Способ превращения низших алканов в ароматические углеводороды
Номер патента: 22683
Опубликовано: 29.02.2016
Авторы: Ийер Махеш Венкатараман, Лауритзен Анн Мари, Мадгавкар Аджай Мадхав
Формула / Реферат
1. Способ получения ароматических углеводородов, который включает:
(a) контакт сырья на основе низшего алкана с катализатором ароматизации в условиях реакции ароматизации в реакторе в течение периода времени, составляющего 30 мин или менее, с получением продуктов реакции ароматизации и затем контакт катализатора ароматизации с водородсодержащим газом при повышенной температуре в течение периода времени, составляющего 30 мин или менее;
(b) повтор стадии (а) по крайней мере один раз;
(c) регенерацию катализатора ароматизации через контакт с кислородсодержащим газом при повышенной температуре;
(g) повтор стадий (а)-(с) по крайней мере один раз.
2. Способ по п.1, где на стадии (а) сырье на основе низшего алкана приводят в контакт с катализатором ароматизации в течение периода времени, составляющего 20 мин или менее, предпочтительно 10 мин или менее.
3. Способ по п.1 или 2, где на стадии (а) катализатор ароматизации приводят в контакт с водородсодержащим газом в течение периода времени, составляющего 20 мин или менее, предпочтительно 10 мин или менее.
4. Способ по пп.1-3, где способ проводят по крайней мере в трех реакторах, установленных параллельно, и по крайней мере один реактор работает в режиме стадии (с), и по крайней мере два реактора работают в режиме стадии (а), и по крайней мере в одном реакторе по крайней мере из двух реакторов, работающих в режиме стадии (а), катализатор ароматизации контактирует с сырьем на основе низшего алкана, и по крайней мере в одном по крайней мере из двух реакторов, работающих в режиме стадии (а), катализатор ароматизации контактирует с водородом.
5. Способ по пп.1-4, где способ проводят по крайней мере в четырех реакторах, поставленных параллельно, и по крайней мере один реактор работает в режиме стадии (с), и по крайней мере три реактора работают в режиме стадии (а), и по крайней мере в одном из последних по крайней мере трех реакторов, работающих в режиме стадии (а), катализатор ароматизации контактирует с сырьем на основе низшего алкана, и по крайней мере в одном из последних по крайней мере трех реакторов, работающих в режиме стадии (а), катализатор ароматизации контактирует с водородсодержащим газом.
6. Способ по пп.1-5, где стадию (а) проводят при 400-700°С, давлении 0,01-1,0 МПа и среднечасовой скорости подачи сырья 300-6000 ч-1.
7. Способ по пп.1-6, где стадию (с) проводят при 400-700°С, предпочтительно 400-550°С.
8. Способ по пп.1-7, где кислородсодержащим газом на стадии (с) является воздух.
9. Способ по пп.1-8, где после стадии (с) регенерированный катализатор подвергают повторному нанесению металла, предпочтительно оксихлорированием.
10. Способ по пп.1-9, где после стадии (с) регенерированный катализатор восстанавливают предпочтительно водородсодержащим газом.
11. Способ по пп.1-10, где после стадии (с) регенированный катализатор сульфидируют.
12. Способ получения ароматических углеводородов, который включает:
(a) подачу сырья на основе низшего алкана, содержащего, по крайней мере, пропан и этан или пропан и/или бутан;
(b) контакт сырья на основе низшего алкана с катализатором ароматизации первой стадии в реакторе в течение периода времени, составляющего 30 мин или менее, в условиях реакции первой стадии, которые максимизируют превращение пропана и/или любого другого высшего углеводорода, присутствующего в потоке, в продукты реакции ароматизации первой стадии и затем контакт катализатора ароматизации первой стадии с водородсодержащим газом при повышенной температуре в течение периода времени, составляющего 30 мин;
(c) повтор стадии (b) по крайней мере один раз;
(d) регенерацию катализатора ароматизации первой стадии через контакт с кислородсодержащим газом при повышенной температуре;
(h) повтор стадий (а)-(d) по крайней мере один раз;
(i) отделение продуктов первой ароматической реакции от непрореагировавшего и/или побочного этана;
(j) контакт непрореагировавшего и/или побочного этана со стадии (i) с катализатором ароматизации со второй стадии в реакторе в течение периода времени, составляющего 30 мин или менее, в условиях реакции второй стадии, что максимизирует превращение этана в продукты ароматической реакции второй стадии, и затем контакт катализатора ароматизации второй стадии с водородсодержащим газом при повышенной температуре в течение периода времени, составляющего 30 мин или менее;
(k) повтор стадии (j) по крайней мере один раз;
(l) регенерацию катализатора ароматизации второй стадии через контакт с кислородсодержащим газом при повышенной температуре;
(р) повтор стадий (j)-(l) по крайней мере один раз.
13. Способ по п.12, где на стадии (b) сырье на основе низшего алкана приводят в контакт с катализатором ароматизации первой стадии в течение периода времени, составляющего 20 мин или менее, предпочтительно 10 мин или менее.
14. Способ по пп.12 и 13, где на стадии (b) катализатор ароматизации первой стадии приводят в контакт с водородсодержащим газом в течение периода времени, составляющего 20 мин или менее, предпочтительно 10 мин или менее.
15. Способ по пп.12-14, где на стадии (j) непрореагировавший и/или побочный этан со стадии (i) приводят в контакт с катализатором ароматизации второй стадии в течение периода времени, составляющего 20 мин или менее, предпочтительно 10 мин или менее.
16. Способ по пп.12-15, где на стадии (j) катализатор ароматизации второй стадии приводят в контакт с водородсодержащим газом в течение периода времени, составляющего 20 мин или менее, предпочтительно 10 мин или менее.
