожидкостном сепараторе 60, жидкие углеводороды переносят в стабилизатор нафты 72, а газовый компонент (содержащий газообразный водород) используют повторно для описанных выше реакций гидрирования. Далее, вторая ректификационная колонна 70 фракционно перегоняет жидкие углеводороды, поданные из реактора гидрокрекинга восковой фракции 50 и реактора гидрообработки среднего дистиллята 52,-9 021749 описанные выше, на фракцию нафты, в которой число атомов углерода составляет приблизительно 10 или меньше (температура кипения которой ниже чем приблизительно 150C), фракцию керосина (температура кипения которой приблизительно от 150 до 250C), фракцию газойля (температура кипения которой приблизительно от 250 до 360C) и некрекированную восковую фракцию из реактора гидрокрекинга восковой фракции 50 (температура кипения которой не выше чем приблизительно 360C). Некрекированную восковую фракцию получают из нижней части второй ректификационной колонны 70 и рециркулируют вверх по направлению потока реактора гидрокрекинга восковой фракции 50. Фракцию керосина и фракцию газойля выгружают из средней части второй ректификационной колонны 70. Тем временем, углеводороды, где число атомов углерода составляет приблизительно 10 или менее, выгружают из верхней части второй ректификационной колонны 70 и направляют в стабилизатор нафты 72. Кроме того, стабилизатор нафты 72 фракционно перегоняет углеводороды, где число атомов углерода составляет приблизительно 10 или менее, которые были поданы из описанного выше реактора гидрообработки фракции нафты 54 и второй ректификационной колонны 70, с получением в виде продукта нафты (С 5-С 10). Соответственно, высокочистую нафту выгружают из нижней части стабилизатора нафты 72. Тем временем, газ, отличный от продуктов (топочный газ), который содержит углеводороды с числом атомов углерода, равным или меньшим, чем заданное число (равное или меньше чем С 4), в качестве основного компонента выгружают из верхней части стабилизатора нафты 72. Этот газ может быть использован в качестве топочного газа риформинг-установки 12 может быть выделен в виде сжиженного газа(LPG, не показано) и может быть введен во внешнее топочное оборудование (не показано), чтобы сжечь в нем и затем сбросить в атмосферу. Далее, в системе синтеза жидкого топлива 1, выполненной, как описано выше, описана работа (реакционный способ синтеза углеводородов) узла синтеза ФТ 5, когда подача синтез-газа в подводящий трубопровод синтез-газа 31 из узла производства синтез-газа 3 остановлена вследствие, например, неожиданных внешних факторов (землетрясение, прекращения подачи энергии или других факторов). Во-первых, проводят стадию детектирования, определяющую, что подача синтез-газа в подводящий трубопровод синтез-газа 31 из узла производства синтез-газа 3 остановлена. В настоящем варианте осуществления средство детектирования 84 определяет остановку подачи синтез-газа в подводящий трубопровод синтез-газа 31 из узла производства синтез-газа 3 и направляет сигнал определения на средство контроля 82. Затем, когда подача синтез-газа в подводящий трубопровод синтез-газа 31 из узла производства синтез-газа 3 была остановлена, выполняют стадию резервной подачи для подведения инертного газа в барботажную реакционную колонну 30 через подводящий трубопровод синтез-газа 31. В данном варианте осуществления средство контроля 82 обнаруживает остановку подачи синтез-газа из узла производства синтез-газа 3 на основе описанного выше сигнала определения и подает инертный газ в барботажную реакционную колонну 30 через резервный подводящий трубопровод 80. В этом случае средство контроля 82 переводит второй двухпозиционный вентиль 94 в открытое положение после переведения первого двухпозиционного вентиля 86 в закрытое положение, в результате инертный газ из емкости резервного газа 92 подают в барботажную реакционную колонну 30 через резервный подводящий трубопровод 80 и описанный выше проточный трубопровод 31 А подводящего трубопровода синтеза-газа 31. В этом случае в данном варианте осуществления первый двухпозиционный вентиль 86 переводят в закрытое положение. Таким образом, инертный газ не протекает в направлении узла производства синтез-газа 3 через подводящий трубопровод синтез-газа 31, и инертный газ может быть надежно подан в барботажную