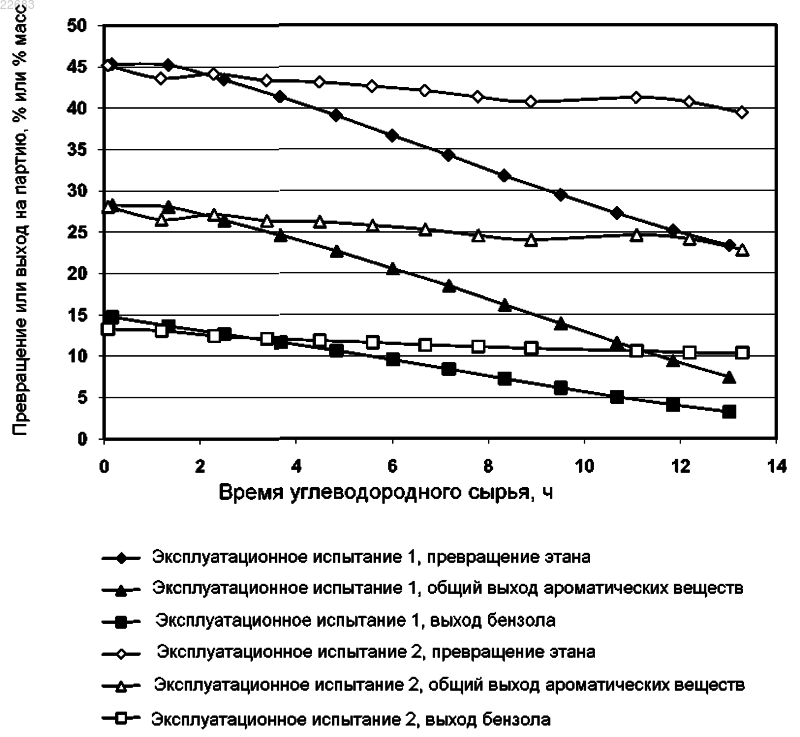
Текст
СПОСОБ ПРЕВРАЩЕНИЯ НИЗШИХ АЛКАНОВ В АРОМАТИЧЕСКИЕ УГЛЕВОДОРОДЫ В изобретении представлен способ получения ароматических углеводородов, который включает(а) попеременный контакт потока низшего алкана с катализатором ароматизации в условиях реакции ароматизации в реакторе в течение короткого периода времени, предпочтительно около 30 мин, с получением продуктов реакции ароматизации, затем контакт катализатора ароматизации с водородсодержащим газом при повышенной температуре в течение короткого периода времени,предпочтительно около 10 мин или меньше; (b) повтор цикла со стадии (а) по крайней мере один раз; (с) регенерацию катализатора ароматизации через контакт с кислородсодержащим газом при повышенной температуре и (d) повтор стадий (а)-(с) по крайней мере один раз. Ийер Махеш Венкатараман,Лауритзен Анн Мари, Мадгавкар Аджай Мадхав (US) Медведев В.Н. (RU)(71)(73) Заявитель и патентовладелец: ШЕЛЛ ИНТЕРНЭШНЛ РИСЕРЧ МААТСХАППИЙ Б.В. (NL) Область техники Данное изобретение относится к способу получения ароматических углеводородов из низших алканов. Более конкретно, изобретение относится к способу повышения производительности катализатора ароматизации в процессе дегидроароматизации. Уровень техники Существует расчетный глобальный дефицит бензола, который необходим для производства ключевых нефтехимических продуктов, таких как стирол, фенол, нейлон и полиуретаны, среди прочих. В общем бензол и другие ароматические углеводороды получают отделением фракции исходного сырья, которая насыщена ароматическими соединениями, такой как риформат, полученный в процессе каталитического риформинга, и пиробензины, полученные в процессе крекирования сырой нефти, от неароматических углеводородов с применением селективной экстракции. Для сокращения расчетного дефицита исследовали множество катализаторов и процессов намеренного производства ароматических соединений (включая бензол) из алканов, содержащих шесть или менее атомов углерода в молекуле. Эти катализаторы обычно являются бифункциональными, содержат цеолит или молекулярные сита для обеспечения кислотности и один или более металлов, таких как Pt,Ga, Zn, Mo и т.д., для удаления водорода. Например, в патенте США 4350835 описан способ превращения этансодержащего газообразного сырья в ароматические соединения с применением кристаллического цеолитного катализатора семейства ZSM-5, содержащего незначительное количество Ga. В другом примере в патенте США 7186871 описана ароматизация С 1-С 4-алканов с применением катализатора, содержащего Pt и ZSM-5. По прошествии некоторого времени применения в реакции ароматизации катализатор становится деактивированным в результате таких процессов, как отложение нагара на частицах катализатора. Нагар состоит преимущественно из углерода, но также содержит небольшое количество водорода. Нагар снижает способность катализатора обеспечивать реакции дегидроароматизации до той степени, что продолжительное применение катализатора становится не практичным и не экономичным. В этот момент катализатор необходимо восстановить или регенерировать до того, как он сможет быть использован повторно. Множество способов регенерации катализатора описано в патентной литературе, и практически все включают до некоторой степени сжигание нагара с поверхности катализатора. Конкретный метод регенерации, который применяется в конкретном способе, зависит от состава слоя(ев) катализатора в реакторе(ах). Неподвижные слои катализатора содержат катализатор постоянно. Когда катализатор в реакторе с неподвижным слоем деактивирован, реактор обычно временно останавливают и катализатор либо регенерируют на месте, либо выгружают и заменяют на регенерированный или свежий катализатор. Коммерчески применяют для способа регенерации неподвижного слоя циклическую регенерацию и полурегенерацию. В способе циклической регенерации по крайней мере один или, самое большее, не все реакторы останавливают в любое время и процесс продолжают в оставшихся реакторах. После регенерации деактивированного катализатора реактор включают обратно, что, в свою очередь, позволяет остановить другой реактор для регенерации катализатора. Ароматизация низшего алкана является высокоэндотермической реакцией, которая термодинамически проходит при высокой температуре и низком давлении. К сожалению, эти условия также способствуют образованию поверхностного нагара, который быстро деактивирует катализатор. Отложения нагара могут быть частично или полностью удалены высокотемпературной десорбцией катализатора с применением потока водородсодержащего газа или пара, или с применением кислородсодержащего газа для сжигания накопившегося нагара. Сжигание нагара обычно предпочтительно для полного удаления накопившегося нагара, но оно должно проходить относительно медленно при тщательном контроле для того, чтобы избежать избыточного увеличения температуры, которое может привести к необратимой потере площади поверхности активного катализатора. Срок эксплуатации катализатора значительно сокращается, если катализатор подвергают множеству операций высокотемпературного сжигания нагара между прохождением сырья на основе низшего алкана и условиями ароматизации. Предпочтительно разработать способ получения дегидроароматизации легкого алкана, в котором могут быть минимизированы (а) деактивация катализатора из-за образования нагара и (b) побочное действие высокотемпературного сжигания нагара. Сущность изобретения В данном изобретении представлен способ получения ароматических углеводородов, который включает:(a) попеременный контакт потока низшего алкана с катализатором ароматизации в условиях реакции ароматизации в реакторе в течение короткого периода времени, предпочтительно около 30 мин, с получением продуктов реакции ароматизации, затем контакт катализатора ароматизации с водородсодержащим газом при повышенной температуре в течение короткого периода времени, предпочтительно около 30 мин или меньше;(b) повтор цикла со стадии (а) по крайней мере один раз;(c) регенерацию катализатора ароматизации через контакт с кислородсодержащим газом при повышенной температуре;(d) необязательное повторное распыление металла на регенерированный катализатор ароматизации;(e) необязательное восстановлении регенерированного катализатора ароматизации предпочтительно водородсодержащим газом;(f) необязательное сульфидирование катализатора и(g) повтор стадий (a)-(f) по крайней мере один раз. В одном варианте способ проводят по крайней мере в трех реакторах, предпочтительно в реакторах с неподвижным слоем, поставленных параллельно, и в любой момент времени по крайней мере один реактор работает согласно стадии способа (с), и по крайней мере два реактора работают согласно стадии(а), и по крайней мере в одном из последних двух реакторов, работающих согласно стадии (а), катализатор ароматизации контактирует с потоком низшего алкана, и по крайней мере в одном из последних двух реакторов, работающих согласно стадии (а), катализатор ароматизации контактирует с водородсодержащим газом. В другом варианте способ проводят по крайней мере в четырех реакторах, предпочтительно реакторах с неподвижным слоем, поставленных параллельно, и в любой момент времени по крайней мере один реактор работает согласно стадии способа (с), и по крайней мере три реактора работают согласно стадии(а), и по крайней мере в одном из последних трех реакторов, работающих согласно стадии (а), катализатор ароматизации контактирует с потоком низшего алкана, и по крайней мере в одном из последних трех реакторов, работающих согласно стадии (а), катализатор ароматизации контактирует с водородом. Краткое описание чертежей На фиг. 1 показан график, в котором сравнивают превращение этана, выход бензола и общий выход ароматических веществ, полученные в эксплуатационных испытаниях 1 и 2 и примере 1. На фиг. 2 показан график, в котором сравнивают общее превращение (этан + пропан), выход бензола и общий выход ароматических веществ, полученные в эксплуатационных испытаниях 3 и 4 и примере 2. На фиг. 3 показан график, в котором сравнивают превращение этана, выход бензола и общий выход ароматических веществ, полученные в эксплуатационных испытаниях 5 и 6 и примере 3. На фиг. 4 показан график, в котором сравнивают превращение этана, выход бензола и общий выход ароматических веществ, полученные в эксплуатационных испытаниях 5 и 7 и примере 3. Подробное описание изобретения В предпочтительной схеме работы/регенерации в соответствии с данным изобретением в любой момент времени большая часть параллельно расположенных реакторов с неподвижным слоем в данной установке подвергаются перемежающимся циклам (а) кратковременной (предпочтительно около 30 мин или менее, более предпочтительно около 20 мин или менее и наиболее предпочтительно около 10 мин или менее, но обычно не менее 1 мин) обработки потоком низшего алкана в подходящих условиях ароматизации низшего алкана; (b) кратковременной (предпочтительно около 30 мин или менее, более предпочтительно около 20 мин или менее и наиболее предпочтительно около 10 мин или менее, но обычно не менее 2 мин) десорбции горячим водородсодержащим газом для повторного нагревания слоя катализатора и снижения ухудшения эффективности катализатора через частичное удаление отложений нагара с поверхности. Расчет времени этих циклов таков, чтобы в любой момент времени по крайней мере один реактор в установке обрабатывал сырье и производил ароматические соединения все время и по крайней мере в одном реакторе производилась десорбция горячим водородсодержащим газом в любой момент времени. В то же время по крайней мере один из реакторов в установке полностью отключен для контролируемой регенерации сжиганием нагара и повторного распыления металла, и/или восстановления водородсодержащим газом, и/или сульфидирования, при необходимости. После завершения сжигания нагара реактор снова включают в работу для циклов реакции/десорбции, а другой из параллельно установленных реакторов, с отработанным катализатором, выключают для сжигания нагара. Эту схему используют до тех пор, пока все реакторы не будут подвергнуты сжиганию нагара, и затем повторяют. Таким образом, поддерживается непрерывное производство ароматических соединений с высоким выходом, несмотря на неотъемлемое быстрое коксование/деактивацию катализатора в условиях реакции ароматизации низшего алкана. Описанная выше схема работы/регенерации позволяет непрерывно производить бензол и другие ароматические соединения для низкозатратного сырья на основе низшего алкана при коммерчески целесообразных скоростях и выходах. Эта схема отвечает потребности в частой регенерации катализатора(удалении нагара) в процессе ароматизации низшего алкана таким образом, который позволяет продлить срок полезного использования применяемого катализатора или катализаторов. Чередование обработки сырья и десорбции горячим водородсодержащим газом в большинстве параллельных реакторов в любой момент времени снижает ухудшение эффективности катализатора в операционном цикле (время между сжиганием нагара). Такое снижение ухудшения эффективности катализатора увеличивает время до того момента, когда становится необходимым медленное, тщательно контролируемое сжигания нагара, что уменьшает необратимое повреждение катализатора. Срок полезного применения катализатора значительно дольше при применении способа в соответствии с данным изобретением, по сравнению с катализатором, который подвергается частому высокотемпературному сжиганию нагара между обработкой низшего алкана и условиями ароматизации. Десорбция закоксованных катализаторов горячим водородсодержащим газом практикуется коммерчески в течение десятилетий, и специалистам известны различные способы. Десорбция катализатора может проводиться в реакторе для ароматизации. Водородная десорбция может проводиться обработкой катализатора потоком, содержащим вплоть до 100% водорода при от около 400 до около 800 С, от около 0,01 до около 1,0 МПа и среднечасовой скорости подачи сырья (ССПС) от около 0,1 до около 5 ч-1. Регенерация закоксованных катализаторов также коммерчески практикуется в течение десятилетий,и специалистам в данной области техники известны различные способы регенерации. Регенерация катализатора может проводиться в реакторе для ароматизации. Например, катализатор может быть регенерирован сжиганием нагара при высокой температуре в присутствии кислородсодержащего газа, как описано в патенте США 4795845, который полностью включен в описание в качестве ссылки. Предпочтительная температура регенерации на стадии регенерации сжиганием нагара составляет от около 400 до около 700 С, более предпочтительно от около 400 до около 550 С. В способе регенерации сжиганием нагара, предпочтительном для применения в соответствии с данным изобретением, используют воздух или разбавленный азотом воздух под давлением от около 0,01 до около 1,0 МПа и от около 300 до около 2000 среднечасовой скорости подачи сырья (ССПС) и при исходной температуре ближе к низшей границе указанного выше предпочтительного интервала, которая непрерывно или постепенно повышается до достижения температуры около высшей границы указанного выше предпочтительного интервала. Необязательную стадию повторного диспергирования металла проводят оксихлорированием или обработкой раствором, содержащим один или более агентов для редиспергирования металла, или различными другими методами, известными в данной области техники. Методы повторного диспергирования металла коммерчески практикуются в течение десятилетий, и специалистам известны различные способы. Оксихлорирование является предпочтительным для большинства Pt-содержащих катализаторов, включая катализаторы для риформинга сырой нефти на подложке из окиси алюминия. Стадии, применяемые при регенерации катализатора риформинга сырой нефти, включая оксихлорирование, описаны в обзорной статье, озаглавленной "Catalyst Regeneration and Continuous Reforming Issues, by P.K. Doolin,D.J. Zalewski and S.O. Oyekan, на с. 433-457 книги Catalytic Naphtha Reforming, 2nd. Edition, edited byG.J. Antos and A.M. Aitani (published by Marcel Dekker, Inc., New York, 2004). Оксихлорирование предпочтительно проводят с применением смеси газов, содержащей воду, кислород, хлороводород и хлор и/или одной или более хлорорганических соединений, таких как тетрахлорэтилен, способных взаимодействовать с выделением хлора в условиях реакции оксихлорирования. Предпочтительно стадию оксихлорирования проводят при температуре от около 480 до около 520 С, при полной концентрации хлорсодержащих видов в газе от около 0,01 до 0,6 мол.%, содержании кислорода в газе от около 0,1 до около 20% моль, при парциальном давлении вплоть до около 25 фут/дюйм 2-полный. Однако необходимо отметить, и это хорошо известно специалистам в данной области техники, что изменения возможностей реакторного оборудования и металлургии и/или вопросов безопасности могут потребовать ограничить верхние пределы содержания соединения хлора и/или содержания кислорода, которые значительно ниже, чем те, которые даны здесь в некоторых случаях. Необязательную стадию восстановления, предпочтительно проводимую с применением водородсодержащего газа, коммерчески практикуют в течение десятилетий и специалистам известны различные способы, включая те, в которых применяются другие восстанавливающие газы, такие как окись углерода. Восстановление служит для целей восстановления металлического компонента катализатора до элементного металлического состояния и для того, чтобы обеспечивать относительно однородное диспергирование металла в подложке. Оно может проводиться согласно способу, описанному в патенте США 5106800, который полностью включен в описание в качестве ссылки, более конкретно, обработкой катализатора водородсодержащим газом со скоростью потока от около 500 до 6000 ССПС, давлении от около 0,05 до 1,0 МПа и температуре от около 450 до около 800 С. Сульфидирование является другой обработкой катализатора, которую много лет применяют для реактивации катализаторов. Оно служит для целей уменьшения активности катализатора для предотвращения избыточного гидрогенолиза и коксования. Оно может проводиться согласно способу, описанному в патенте США 5106800, который полностью включен в описание в качестве ссылки, более конкретно, обработкой восстановленного катализатора сульфидирующим газом, таким как смесь водорода и сульфида водорода и/или одного или более летучих сероорганических соединений, содержащих по крайней мере около 10 моль водорода на 1 моль сульфида водорода, более предпочтительно по крайней мере 50 моль водорода на 1 моль соединения(й) серы при температуре от около 200 до