реакционную колонну 30. Затем, в данном варианте осуществления на стадии резервной подачи инертный газ нагревают, а затем подают в барботажную реакционную колонну 30. То есть, инертный газ, который проходит через описанный выше проточный трубопровод 31 А, нагревают с помощью устройства для нагрева текучей среды 96 и затем подают в барботажную реакционную колонну 30. Кроме того, в настоящем изобретении средство контроля 82 контролирует нагреватель 90, снабженный системой труб 88, переключая в результате теплообменную трубу 32 в нагревающее устройство,которое нагревает содержимое барботажной реакционной колонны 30, и нагревая содержимое барботажной реакционной колонны 30. То есть, теплообменная труба 32 выполнена так, чтобы она имела возможность переключения в нагревающее устройство, которое нагревает содержимое барботажной реакционной колонны 30, когда подача синтез-газа в подводящий трубопровод синтез-газа 31 из узла производства синтез-газа 3 была остановлена. Как показано выше, в соответствии с узлом синтеза ФТ 5, относящимся к данному варианту осуществления, так как включено устройство для нагрева текучей среды 96, инертный газ, поданный в барботажную реакционную колонну 30 через резервный подводящий трубопровод 80, когда подача синтез-газа в подводящий трубопровод синтез-газа 31 из узла производства синтез-газа 3 была остановлена, может быть нагрет перед тем, как его подадут в барботажную реакционную колонну 30, и в барботажную реакционную колонну 30 может быть подан нагретый инертный газ. Следовательно, существует возможность удерживать внутреннюю температуру барботажной реакционной колонны 30 от перепада и обеспечивать псевдоожиженное состояние суспензии катализатора, и отравление катализатора может быть подавлено. Кроме того, так как перепад внутренней температуры барботажной реакционной колонны 30 подавляют, можно предотвратить образование карбонильных соединений металлов, которые отравляют катализатор, даже если синтез-газ остается в барботажной реакционной колонне 30. То есть, когда внутренняя температура барботажной реакционной колонны 30 падает до температуры ниже, чем температура разложения карбонильных соединений металлов, существует вероятность того, что могут образоваться карбонильные соединения металлов, так как синтез-газ, оставшийся в барботажной реакционной колонне 30, вступает в контакт с железом, никелем или подобными металлами, составляющими сталь, которая образует барботажную реакционную колонну 30. Более того, так как инертный газ подают в барботажную реакционную колонну 30, когда подача синтез-газа была остановлена, может быть предотвращено отравление катализатора благодаря текучей среде, поданной в барботажную реакционную колонну 30. Как описано выше, когда подача синтез-газа в барботажную реакционную колонну 30 была остановлена, существует возможность надежно подавлять отравление катализатора, и выход при синтезе углеводородов после возобновления процесса может быть улучшен. Кроме того, так как инертный газ подают в барботажную реакционную колонну 30 через подводящий трубопровод синтез-газа 31, инертный газ, поданный в барботажную реакционную колонну 30, может проходить через суспензию катализатора, протекая за счет этого вверх аналогично синтез-газу при нормальном процессе. Следовательно, можно поддерживать суспендированное состояние суспензии катализатора с помощью инертного газа с тем же успехом, что и при реакции синтеза ФТ. Соответственно,частицы катализатора не оседают и не скапливаются, и предотвращено стекание суспензии катализатора назад к соединительному проходу между барботажной реакционной колонной 30 и подводящим трубопроводом синтез-газа 31 с блокировкой указанного выше соединительного прохода. В результате, когда работу узла синтеза ФТ 5 возобновляют, выход при синтезе углеводородов после возобновления процесса может быть дополнительно улучшен, не требуя времени для суспендирования частиц катализатора в окружающем масле до степени, приемлемой для реакции синтеза ФТ, или для удаления суспензии, которая блокировала указанный выше соединительный проход. Кроме того, инертный газ включает в себя газ, содержащий любой газ из числа азота, диоксида углерода, благородного газа, метана и этана или смесевого газа, в котором смешано большое число таких газов. В