около 700 С. Подходящее сырье для ароматизации в соответствии с данным изобретением включает потоки алкана, которые могут содержать преимущественно один или более С 2-, С 3- и/или С 4-алканы (названные здесь "низшие алканы"), например потоки, насыщенные этаном/пропаном/бутаном, полученные из природного газа, потоков сырой или переработанной нефти, включая потоки отходов. Примеры потенциально подходящих потоков сырья включают (но не ограничены ими) остаточный этан и пропан после очистки природного газа (метана), чистые потоки этана, пропана и бутана (также известные как жидкие компоненты газа), полученные совместно в установке по сжижению природного газа, потоки С 2-С 5 из попутных газов, совместно полученных при производстве неочищенной нефти, "отработанные" потоки непрореагировавшего этана из паровых крекинг-установок, и поток побочного C1-C4 продукта из установок для риформинга сырой нефти. Сырье на основе низшего алкана может быть осторожно разбавлено относительно инертными газами, такими как азот, и/или различными легкими углеводородами, и/или незначительными количествами добавок, необходимых для улучшения эффективности катализатора. В одном варианте большая часть сырья состоит из этана и пропана. В другом варианте сырье состоит из смешанных С 2-С 4-алканов. Еще в одном варианте сырье состоит преимущественно из пропана и/или бутана. Сырье может содержать, в дополнение, другие углеводороды с открытой цепью, содержащие от 3 до 8 атомов углерода, в качестве сореагентов. Конкретные примеры таких дополнительных сореагентов включают пропилен, изобутан, н-бутены и изобутен. Сырье может содержать вплоть до около 20 мас.% С 2-С 4-олефинов, предпочтительно не более около 10 мас.% олефинов. Слишком большое содержание олефинов может вызывать образование неприемлемого количества нагара. Углеводородное сырье предпочтительно может содержать по крайней мере около 30 мас.% С 2-C4-углеводородов, предпочтительно по крайней мере около 50 мас.%. Данное изобретение является способом получения ароматических углеводородов, который включает контакт углеводородного сырья, содержащего низшие алканы, и, возможно, другие углеводороды, и композиции катализатора, подходящие для способствования реакции таких углеводородов с получением ароматических углеводородов, таких как бензол, при температуре от около 400 до около 700 С и давлении от около 0,01 до около 1,0 МПа абс. Среднечасовая скорость подачи сырья (ССПС) в час может варьироваться от около 300 до около 6000. Способ можно проводить одной стадией или во множество,предпочтительно две стадии. Если применяют двухстадийный способ, условия на каждой стадии могут попадать в указанные выше интервалы и могут быть одинаковыми или разными. В одном варианте сырье на основе низшего алкана содержит по крайней мере около 20 мас.%, пропана и около 20 мас.%, этана, и способ проводят в две стадии, как описано в находящейся на одновременном рассмотрении, принадлежащей тому же правообладателю, предварительной заявке на патент США 61/257085, озаглавленной "Способ превращения смешанных низших алканов в ароматические углеводороды", поданной 2 ноября 2009 г., которая полностью включена в описание в качестве ссылки. В другом варианте сырье содержит по крайней мере около 20 мас.% пропана и/или бутана, и способ проводят в две стадии. Способ включает:(a) подачу сырья на основе смешанного низшего алкана, содержащего, по крайней мере, пропан и этан или по крайней мере около 20 мас.% пропана и/или бутана, в реактор ароматизации;(b) попеременный контакт сырья на основе смешанного низшего алкана с катализатором ароматизации с первой стадии в реакторе в течение короткого периода времени, предпочтительно около 30 мин или менее, в условиях реакции первой стадии, которые максимизируют превращение пропана и/или любого другого высшего углеводорода, присутствующего в потоке, в продукты реакции ароматизации первой стадии, и затем контакт катализатора ароматизации первой стадии с водородсодержащим газом при повышенной температуре в течение короткого периода времени, предпочтительно около 30 мин или менее;(c) повтор цикла со стадии (b) по крайней мере один раз;(d) регенерацию катализатора ароматизации первой стадии через контакт с кислородсодержащим газом при повышенной температуре;(e) необязательную обработку регенерированного катализатора ароматизации первой стадии повторным диспергированием металла;(f) необязательное восстановление регенерированного катализатора ароматизации первой стадии предпочтительно водородсодержащим газом;(h) повтор стадий (а)-(g) по крайней мере один раз;(i) отделение продуктов первой ароматической реакции от непрореагировавшего и/или побочного этана;(j) попеременный контакт непрореагировавшего и/или побочного этана со стадии (i) с катализатором ароматизации со второй стадии в реакторе в течение короткого периода времени, предпочтительно около 30 мин или менее, в условиях реакции второй стадии, что максимизирует превращение этана в продукты ароматической реакции второй стадии, и затем контакт катализатора ароматизации второй стадии с водородсодержащим газом при повышенной температуре в течение короткого периода времени,предпочтительно около 30 мин или менее;(k) повтор цикла со стадии (j) по крайней мере один раз;(l) регенерацию катализатора ароматизации второй стадии через контакт с кислородсодержащим газом при повышенной температуре;(m) необязательное повторное диспергирование металла на регенерированный катализатор ароматизации второй стадии;(n) необязательное восстановление регенерированного катализатора ароматизации второй стадии,предпочтительно водородсодержащим газом;(р) повтор стадий (j)-(o) по крайней мере один раз. На первой стадии температура реакции предпочтительно варьируется от около 400 до около 650 С,наиболее предпочтительно от около 420 до около 650 С, и на второй стадии температура реакции предпочтительно варьируется от около 450 до около 680 С, наиболее предпочтительно от около 450 до около 660 С. Первичные желаемые продукты способа в соответствии с данным вариантом включают бензол,толуол и/или ксилол (BTK). В одном варианте условия реакции на первой стадии могут быть оптимизированы для превращения пропана и/или бутана в ароматические соединения. Необязательно, условия реакции на первой стадии также могут быть оптимизированы для превращения ароматических соединений любых высших углеводородов, которые могут присутствовать в сырье. В другом варианте условия реакции второй стадии могут быть оптимизированы для превращения этана в ароматические соединения. Необязательно, условия реакции второй стадии также могут быть оптимизированы для превращения вBTK любых других неароматических углеводородов, которые могут быть получены на первой стадии. Любой из множества катализаторов может применяться для способствования реакции превращения низших алканов в ароматические углеводороды. Один из таких катализаторов описан в патенте США 4899006, который полностью включен в описание в качестве ссылки. Описанная композиция катализаторов содержит алюмосиликат с отложенным на нем галлием и/или алюмосиликат, в котором катионы заменены ионами галлия. Молярное отношение двуокиси кремния к окиси алюминия составляет по крайней мере 5:1. Другой катализатор, который может применяться в способе в соответствии с данным изобретением,описан в ЕР 0244162. Этот катализатор содержит катализатор, описанный в предыдущем параграфе, и металл VIII группы, выбранный из родия и платины. Алюмосиликаты предпочтительно имеют структуру типа MFI или MEL и могут быть ZSM-5, ZSM-8, ZSM-11, ZSM-12 или ZSM-35. Другие катализаторы, которые могут применяться в способе в соответствии с данным изобретением, описаны в патентах США 7186871 и 7186872, оба которых полностью включены в описание в качестве ссылок. В первом из этих патентов описан содержащий платину ZSM-5 кристаллический цеолит,синтезированный получением цеолита, содержащего алюминий и кремний в матрице, нанесением платины на цеолит и спеканием цеолита. Во втором патенте описан такой катализатор, который содержит галлий в матрице и практически не содержит алюминий. Дополнительные катализаторы, которые могут применяться в способе в соответствии с данным изобретением, описаны в патенте США 5227557, который полностью включен в описание в качестве ссылки. Эти катализаторы содержат MFI цеолит плюс по крайней мере один благородный металл из семейства платины и по крайней мере один дополнительный металл, выбранный из группы, включающей олово, германий, свинец и индий. Один из предпочтительных катализаторов для применения в соответствии с данным изобретением описан в заявке на патент США 12/371787, поданной 16 февраля 2009 г., озаглавленной "Process forthe Conversion of Ethane to Aromatic Hydrocarbons". Эта заявка полностью включена в описание в качестве ссылки. В этой заявке описан катализатор, содержащий (1) от 0,005 до 0,1 мас.% платины в расчете на металл, предпочтительно от 0,01 до 0,05 мас.%; (2) количество смягчающего металла, выбранного из группы, включающей олово, свинец и германий, которое составляет не более 0,02 мас.% от количества платины, предпочтительно не более 0,2 мас.% от катализатора в расчете на металл; (3) от 10 до 99,9 мас.% алюмосиликата, предпочтительно цеолита, в расчете на алюмосиликат, предпочтительно от 30 до 99,9 мас.%, предпочтительно выбранного из группы, включающей ZSM-5, ZSM-11, ZSM-12,ZSM-23 или ZSM-35, предпочтительно превращенного в Н+ форму, предпочтительно имеющего молярное отношение SiO2/Al2O3 от 20:1 до 80:1; и (4) связующий агент, предпочтительно выбранный из двуокиси кремния, окиси алюминия и их смесей. Другой предпочтительный катализатор для применения в соответствии с данным изобретением описан в предварительной заявке на патент США 61/029939, поданной 20 февраля 2008 г., озаглавленной "Process for the Conversion of Ethane to Aromatic Hydrocarbons". Эта заявка полностью включена в описание в качестве ссылки. В заявке описан катализатор, содержащий (1) от 0,005 до 0,1 мас.% платины в расчете на металл, предпочтительно от 0,01 до 0,06 мас.%, наиболее предпочтительно от 0,01 до 0,05 мас.%; (2) количество железа, которое равно или больше количества платины, но не более 0,50 мас.% катализатора, предпочтительно не более 0,20 мас.% катализатора, наиболее предпочтительно не более 0,10 мас.% катализатора в расчете на металл; (3) от 10 до 99,9 мас.%, алюмосиликата, предпочтительно цеолита в расчете на алюмосиликат, предпочтительно от 30 до 99,9 мас.%, предпочтительно выбранного из группы, включающей ZSM-5, ZSM-11, ZSM-12, ZSM-23 или ZSM-35, предпочтительно превращенного в Н+ форму, предпочтительно имеющего молярное отношение SiO2/Al2O3 от 20:1 до 80:1; и (4) связующий агент, предпочтительно выбранный из двуокиси кремния, окиси алюминия и их смесей. Другой предпочтительный катализатор для применения в соответствии с данным изобретением описан в заявке на патент США 12/371803, поданной 16 февраля 2009 г., озаглавленной "Process forthe Conversion of Ethane to Aromatic Hydrocarbons". Эта заявка полностью включена в описание в качестве ссылки. В заявке описан катализатор, содержащий (1) от 0,005 до 0,1 мас.% платины в расчете на металл, предпочтительно от 0,01 до 0,05 мас.%, наиболее предпочтительно от 0,02 до 0,05 мас.%; (2) количество галлия, которое равно или больше количества платины, предпочтительно не более 1 мас.%, наиболее предпочтительно не более 0,5 мас.% в расчете на металл; (3) от 10 до 99,9 мас.% алюмосиликата,предпочтительно цеолита в расчете на алюмосиликат, предпочтительно от 30 до 99,9 мас.%, предпочтительно выбранного из группы, включающей ZSM-5, ZSM-11, ZSM-12, ZSM-23 или ZSM-35, предпочтительно превращенного в Н+ форму, предпочтительно имеющего молярное отношение SiO2/Al2O3 от 20:1 до 80:1; и (4) связующий агент, предпочтительно выбранный из двуокиси кремния, окиси алюминия и их смесей. Непрореагировавший метан и побочные углеводороды могут применяться на других стадиях, храниться и/или перерабатываться. Может быть необходимым охлаждать такие побочные продукты для их сжижения. Когда этан или смешанные низшие алканы получают на заводе по производству СПГ в результате очистки природного газа, по крайней мере, некоторые из этих поблочных продуктов могут быть охлаждены и сжижены с применением теплообменников, применяемых для сжижения очищенного природного газа (метана). Толуол и ксилол могут быть превращены в бензол гидродеалкилированием. Реакция гидродеалкилирования включает взаимодействие толуола, ксилола, этилбензола и высших ароматических соединений с водородом для отсоединения алкильных групп от ароматического кольца с получением дополнительного бензола и легких фракций, включая метан и этан, которые отделяют от бензола. Эта стадия значительно повышает общий выход бензола и, поэтому, очень предпочтительна. Тепловой и каталитический процессы гидродеалкилирования известны в данной области техники. Способы гидродеалкилирования описаны в опубликованной заявке на патент США 2009/0156870, которая полностью включена в описание в качестве ссылки. Интегрированный способ в соответствии с данным изобретением также может включать взаимодействие бензола с пропиленом с получением кумена который, в свою очередь, может быть превращен в фенол и/или ацетон. Пропилен может быть получен отдельно в аппарате по дегидрированию пропана,или может поступать из отходящих потоков процесса крекинга олефина или других источников. Способы взаимодействия бензола с пропиленом с получением кумена описаны в опубликованной заявке на патент США 2009/0156870, которая полностью включена в описание в качестве ссылки. Интегрированный способ в соответствии с данным изобретением также может включать взаимодействие бензола с другими олефинами, такими как этилен. Этилен может быть получен отдельно в аппарате дегидрирования этана или может поступать из отходящих потоков процесса крекинга олефина или других источников. Этилбензол является органическим химическим соединением, которое является ароматическим углеводородом. Его основным применением в нефтехимической промышленности является промежуточное соединение для производства стирола, который, в свою очередь, применяют для получения полистирола, широко применяемого пластикового материала. Способы взаимодействия бензола с этиленом с получением этилбензола описаны в опубликованной заявке на патент США 2009/0156870, которая полностью включена в описание в качестве ссылки. Затем стирол может быть получен дегидрированием этилбензола. Один из способов получения стирола описан в патенте США 4857498, который полностью включен в описание в качестве ссылки. Другой способ получения стирола описан в патенте США 7276636, который полностью включен в описание в качестве ссылки. Примеры Представленные ниже примеры предназначены только для иллюстративных целей и не должны рассматриваться как ограничивающие объем данного изобретения. Пример 1. Этот пример иллюстрирует один аспект схемы процесса ароматизации низшего алкана/регенерации катализатора в соответствии с данным изобретением. Более конкретно, в этом примере показано снижение падения эффективности катализатора и образования нагара через применение процесса с быстрой сменой циклов воздействия углеводородного сырья и стадий очистки горячим водородом, в противоположность непрерывному воздействию углеводородного сырья. Углеводородное сырье, применяемое для ароматизации в этом примере, состоит из 100% этана. Катализатор А получают из цилиндрических частиц экструдата диаметром 1,6 мм, содержащих 80 мас.% порошка цеолита ZSM-5 CBV 3014E (30:1 молярное соотношение SiO2/Al2O3, от Zeolyst International) и 20 мас.% связующего агента гамма-окиси алюминия. Образцы экструдата обжигают на воздухе вплоть до 650 С для удаления остаточной влаги перед применением для получения катализатора. Целевые загрузки металла для катализатора А составляют 0,025 мас.% Pt и 0,09 мас.