результате существует возможность надежно предупреждать отравление катализатора благодаря контактированию инертного газа и частиц катализатора. Следовательно, выход при синтезе углеводородов после возобновления процесса может быть дополнительно улучшен. Кроме того, так как установлено устройство для нагрева текучей среды 96 с тем, чтобы нагревать текучую среду, которая протекает через описанный выше проточный трубопровод 31 А, синтез-газ, поданный в подводящий трубопровод синтез-газа 31 из узла производства синтез-газа 3 в нормальном процессе, также может быть нагрет перед подачей в барботажную реакционную колонну 30. В результате,даже в случае, где карбонильные соединения металлов, которые оказывают влияние на катализатор, находятся в синтез-газе, синтез-газ может быть нагрет с помощью устройства для нагрева текучей среды 96, чтобы разложить карбонильные соединения металлов, а затем может быть подан в барботажную реакционную колонну 30. Соответственно, существует возможность предупредить отравление катализатора из-за карбонильных соединений металлов, находящихся в синтез-газе, и выход при синтезе углеводородов по реакции синтеза ФТ может быть дополнительно улучшен. Так как устройство для нагрева текучей среды 96 нагревает синтез-газ, который протекает через подводящий трубопровод синтез-газа 31 до 140C или выше, что является температурой разложенияFe3(CO)12 (додекакарбонилтрижелезо), карбонильное соединение железа или карбонильное соединение никеля, находящееся в синтез-газе внутри подводящего трубопровода синтез-газа 31, может быть надежно разложено. Кроме того, что касается температуры разложения других карбонильных соединений железа с более низким числом карбонильных групп, чем у Fe3(CO)12, то среди карбонильных соединений железа, например, температура разложения Fe3(CO)9 составляет приблизительно 100C, а температура разложения Fe3(CO)5 составляет приблизительно 77C. Более того, что касается температур разложения карбонильных соединений никеля, то, например, температура разложения Ni(CO)4 составляет приблизительно 127C. Все температуры разложения ниже или равны 140C. Более того, устройство для нагрева текучей среды 96 нагревает синтез-газ внутри подводящего трубопровода синтез-газа 31 до температуры реакции синтеза ФТ в барботажной реакционной колонне 30 или ниже, нагревая при этом синтез-газ до 140C или выше. Соответственно, когда нагретый синтез-газ подают в барботажную реакционную колонну 30, температуру содержимого барботажной реакционной колонны 30 излишне не повышают, и реакцию синтеза ФТ проводят стабильно. Следовательно, выход при синтезе углеводородов может быть дополнительно улучшен. Кроме того, так как включена теплообменная труба 32, существует возможность удерживать внутреннюю температуру барботажной реакционной колонны 30 от избыточного повышения за счет теплоты реакции от реакции синтеза ФТ. Кроме того, теплообменная труба 32 выполнена так, чтобы она имела возможность переключения в нагревающее устройство, которое нагревает содержимое барботажной реакционной колонны 30, когда подача синтез-газа в подводящий трубопровод синтез-газа 31 из узла производства синтез-газа 3 была остановлена. За счет нагревания содержимого барботажной реакционной колонны 30 с помощью теплообменной трубы 32, когда подача синтез-газа была остановлена, существует возможность надежно подавлять неожиданное падение внутренней температуры барботажной реакционной колонны 30 и надежно подавлять отравление катализатора. Следовательно, выход при синтезе углеводородов после возобновления процесса может быть дополнительно улучшен. Кроме того, так как включено средство контроля 82, когда подача синтез-газа в подводящий трубопровод синтез-газа 31 из узла производства синтез-газа 3 была остановлена, существует возможность надежно подавать инертный газ в барботажную реакционную колонну 30 через резервный подводящий трубопровод 80. Следовательно, внезапное падение внутреннего давления и внутренней температуры в барботажной реакционной колонне 30 может быть надежно подавлено. Соответственно, существует возможность надежно подавлять отравление катализатора, и выход при синтезе углеводородов после возобновления процесса может быть дополнительно улучшен. Кроме того, реакционная система синтеза углеводородов 