% Ga. Металлы наносят на 25-100-граммовые образцы указанного выше экструдата ZSM-5/окиси алюминия, сначала объединяя подходящие количества исходных водных растворов тетраамина платины и нитрата галлия(III), разбавляя эту смесь деионизированной водой до объема, достаточного только для заполнения пор экструдата, и пропитывая экструдат этим раствором при комнатной температуре и атмосферном давлении. Пропитанные образцы выстаивают при комнатной температуре в течение 2-3 ч и затем сушат в течение ночи при 100 С. Образцы катализатора А, полученные, как описано выше, тестируют "как есть", не измельчая, в эксплуатационных испытаниях 1 и 2. Для каждого эксплуатационного испытания 15 см 3 партию свежего(предварительно не тестированного) катализатора загружают в кварцевую трубку (внутренний диаметр 1,40 см) и располагают в трехзонной печи, соединенной с автоматической системой подачи газа. Перед каждым эксплуатационным испытанием партию катализатора предварительно обрабатываютin situ при атмосферном давлении (приблизительно 0,1 МПа абс.) следующим образом:(a) обжигание на воздухе со скоростью приблизительно 60 л/ч, во время чего температура стенок реактора увеличивается от 25 до 510 С за 12 ч, выстаивают при 510 С в течение 4 ч, затем далее повышают от 510 до 621 С за 1 ч, затем выстаивают при 621 С в течение 30 мин;(b) продувают азотом со скоростью приблизительно 60 л/ч, 621 С, в течение 20 мин;(c) восстанавливают водородом в количестве 60 л/ч, 621 С, в течение 30 мин. Для эксплуатационного испытания 1 в конце указанной выше предварительной обработки поток водорода в реактор превращают и партию катализатора непрерывно обрабатывают потоком 100% этана при атмосферном давлении (около 0,1 МПа абс.), температуре стенок реактора 621 С и скорости потока 1000 ССПС (1000 см 3 сырья на 1 см 3 катализатора в час) в течение 13 ч. Для отслеживания изменений в эффективности катализатора во время указанного выше испытания берут образцы из общего выходящего из реактора потока и анализируют на встроенной системе хроматографического газоанализатора. Первый образец берут через 10 мин после введения потока этана. Затем образцы берут каждые 70 мин, всего 12 образцов во время испытания. На основании данных выходящей композиции, полученных газохроматографическим анализом, превращение этана рассчитывают по формуле: % превращения этана = 100 - мас.% этана в выходящем потоке. Выход на проход бензола и общее количество ароматических веществ даны в мас.% бензола и общего количества ароматических веществ соответственно в выходящем из реактора потоке. В конце 13-часового тестирования поток этана в реактор останавливают и водород повторно вводят со скоростью потока 60 л/ч. Печные нагреватели реактора выключают и катализатор охлаждают до около 38 С за приблизительно 8 ч. Для эксплуатационного испытания 2 в конце описанной выше предварительной обработки партию катализатора подвергают 157 циклам перемежающейся обработки потоком этана и водородом при атмосферном давлении (около 0,1 МПа) и температуре стенок реактора 621 С согласно следующему протоколу:(a) 5 мин 100% этанового сырья при 1000 ССПС;(b) 10 мин 100% водорода при 4000 ССПС. Общее суммарное время обработки катализатора потоком этана в данном режиме тестирования составляет 39,9 ч. Для отслеживания изменений в эффективности катализатора во время указанного выше эксплуатационного испытания 2 берут образцы из общего выходящего из реактора потока и анализируют в конце выбранных 5-минутных интервалов на встроенной системе хроматографического газоанализатора. Превращение этана, выход бензола на партию и общий выход ароматических веществ определяют так же,как в эксплуатационном испытании 2 выше. В конце тестирования поток этана в реактор останавливают, и водород повторно вводят со скоростью потока 60 л/ч. Печные нагреватели реактора выключают и катализатор охлаждают до около 38 С за приблизительно 8 ч. Данные превращения этана, выхода бензола и общего выхода ароматических соединений, полученные в эксплуатационном испытании 1 и 2, сравнивают на фиг. 1. Как показано на этой фигуре, потеря уровня превращения этана, выхода бензола и общего выхода, демонстрируемые катализатором, были значительно больше во время 13-часовой непрерывной обработки потоком этана (эксплуатационное испытание 1), чем во время 13,3 ч суммарной обработки потоком этана в циклическом рабочем режиме сырье/водород, применяемом в эксплуатационном испытании 2. В соответствии с этими результатами уровни нагара (углерода), определенные ASTM Method D5291 на образцах израсходованного катализатора из эксплуатационных примеров 1 и 2, составляют 12,2 и 7,6 мас.% соответственно. Пример 2. Этот пример иллюстрирует один аспект схемы процесса ароматизации низшего алкана/регенерации катализатора в соответствии с данным изобретением. Более конкретно, в этом примере показано снижение падения эффективности катализатора и образования нагара через применение процесса с быстрой сменой циклов воздействия углеводородного сырья и стадий очистки горячим водородом, в противоположность непрерывному воздействию углеводородного сырья. Углеводородное сырье, применяемое для ароматизации в этом примере, состоит из 50% этана и 50% пропана. Катализатор В получают из цилиндрических частиц экструдата диаметром 1,6 мм, содержащих 80 мас.%, порошка цеолита ZSM-5 CBV 2314E (23:1 молярное соотношение SiO2/Al2O3, от ZeolystInternational) и 20 мас.% связующего агента гамма-окиси алюминия. Образцы экструдата обжигают на воздухе вплоть до 650 С для удаления остаточной влаги перед применением для получения катализатора. Целевые загрузки металла для катализатора В составляют 0,025 мас.% Pt и 0,09 мас.% Ga. Катализатор В, полученный как описано выше, тестируют "как есть", не измельчая, в эксплуатационных испытаниях 3 и 4. Для каждого эксплуатационного испытания 15 см 3 партию свежего (предварительно не тестированного) катализатора загружают в кварцевую трубку (внутренний диаметр 1,40 см) и располагают в трехзонной печи, соединенной с автоматической системой подачи газа. Перед каждым эксплуатационным испытанием партию катализатора предварительно обрабатываютin situ при атмосферном давлении (приблизительно 0,1 МПа абс.) следующим образом:(a) обжигание на воздухе со скоростью приблизительно 60 л/ч, во время чего температура стенок реактора увеличивается от 25 до 510 С за 12 ч, выстаивают при 510 С в течение 4 ч, затем далее повышают от 510 до 600 С за 1 ч, затем выстаивают при 600 С в течение 30 мин;(b) продувают азотом со скоростью приблизительно 60 л/ч, 600 С, в течение 20 мин;(c) восстанавливают водородом в количестве 60 л/ч, 600 С, в течение 30 мин. Для эксплуатационного испытания 3 в конце указанной выше предварительной обработки поток водорода в реактор прекращают и партию катализатора непрерывно обрабатывают потоком, состоящим из 50% этана и 50% пропана при атмосферном давлении (около 0,1 МПа абс.), температуре стенок реактора 600 С и скорости потока 1000 ССПС (1000 см 3 сырья на 1 см 3 катализатора в час) в течение 26 ч. Для отслеживания изменений в эффективности катализатора во время указанного выше испытания берут образцы из общего выходящего из реактора потока и анализируют на встроенной системе хроматографического газоанализатора. Первый образец берут через 10 мин после введения потока этана/пропана. Затем образцы берут в выбранные интервалы времени в течение оставшегося времени тестирования. На основании данных выходящей композиции, полученных газохроматографическим анализом,превращение углеводородного сырья рассчитывают по формулам: Превращение этана, % = 100(мас.% этана в сырье - мас.% этана в выходящем потоке)/(мас.% этана в сырье),Превращение пропана, % = 100(мас.% пропана в сырье - мас.% пропана в выходящем потоке)/(мас.% пропана в сырье),Общее превращение этана + пропана = мас.% этана в сырье% превращения этана) + (мас.% пропана в сырье% превращения/100. В конце тестирования поток этана/пропана в реактор останавливают и водород повторно вводят со скоростью потока 60 л/ч. Печные нагреватели реактора выключают и катализатор охлаждают до около 38 С за приблизительно 8 ч. Для эксплуатационного испытания 4 в конце описанной выше предварительной обработки партию катализатора подвергают 155 циклам перемежающейся обработки 50/50 (мас./мас.) потоком этана/пропана и водородом при атмосферном давлении (около 0,1 МПа) и температуре стенок реактора 600 С согласно следующему протоколу:(b) 20 мин 100% водорода при 4000 ССПС. Общее суммарное время обработки катализатора потоком этана в данном режиме тестирования составляет 26 ч. Общее время для 155 циклов обработки этановым/пропановым сырьем и водородом, как описано выше, составляет 78 ч. Для отслеживания изменений в эффективности катализатора во время указанного выше эксплуатационного испытания 4 берут образцы из общего выходящего из реактора потока и анализируют в конце выбранных 10-минутных циклов обработки этаном/пропаном на встроенной системе хроматографического газоанализатора. Превращение этана, превращение пропана, общее превращение углеводородов, выход бензола на партию и общий выход ароматических веществ на партию определяют так же, как в эксплуатационном испытании 3 выше. В конце тестирования поток этана/пропана в реактор останавливают и водород повторно вводят со скоростью потока 60 л/ч. Печные нагреватели реактора выключают и катализатор охлаждают до около 38 С за приблизительно 8 ч. Данные общего превращения сырья, выхода бензола и общего выхода ароматических соединений,полученные в эксплуатационном испытании 3 и 4, сравнивают на фиг. 2. Как показано на этой фигуре,потеря уровня превращения сырья, выхода бензола и общего выхода, демонстрируемые катализатором,были значительно больше во время 26-часовой непрерывной обработки потоком углеводородов (эксплуатационное испытание 3), чем во время 26 ч суммарной обработки потоком углеводородов в циклическом рабочем режиме сырье/водород, применяемом в эксплуатационном испытании 4. В соответствии с этими результатами уровни нагара (углерода), определенные ASTM Method D5291 на образцах израсходованного катализатора из эксплуатационных примеров 3 и 4, составляют 13,9 и 8,3 мас.