1, описанная выше, включает в себя установку для реакции синтеза углеводородов, в которой выход при синтезе углеводородов улучшен, когда процесс возобновляют после остановки подачи синтез-газа. Следовательно, реакционная система синтеза углеводородов 1 может улучшать выход при производстве базового компонента жидкого топлива из углеводородного сырья. Хотя предпочтительный вариант осуществления настоящего изобретения описан со ссылкой на прилагаемый чертеж, изобретение не ограничено такими вариантами осуществления. Специалисту в данной области техники очевидно, что различные изменения и модификации могут быть выполнены в классе, который представлен в формуле изобретения, и будет понятно, что такие изменения и модификации естественно принадлежат к техническому объему изобретения. Например, в описанном выше варианте осуществления природный газ используют в качестве водородного сырья, которое подают в систему синтеза жидкого топлива 1. Однако изобретение не ограничено таким примером. Например, может быть использовано другое углеводородное сырье, такое как асфальт и нефтяной остаток. В описанном выше варианте осуществления синтез углеводородов по реакции синтеза ФТ описан как реакция синтеза в барботажной реакционной колонне 30. Однако технология, связанная с изобретением, не ограничена этим примером, и эта технология применима к другим реакциям синтеза в барботажной реакционной колонне с использованием синтез-газа в качестве исходного сырья. Как реакции синтеза целевых продуктов, отличных от углеводородов, в барботажной реакционной колонне с использованием синтез-газа в качестве исходного сырья, могут иметь место такие примеры, как реакция оксосинтеза (реакция гидроформилирования, R-CH=CH2+CO+H2R-CH2CH2CHO), реакция синтеза метанола (CO+2H2CH3OH), реакция синтеза диметилового эфира (ДМЭ, DME) (3CO+3H2CH3OCH3+CO2). Средство детектирования 84 не ограничено приведенным выше вариантом осуществления, пока оно обнаруживает остановку подачи синтез-газа из узла производства синтез-газа 3 в подводящий трубопровод синтез-газа 31. Например, средство детектирования 84 может быть установлено в узле удаления CO2 20 и может определять, что подача синтез-газа из узла производства синтез-газа 3 была остановлена, когда остановлена работа узла удаления CO2 20. Кроме того, средство детектирования 84 может быть не предусмотрено. В описанном выше варианте осуществления, хотя устройство для нагрева текучей среды 96 нагревает текучую среду, которая протекает через описанный выше проточный трубопровод 31 А, устройство для нагрева текучей среды не ограничено этим. Например, устройство для нагрева текучей среды 96 может нагревать текучую среду, которая протекает через резервный подводящий трубопровод 80. Кроме того, устройство для нагрева текучей среды может нагревать как текучую среду, которая протекает через описанный выше проточный трубопровод 31 А, так и текучую среду, которая протекает через резервный подводящий трубопровод 80. Более того, температура, до которой устройство для нагрева текучей среды 96 нагревает синтез-газ, который протекает через описанный выше проточный трубопровод 31 А, не ограничено температурой, показанной в упомянутом выше варианте осуществления. В описанном выше варианте осуществления теплообменная труба 32 выполнена с возможностью переключения нагревающего устройства, которое нагревает содержимое барботажной реакционной колонны 30, на охлаждающее устройство, которое охлаждает содержимое барботажной реакционной колонны 30, когда подача синтез-газа из узла производства синтез-газа 3 в подводящий трубопровод синтез-газа 31 была остановлена. Например, теплообменная труба 32 может функционировать только как охлаждающее устройство, которое охлаждает содержимое барботажной реакционной колонны 30. Кроме того, форма охлаждающего устройства, которое охлаждает содержимое барботажной реакционной колонны 30, не ограничено теплообменной трубой 32, показанной в описанном выше варианте осуществления. Хотя описанный выше вариант осуществления включает в себя первый двухпозиционный вентиль 86, первый двухпозиционный вентиль 86 может быть не предусмотрен. В описанном выше варианте осуществления емкость резервного газа 92 соединена с резервным подводящим трубопроводом 80, а второй двухпозиционный вентиль 94 оборудован