% соответственно. Пример 3. В этом примере одну партию катализатора применяют в последовательно проводящихся тестах,применяющих режим обработки углеводородным сырьем/очистки водородом (как описано в примерах 1 и 2) и методики регенерации катализатора, включающие только сжигание нагара или сжигание нагара с последующим оксихлорированием. В этом примере иллюстрируются возможные операционные последовательности, которые могут применяться в реакторе ароматизации чистого низшего алкана в способе в соответствии с данным изобретением. Углеводородное сырье, применяемое для ароматизации в этом примере, состоит из 100% этана. В эксплуатационном испытании 5, 15 см 3 свежего катализатора А (см. пример 1) тестируют при быстрой смене циклов 100% этанового сырья и очистки водородом в тех же условиях и по той же методике,которые описаны в эксплуатационном испытании 2, описанном выше в примере 1. Общее суммарное время обработки потоком этана составляет 13,3 ч, и общее время тестирования составляет 39,9 ч. В конце тестирования поток этана в реактор останавливают, повторно вводят водород со скоростью потока 60 л/ч и температуру стенок реактора снижают от 621 до около 204 С за 5 ч. Затем реактор продувают азотом при атмосферном давлении (около 0,1 МПа) со скоростью потока 60 л/ч в течение 20 мин, в препарате для сжигания нагара применяют воздух. После стадии продувания азотом поток в реактор снижают до 10 л/ч воздуха при атмосферном давлении. Температуру стенок реактора повышают от около 204 до 427 С за 5 ч, выдерживают при 427 С в течение 1,5 ч, повышают с 427 до 482 С за 1 ч, выдерживают при 482 С в течение 1,5 ч, повышают от 482 до 510 С за 1 ч, выдерживают при 510 С в течение 4 ч и затем реактор охлаждают до температуры окружающей среды. Эксплуатационное испытание 6 проводят по методике эксплуатационного испытания 5, применяя уже использованный, с сожженным нагаром, катализатор А из эксплуатационного испытания 5. После завершения эксплуатационного испытания 6 партию катализатора подвергают второму сжиганию нагара в воздухе по методике, которую применяли в конце эксплуатационного испытания 5. После второго сжигания использованный катализатор А подвергают оксихлорированию. Для этой обработки 15 см 3 использованного катализатора загружают в кварцевую трубку (внутренний диаметр 1,40 см) и располагают в трехзонной печи и подключают к системе потока газа. Поток азота 30 л/ч устанавливают при атмосферном давлении (около 0,1 МПа) и катализатор нагревают от комнатной температуры до 500 С за 2 ч. После достижения температуры 500 С газ, проходящий через слой катализатора при атмосферном давлении, меняют с 30 л/ч азота на 30 л/ч смеси газов со следующей композицией: около 1,8-2,0 мол.% кислорода, около 1,8-2,0 мол.% воды, около 0,8-1,0 мол.% хлороводорода, около 0,2-0,3 мол.% хлора, азот до полного. Через 3 ч обработки этой смесью газов газ,проходящей через катализатор, меняют на 30 л/ч смеси, состоящей из около 1,8-2,0 мол.% кислорода,1,8-2,0 мол.% воды, азота до полного, в течение 3 ч. В конце 3-часового периода поток газа через катализатор меняют на 30 л/ч воздуха при атмосферном давлении и слой катализатора охлаждают до температуры окружающей среды. Эксплуатационное испытание 7 проводят по методике эксплуатационного испытания 5 с применением 15 см 3 партии катализатора А, который подвергают оксихлорированию, описанному выше. Данные превращения этана, выхода бензола и общего выхода ароматических соединений, полученные в эксплуатационном испытании 5 и 6 сравнивают на фиг. 3. Среднее превращение этана и общий выход ароматических соединений, демонстрируемые регенерированным катализатором в эксплуатационном испытании 6, составляют около 93% от соответствующих значений для свежего катализатора в эксплуатационном испытании 5. Средний выход бензола, демонстрируемый регенерированным катализатором в эксплуатационном испытании 6, составляет около 97% от соответствующих значений для свежего катализатора в эксплуатационном испытании 5. Данные превращения этана, выхода бензола и общего выхода ароматических соединений, полученные в эксплуатационном испытании 5 и 7, сравнивают на фиг. 4. Среднее превращение этана и общий выход ароматических соединений, демонстрируемые регенерированным катализатором в эксплуатационном испытании 7, составляют около 95% от соответствующих значений для свежего катализатора в эксплуатационном испытании 5. Средний выход ароматических соединений и бензола, демонстрируемый регенерированным катализатором в эксплуатационном испытании 7, составляет около 97 и 100% соответственно от соответствующих значений для свежего катализатора в эксплуатационном испытании 5. Пример 4. На основании данных примеров 1 и 3 в этих примерах обрисована возможная схема процесса ароматизации низшего алкана с применением множества параллельных реакторов с неподвижным слоем в соответствии с данным изобретением. Углеводородное сырье, применяемое в этом примере, представляет собой 100% этан. В этом примере пять параллельных реакторов с неподвижным слоем работают циклами, длящимися приблизительно 60 ч каждый. Во время каждого 6-часового цикла каждый отдельный реактор работает в следующих двух режимах:(a) около 36 ч в режиме "сырье/Н 2", в котором катализатор подвергают быстрым циклам воздействия углеводородного сырья (около 5 мин) и водорода (около 10 мин), как описано в эксплуатационном испытании 2 (см. пример 1);(b) около 24 ч в режиме "реген", в котором катализатор подвергают сжиганию нагара (такому, как описано в примере 3), необязательному оксихлорированию или стадии нанесения другого металла (такому, как описано в примере 3) и (при необходимости) короткой стадии восстановления водородом препарата, который возвращают обратно в режим "сырье/H2". Время для каждого отдельного реактора, составляющее 60 ч рабочего цикла, совмещают таким образом, чтобы во время любого 12-часового периода в общем 60-часовом цикле три из пяти параллельных реакторов находятся в режиме работы "сырье/H2", а два других реактора находятся в режиме "реген". Такая совмещенная временная схема для системы из пяти реакторов показана в табл. 1. Во время каждого 12-часового периода в общем 60-часовом цикле время стадий обработки сырья и очистки водородом в каждом из трех работающих (не регенерирующихся) реакторах совмещают так,чтобы во время любого 15-минутного периода в 12-часовом интервале один реактор находился в режиме обработки углеводородного сырья для производства бензола и других ароматических веществ, а два других реактора - в режиме очистки водородом. Такая схема временного совмещения для трех параллельных работающих реакторов во время каждого 15-минутного интервала показана в табл. 2. Совмещенная циклическая схема работы, суммированная в табл. 1 и 2, получение ароматических соединений из низшего алкана может происходить непрерывно через свежий или свежерегерированный катализатор, хотя все равно существует необходимость в частой регенерации катализатора для сохранения общей эффективности. Пример 5. На основании данных из примеров 2 и 3 в этом примере обрисована возможная схема процесса ароматизации низшего алкана с применением множества параллельных реакторов с неподвижным слоем в соответствии с данным изобретением. Углеводородное сырье, применяемое в этом примере, представляет собой 100 мас.