на резервном подводящем трубопроводе 80. Однако резервный подводящий трубопровод 80 не ограничен этим, если резервный подводящий трубопровод соединен с подводящим трубопроводом синтез-газа 31 и подает инертный газ в барботажную реакционную колонну 30 через подводящий трубопровод синтез-газа 31, когда подачу синтез-газа из узла производства синтез-газа 3 в подводящий трубопровод синтез-газа 31 останавливают. Например, подающее устройство, такое как насос, может быть установлено в резервном подводящем трубопроводе 80, и инертный газ в емкости резервного газа 92 может быть подан в барботажную реакционную колонну 30. Кроме того, вместо емкости резервного газа 92 узел выработки инертного газа, который вырабатывает инертный газ, может быть соединен с упомянутым выше другим концом резервного подводящего трубопровода 80. В упомянутом выше варианте осуществления, когда подача синтез-газа из узла производства синтез-газа 3 в подводящий трубопровод синтез-газа 31 была остановлена, инертный газ подают в барботажную реакционную колонну 30. Однако вместо этого такой же эффект, как и этот, может быть получен, когда подают газообразный водород, который является компонентом синтез-газа. В этом случае газообразный водород можно хранить в емкости резервного газа 92. В этом случае используемый газообразный водород может представлять собой газообразный водород, который был отделен в водородном сепараторе 26 от синтез-газа, произведенного в узле производства синтез-газа 3, или непрореагировавший газообразный водород, который был выгружен и выделен с установок реакции гидрирования в узле повышения качества 7; и конфигурация может быть выполнена так, чтобы обеспечить возможность подачи такого газообразного водорода в барботажную реакционную колонну через резервный подводящий трубопровод 80. Хотя описанный выше вариант осуществления включает в себя средство контроля 82, средство контроля 82 может быть не предусмотрено. Например, может быть установлен узел управления, который приводит в действие первый двухпозиционный вентиль 86, второй двухпозиционный вентиль 94 и устройство для нагрева текучей среды 96; и когда подача синтез-газа из узла производства синтез-газа 3 в подводящий трубопровод синтез-газа 31 остановлена, нагретый синтез-газ может быть подан в барботажную реакционную колонну 30, когда оператор системы синтеза жидкого топлива 1 вводит в действие первый двухпозиционный вентиль 86, второй двухпозиционный вентиль 94 и устройство для нагрева текучей среды 96 с использованием описанного выше узла управления. Промышленное применение В соответствии с установкой для реакции синтеза углеводородов, реакционной системой синтеза углеводородов и реакционным способом синтеза углеводородов настоящего изобретения, когда подача синтез-газа в реактор была остановлена, может быть подавлено падение температуры в реакторе, чтобы сохранить псевдоожиженное состояние суспензии катализатора, и может быть подавлено отравление катализатора, чтобы улучшить выход при синтезе углеводородов после возобновления процесса. Список справочных позиций: 1 - система синтеза жидкого топлива (реакционная система синтеза углеводородов); 3 - узел производства синтез-газа (подающее устройство синтез-газа); 5 - узел синтеза ФТ (установка для реакции синтеза углеводородов); 7 - узел повышения качества; 30 - барботажная реакционная колонна (реактор); 31 - подводящий трубопровод синтез-газа; 31 А - проточный трубопровод; 32 - теплообменная труба (охлаждающее устройство, нагревающее устройство); 80 - резервный подводящий трубопровод; 82 - средство контроля; 96 - устройство для нагрева текучей среды. ФОРМУЛА ИЗОБРЕТЕНИЯ 1. Установка для реакции синтеза углеводородов, включающая в себя реактор, предназначенный для заполнения суспензией катализатора, содержащей частицы твердого катализатора, суспендированные в жидкости, в котором суспензию катализатора приводят в контакт с синтез-газом, содержащим газообразный монооксид углерода и газообразный водород в качестве основных компонентов, для синтезирования углеводородов; подводящий трубопровод синтез-газа, предназначенный для подачи синтез-газа в реактор; устройство для нагрева текучей среды, расположенное в подводящем трубопроводе синтез-газа и предназначенное для нагрева текучей среды, протекающей через