% этана и 50 мас.% пропана. В этом примере четыре параллельных реактора с неподвижным слоем работают циклами, длящимися приблизительно 96 ч (4 дня) каждый. Во время каждого 4-дневного цикла каждый отдельный реактор работает в следующих двух режимах:(a) около 3 дней (72 ч) в режиме "сырье/H2", в котором катализатор подвергают быстрым циклам воздействия углеводородного сырья (около 10 мин) и водорода (около 20 мин), как описано в эксплуатационном испытании 4 (см. пример 2);(b) около 1 дня (24 ч) в режиме "реген", в котором катализатор подвергают сжиганию нагара (такому, как описано в примере 3), необязательному оксихлорированию или стадии нанесения другого металла (такому, как описано в примере 3) и (при необходимости) короткой стадии восстановления водородом препарата, который возвращают обратно в режим "сырье/H2". Время для каждого отдельного реактора, составляющее 4 ч рабочего цикла, совмещают таким образом, чтобы во время любого 1-дневого периода в общем 4-дневном цикле три из четырех параллельных реакторов находятся в режиме работы "сырье/Н 2", а два других реактора находятся в режиме "реген". Такая совмещенная временная схема для системы из пяти реакторов показана в табл. 3. Во время каждого 24-часового периода в общем 96-часовом цикле время стадий обработки сырья и очистки водородом в каждом из трех работающих (не регенерирующихся) реакторах совмещают так,чтобы во время любого 30-минутного периода в 24-часовом интервале один реактор находился в режиме обработки углеводородного сырья для производства бензола и других ароматических веществ, а два других реактора - в режиме очистки водородом. Такая схема временного совмещения для трех параллельных работающих реакторов во время каждого 30-минутного интервала показана в табл. 4. Совмещенная циклическая схема работы, суммированная в табл. 3 и 4, получение ароматических соединений из низшего алкана может происходить непрерывно через свежий или свежерегерированный катализатор, хотя все равно существует необходимость в частой регенерации катализатора для сохранения общей эффективности. Таблица 1 ФОРМУЛА ИЗОБРЕТЕНИЯ 1. Способ получения ароматических углеводородов, который включает:(a) контакт сырья на основе низшего алкана с катализатором ароматизации в условиях реакции ароматизации в реакторе в течение периода времени, составляющего 30 мин или менее, с получением продуктов реакции ароматизации и затем контакт катализатора ароматизации с водородсодержащим газом при повышенной температуре в течение периода времени, составляющего 30 мин или менее;(b) повтор стадии (а) по крайней мере один раз;(c) регенерацию катализатора ароматизации через контакт с кислородсодержащим газом при повышенной температуре;(g) повтор стадий (а)-(с) по крайней мере один раз. 2. Способ по п.1, где на стадии (а) сырье на основе низшего алкана приводят в контакт с катализатором ароматизации в течение периода времени, составляющего 20 мин или менее, предпочтительно 10 мин или менее. 3. Способ по п.1 или 2, где на стадии (а) катализатор ароматизации приводят в контакт с водородсодержащим газом в течение периода времени, составляющего 20 мин или менее, предпочтительно 10 мин или менее. 4. Способ по пп.1-3, где способ проводят по крайней мере в трех реакторах, установленных параллельно, и по крайней мере один реактор работает в режиме стадии (с), и по крайней мере два реактора работают в режиме стадии (а), и по крайней мере в одном реакторе по крайней мере из двух реакторов,работающих в режиме стадии (а), катализатор ароматизации контактирует с сырьем на основе низшего алкана, и по крайней мере в одном по крайней мере из двух реакторов, работающих в режиме стадии (а),катализатор ароматизации контактирует с водородом. 5. Способ по пп.1-4, где способ проводят по крайней мере в четырех реакторах, поставленных параллельно, и по крайней мере один реактор работает в режиме стадии (с), и по крайней мере три реактора работают в режиме стадии (а), и по крайней мере в одном из последних по крайней мере трех реакторов,работающих в режиме стадии (а), катализатор ароматизации контактирует с сырьем на основе низшего алкана, и по крайней мере в одном из последних по крайней мере трех реакторов, работающих в режиме стадии (а), катализатор ароматизации контактирует с водородсодержащим газом. 6. Способ по пп.1-5, где стадию (а) проводят при 400-700 С, давлении 0,01-1,0 МПа и среднечасовой скорости подачи сырья 300-6000 ч-1. 7. Способ по пп.1-6, где стадию (с) проводят при 400-700 С, предпочтительно 400-550 С. 8. Способ по пп.1-7, где кислородсодержащим газом на стадии (с) является воздух. 9. Способ по пп.1-8, где после стадии (с) регенерированный катализатор подвергают повторному нанесению металла, предпочтительно оксихлорированием. 10. Способ по пп.1-9, где после стадии (с) регенерированный катализатор восстанавливают предпочтительно водородсодержащим газом. 11. Способ по пп.1-10, где после стадии (с) регенированный катализатор сульфидируют. 12. Способ получения ароматических углеводородов, который включает:(a) подачу сырья на основе низшего алкана, содержащего, по крайней мере, пропан и этан или пропан и/или бутан;(b) контакт сырья на основе низшего алкана с катализатором ароматизации первой стадии в реакторе в течение периода времени, составляющего 30 мин или менее, в условиях реакции первой стадии, которые максимизируют превращение пропана и/или любого другого высшего углеводорода, присутствующего в потоке, в продукты реакции ароматизации первой стадии и затем контакт катализатора ароматизации первой стадии с водородсодержащим газом при повышенной температуре в течение периода времени, составляющего 30 мин;(c) повтор стадии (b) по крайней мере один раз;(d) регенерацию катализатора ароматизации первой стадии через контакт с кислородсодержащим газом при повышенной температуре;(h) повтор стадий (а)-(d) по крайней мере один раз;(i) отделение продуктов первой ароматической реакции от непрореагировавшего и/или побочного этана;(j) контакт непрореагировавшего и/или побочного этана со стадии (i) с катализатором ароматизации со второй стадии в реакторе в течение периода времени, составляющего 30 мин или менее, в условиях реакции второй стадии, что максимизирует превращение этана в продукты ароматической реакции второй стадии, и затем контакт катализатора ароматизации второй стадии с водородсодержащим газом при повышенной температуре в течение периода времени, составляющего 30 мин или менее;(k) повтор стадии (j) по крайней мере один раз;(l) регенерацию катализатора ароматизации второй стадии через контакт с кислородсодержащим газом при повышенной температуре;(р) повтор стадий (j)-(l) по крайней мере один раз. 13. Способ по п.12, где на стадии (b) сырье на основе низшего алкана приводят в контакт с катализатором ароматизации первой стадии в течение периода времени, составляющего 20 мин или менее,предпочтительно 10 мин или менее. 14. Способ по пп.12 и 13, где на стадии (b) катализатор ароматизации первой стадии приводят в контакт с водородсодержащим газом в течение периода времени, составляющего 20 мин или менее,предпочтительно 10 мин или менее. 15. Способ по пп.12-14, где на стадии (j) непрореагировавший и/или побочный этан со стадии (i) приводят в контакт с катализатором ароматизации второй стадии в течение периода времени, составляющего 20 мин или менее, предпочтительно 10 мин или менее. 16. Способ по пп.12-15, где на стадии (j) катализатор ароматизации второй стадии приводят в контакт с водородсодержащим газом в течение периода времени, составляющего 20 мин или менее, предпочтительно 10 мин или менее.
МПК / Метки
МПК: C07C 15/00
Метки: ароматические, превращения, способ, углеводороды, алканов, низших
Код ссылки
<a href="https://eas.patents.su/15-22683-sposob-prevrashheniya-nizshih-alkanov-v-aromaticheskie-uglevodorody.html" rel="bookmark" title="База патентов Евразийского Союза">Способ превращения низших алканов в ароматические углеводороды</a>
Предыдущий патент: Оценка уровня помех и избыточного тока в линии электропередачи
Следующий патент: Система быстрого контактного охлаждения сжимаемого контейнера с напитком в системе раздачи напитков
Случайный патент: Импульсный модулятор с формирователем ступенчатого напряжения