подводящий трубопровод синтез-газа; средство детектирования, расположенное в подводящем трубопроводе синтез-газа, которое обнаруживает прекращение подачи синтез-газа в реактор; первый двухпозиционный вентиль, расположенный в подводящем трубопроводе синтез-газа; емкость резервного газа, в которой хранятся инертный газ или газообразный водород; резервный подводящий трубопровод, предназначенный для подачи в реактор инертного газа или водорода, хранящихся в емкости резервного газа, при этом резервный подводящий трубопровод соединен с подводящим трубопроводом синтез-газа в промежутке между первым двухпозиционным вентилем и устройством для нагрева текучей среды; второй двухпозиционный вентиль, расположенный в резервном подводящем трубопроводе; и средство контроля, предназначенное для закрывания первого двухпозиционного вентиля и открывания второго двухпозиционного вентиля, когда средство детектирования обнаруживает прекращение подачи синтез-газа в реактор,при этом упомянутое устройство для нагрева текучей среды также предназначено для нагрева инертного газа или газообразного водорода из емкости резервного газа, которые подают в реактор через резервный подводящий трубопровод синтез-газа, когда останавливают подачу синтез-газа в реактор. 2. Установка для реакции синтеза углеводородов по п.1, дополнительно включающая в себя теплообменную трубу, установленную внутри реактора, через которую осуществляется теплообмен с суспензией катализатора, при этом при синтезировании углеводородов внутри реактора по теплообменной трубе протекает жидкая среда для отвода тепла реакции, образовавшегося при синтезировании углеводородов, а когда подачу синтез-газа в реактор прекращают, жидкая среда нагревается и затем протекает по теплообменной трубе, нагревая суспензию катализатора в реакторе. 3. Реакционная система синтеза углеводородов для производства базовых компонентов жидкого топлива из углеводородного сырья, включающая в себя установку для реакции синтеза углеводородов по п.1; узел производства синтез-газа, предназначенный для риформинга углеводородного сырья с образованием синтез-газа и подачи синтез-газа в реактор установки для реакции синтеза углеводородов; узел повышения качества, предназначенный для очищения углеводородов, полученных в реакторе установки для реакции синтеза углеводородов, с получением базовых компонентов жидкого топлива. 4. Способ синтеза углеводородов с помощью установки по п.1, включающий стадии, на которых нагревают синтез-газ, содержащий газообразный монооксид углерода и газообразный водород в качестве основных компонентов, с помощью устройства для нагрева текучей среды; подают синтез-газ, нагретый указанным устройством для нагрева текучей среды, в реактор, содержащий суспензию катализатора, содержащую частицы твердого катализатора, суспендированные в жидкости, через подводящий трубопровод синтез-газа, для того чтобы синтезировать углеводороды посредством приведения в контакт суспензии катализатора с синтез-газом в реакторе; хранят инертный газ или газообразный водород в емкости резервного газа; подают инертный газ или газообразный водород, хранящиеся в емкости резервного газа, в реактор через подающий трубопровод синтез-газа совместно с нагреванием инертного газа или газообразного водорода с помощью указанного устройства для нагрева текучей среды после прекращения подачи синтез-газа в реактор. 5. Способ по п.4, где инертный газ представляет собой газ, состоящий из любого газа из ряда азота,диоксида углерода, благородного газа, метана и этана или смесевого газа, в котором смешано большое число таких газов.
МПК / Метки
МПК: C10G 45/00, C10G 2/00
Метки: углеводородов, реакции, система, синтеза, реакционная, установка, способ
Код ссылки
<a href="https://eas.patents.su/16-21749-ustanovka-dlya-reakcii-sinteza-uglevodorodov-reakcionnaya-sistema-sinteza-uglevodorodov-i-sposob-sinteza-uglevodorodov.html" rel="bookmark" title="База патентов Евразийского Союза">Установка для реакции синтеза углеводородов, реакционная система синтеза углеводородов и способ синтеза углеводородов</a>
Предыдущий патент: Разъединительная установка и связанный с ней способ отделения
Следующий патент: Способ декодирования, декодирующее устройство, способ кодирования и кодирующее устройство
Случайный патент: Магнитный ударник